Reactive acrylics are well-established structural adhesives in a wide range of industries and compete with adhesives like epoxies and polyurethanes. They are also called tough acrylics, toughened acrylics or second-generation acrylics (SGAs). However, these adhesives have never achieved the market penetration that many people anticipated. There are several reasons for the lack of acceptance: a limited number of suppliers, artificial high pricing and lack of widespread availability of raw materials, notably sources of good activators.
Several events indicate that significant growth may be expected for SGAs:
· Key patents have expired or will expire shortly,
· Greater availability of raw materials,
· Dispersion of technical knowledge, and
· Technical advancements in adhesives.
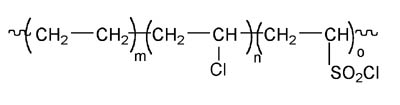
Background
Reactive acrylic adhesives have been around since the early 1970s when DuPont announced a family of patented adhesives based on solutions of its Hypalon[1]chlorosulfonated polyethylene rubber. (See Figure 1.)They comprised essentially Hypalon rubber dissolved in methyl methacrylate monomer with a peroxide or hydroperoxide initiator. They were cured using an activator second-component, which was a crude mixture of dihydropyridines known as DuPont 808 that was prepared from the condensation of butyraldehyde with aniline.
The activator and adhesive could be applied separately on the two surfaces to be bonded or laid on top of each other, prior to assembly. Compared to other two-component adhesives such as epoxies, the mix ratio of adhesive and activator was not critical.
The adhesives were found to be outstanding at bonding unprepared or oily metals with fixture times varying from about one minute to several minutes. They were also tough adhesives with high impact and peel strengths because of the rubber component. Table 1 shows the traditional advantages and disadvantages of the adhesives.
Reactive acrylics are true structural adhesives with a wide range of applications. Applications include fiberglass and sheet-steel bonding, magnets, loudspeakers, sporting goods, and miscellaneous metal and plastics assembly, particularly when fast curing with no surface preparation is desired.

Patent Expiration
The early patents of DuPont, Loctite and others appeared in the 1970s and early ‘80s, and have expired. A further series of patents, mainly by Illinois Tool Works, appeared in the 1980s and have expired or will expire shortly.DuPont originally licensed its technology to a small number of companies and collected substantial license fees on sales of the adhesives. This created a situation where:
• Prices of the adhesives were kept higher than normal market forces would dictate.
• Companies initiated research work to “get around the patents.”
• The adhesives did not penetrate many application areas where high volumes were used and low prices were essential.

Greater Availability of Raw Materials
The two major ingredients in reactive acrylic adhesives are the monomer and the rubber toughener. Reactive acrylics are based mainly on monofunctional monomers, e.g., methyl methacrylate or cyclohexyl methacrylate. The most widely used monomer, methyl methacrylate, is very inexpensive (less than $1/lb), and many other low-cost monomers are now widely available from several suppliers, often manufactured predominantly for coatings applications. Chlorosulfonated polyethylene rubbers have a more limited availability (two suppliers: DuPont Dow Elastomers and Tosoh Corp.) but only cost $2-$3/lb. Thus, there is no reason for high adhesive prices based on raw material costs.Dennis Damico of Lord Corp. in a review article on acrylic adhesives[2] stated that “ …..some of the key raw materials, most notably the amine-aldehyde accelerator, have limited availability, which interferes with the ability of manufacturers to supply product consistently.”
However, Reilly Industries has recently announced the global availability of Reilly PDHP Adhesive Activator[3]. This is a highly purified form of dihydropyridine activator, which contains 85 to 90 percent of the key active ingredient 3,5-diethyl-1,2-dihydro-1-phenyl-2-propylpyridine shown in Figure 2. The activator was originally developed by Reilly in collaboration with Loctite and is the subject of an expired patent[4].
According to Reilly Industries, the high assay of this activator (85 to 90 percent pure compared to 40 percent or less for earlier impure versions of dihydropyridines) gives the following benefits:
• Much higher and consistent bond strengths;
• Very low odor;
• Very low color, leading to colorless bond lines;
• High stability in monomers, thus allowing the formulation of stable two-part systems;
• Non-slip systems – does not contain oily impurities, which cause the adhesive to slip or “skate” across the surface of the activator;
• Very low residual aniline content (less than 0.05 percent), which allows it to meet strict new European safety directives such as CHIP-3 regulations in the UK[5].
Dispersion of Technical Knowledge
Several inventors and formulators of reactive acrylic adhesives have changed companies and continents over the years. The ITW Plexus line of reactive acrylics was developed using expertise of an inventor on the original DuPont patents. The inventor has subsequently transferred to IPS Weld-On. Several ex-Loctite people have founded their own companies or joined other companies in Europe and North America.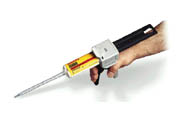
Technical Advancements In Adhesives
One major benefit of most types of reactive acrylics is the ability to be formulated to give adhesives that have a well-defined induction time after contact of the adhesive and activator where no obvious thickening or curing takes place, followed by a very rapid fixturing and full cure of the adhesive. Recent developments have given adhesives with induction times of two or three hours, allowing the assembly of large, complex structures such as in boat manufacturing.Reactive acrylics have also evolved from surface-activated systems to two-component mixable systems, which can cure through large gaps. The widespread availability of two-component syringes and cartridges has assisted these developments.
The odor and flammability of methyl methacrylate monomer is a concern to some customers, although companies like ITW Plexus have been very successful in marketing these adhesives to the automotive industry, particularly for bonding olefin-based substrates like automotive bumpers. Low-volatile versions were introduced, initially by Henkel Loctite, using higher-molecular-weight monomers such as tetrahydrofurfural methacrylate or cyclohexyl methacrylate.
Although the low-volatile versions did not develop the same strength as the methyl methacrylate-based ones, they were faster curing and very versatile in bonding a very wide range of materials. These “consumer-friendly,” low-volatile products were introduced into the consumer market in the 1980s as Loctite Depend in the United States and Multibond in Europe, and positioned as easy-to-use instant adhesives, without the skin-bonding negative of cyanoacrylates or the slow-curing and difficult-to-mix nature of epoxies. However, they seem to have disappeared from the consumer marketplace as Henkel Loctite has focused its efforts on other core technologies like cyanoacrylates. ITW Plexus also offers a low-volatile range of products for the industrial market.
A major technical breakthrough occurred when 3M recently introduced two-part reactive acrylics that can bond many low-surface-energy plastics, including many grades of polypropylene, polyethylene and thermoplastic polyolefins without special surface preparation. These adhesives have one component comprising an amine-complexed organoborane initiator, which is extended with a polyester adipamide, and a second component comprising a toughened methacrylate-monomer system. The major limitation of the 3M adhesives appears to be their cure time, with time to reach handling strength being two to three hours at room temperature and full cure in eight to 24 hours – although heat can accelerate the reactions. We understand that research is under way to improve the cure speed.
Researchers at Henkel Loctite have recently shown that, by adding activators to common cutting oils, reactive acrylics can be cured by metal surfaces on components fabricated using these lubricants[6]. This makes the adhesives essentially one-component systems.
The major manufacturers of reactive acrylics are Henkel Loctite, ITW Plexus, Lord Corp. and Dymax, although as key patents are expiring, other companies are entering the field.
No company has established very strong brand recognition in reactive acrylics, and we forecast that many companies will start manufacturing these adhesives in the future and that the business will become similar to the epoxy-adhesive industry with a lot of formulators. With the restrictions of licensing agreements removed and more competition, a lowering of market prices should lead to large growth opportunities in large-area bonding where polyurethanes and epoxies currently dominate. It is worth noting that Vantico (formerly Ciba Geigy Formulated Systems), the inventors of epoxy adhesives, has recently acquired a line of reactive acrylics.
References:
1. Hypalon is now a registered trademark of DuPont Dow Elastomers.2. D.J. Damico, Engineered Materials Handbook, Volume 3, 119 ASM International, 1990.
3. PDHP Adhesive Activator from Reilly Industries, http://www.reillyind.com.
4. D.P. Melody, S.M. Grant, and F.R. Martin; inventors. Loctite Corp. assignee; US Patent 4,450,030, 1984.
5. CHIP-3 is Version 3 of the UK Chemicals Hazard Information & Packaging for Supply Regulations, effective July 1, 2002, and implements the European Commission Dangerous Preparations Directive (1999/45/EC).
6. S. Morrill, J. Woods and T. LaBelle, 26th Annual Meeting of the Adhesion Society, Myrtle Beach, S.C., February 2003.