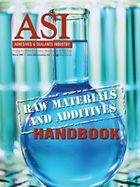
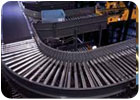
A variety of material handling options - from conveying to palletizing, depalletizing, sortation, storage and retrieval - can save significant time and money, prevent accidents in the manufacturing and distribution process, and improve product consistency and quality. Choosing from these options, or even choosing whether to automate at all, can be as tricky as developing a winning formula.
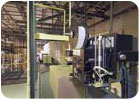
The Basics
Many factors go into deciding whether an operation is a candidate for automated material handling. From the vantage point of a material-handling specialist, we suggest asking two very basic questions.- Is the product you want to handle in a container, such as a drum, carton or pail?
- Is that container conveyable, i.e., does it have at least one flat surface or a solid side or frame? (Even oddly shaped items can usually be conveyed by palletizing, first with a robot or another mechanism, and then conveying them by pallet.)
If the adhesive or sealant is in a sealed container, then the situation is likely to be safe and viable for automated material handling. Some containers may require a non-corrosive equipment surface, such as stainless steel, but automated systems can generally be designed to work in any environment that is suitable for manual material handling.
Establishing Business Goals
Once you've determined that it's possible to automate your material-handling operation, the next step is to decide whether automation makes sense for your business.The following questions should be addressed.
- Can your factory floor and warehouse space accommodate a material-handling system?
- How will the benefits of automation - increased speed, accuracy, and efficiency - improve your operation?
- Are there worker safety or ergonomic factors that need to be considered?

How Automated Systems Work
Automating material handling can produce results as simple as reducing forklift hours or as dramatic as improving the logistics of an antiquated or expensive material-storage system.A pail destined to be filled with an adhesive serves as a good example to demonstrate the many possibilities that automation affords. In an automated material-handling system, a motorized roller conveyor delivers the pail to a process machine, where it is filled and capped. From there, the conveyor carries it to a robotic palletizer that stacks the pails on a pallet.
There are several possibilities once the pail is on a pallet. For example, the pallet could be automatically conveyed by a pallet conveyor through a stretch-wrapper and into a warehouse area. If the pallet needs to be stored, it could be moved by an automated storage-and-retrieval crane into a racking system, to be retrieved by the crane later and moved by conveyor to shipping. If floor space is in short supply, or if a conveying line cannot cross a floor production line, it might prove beneficial to move the pails or pallets overhead. Additionally, if improved inventory tracking or order fulfillment accuracy is important, integrated material-handling software can be added to the automated solution.
Return on Investment
Calculating the potential payback on a material-handling investment requires careful analysis of how well a proposed system increases efficiencies in a company's business operation.An automated system should:
- Reduce manual handling sufficiently to justify the cost of an upgrade.
- Reduce machine or labor downtime, especially if manual handling of materials is interfering with production or adding to production costs.
- Decrease accidents, staffing and liability problems.
- Eliminate handling practices that diminish product quality.
The flexibility of a material-handling solution can also give an operation room to grow. While a manual processes may meet today's needs, the next big order could require capacity that isn't available and that would be difficult to add. Automated systems can be designed to include plenty of room to grow, and that ability to grow may help companies to determine whether automation is a good fit.

Choosing a Qualified Solutions Provider
If your company is considering an automated material-handling solution, the first step is to partner with an experienced company that has developed systems for similar manufacturers or distributors and that has a track record of systems experience in general industry. A breadth of experience, coupled with direct knowledge of adhesives and sealants companies, gives a material-handling supplier a thorough base to design the most efficient system at the lowest cost, the lowest risk, and the highest ROI.An experienced and qualified material-handling systems provider will do the following.
- Evaluate the current throughput needs on your factory floor.
- Determine what type of automated material-handling system makes the most sense for the amount of open floor space you have.
- Determine how storage capacity can be maximized.
- Calculate how much downtime is incurred because manual handling is slowing down or halting production.
- Collaborate with your process equipment provider.
- Assess the risks of a potential implementation.
Just as choosing the right material-handling equipment and systems for your specific operation is key, so too is identifying a qualified solution provider with top engineering, design, and project management capabilities, and who will ultimately ensure that your company gets an implementation that will succeed.
About FKI Logistex
FKI Logistex is a leading global provider of automated material-handling solutions, supplying its customers with an integrated set of leading-edge technologies in high-speed sortation, conveyor systems, palletizing, paperless pick products, AS/RS, controls, order fulfillment systems, RFID implementation, EDS integration, baggage-handling systems, warehouse-control systems and total material handling automation.FKI Logistex provides material-handling solutions for airports, postal facilities, parcel distribution, manufacturing operations, library automation, and for warehouse and distribution facilities. With projects that include many of the world's largest and most advanced material-handling operations, the company has manufacturing, engineering, and support facilities around the world.
For more information on FKI Logistex, phone (877) 935-4564, +44 (0) 8706 060120 in Europe, or +86 21 52372255 in Asia; e-mail info@fkilogistex.com; or visit www.fkilogistex.com.
All photographs courtesy of FKI Logistex®. © 2006 FKI Logistex. All rights reserved.