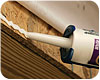
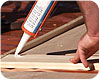
Over the last decade, however, phthalates have come under increased scrutiny for their potentially adverse health effects. Early tests linked high doses of phthalate exposure to cancer and infertility. More recently, low levels of phthalates have been associated with fetal development problems - specifically in male reproduction. In fact, some scientists claim phthalates have an anti-androgenic effect. This low-level risk, combined with the pervasiveness of phthalates in our environment, has caused regulating agencies worldwide to seriously examine the continued use of phthalates.
The Registration, Evaluation and Authorization of Chemicals (REACH) initiative is a recent regulatory effort to propose restrictions on phthalate use. Though it originated in Europe, the effects of REACH are being felt around the globe. In addition, other organizations and legislative bodies, including many in the U.S., continue to question the potential risk and liability of phthalates.
Investigations into the safety of certain phthalates date back to long before REACH was conceived. One of the most commonly used plasticizers in many consumer products, including toys, is di-2-ethylhexyl phthalate, or DEHP. Toys containing DEHP were voluntarily recalled by many toy manufacturers selling them in the U.S. because the International Agency for Research on Cancer declared DEHP a probable human carcinogen in 1982.
The Center for the Evaluation of Risks to Human Reproduction (CERHR) convened a panel to review any potential health risks to human reproduction caused by phthalates in 1999. The CERHR issued a draft report in 2000 that discussed findings of low to negligible concern on most of the phthalates reviewed. However, the panel expressed varying levels of concern for infants, children and pregnant women exposed to DEHP. The phthalate has since been linked to problems with sperm formation, low sperm counts and male genitalia deformities in trials with rodents. The term “phthalate syndrome” was coined in 2005 for use in the medical community to describe documented changes in the male reproductive system.
In response to consumer concerns, the Consumer Products Safety Commission called for a voluntary phaseout of DEHP in toys and medical devices. California issued a state ban on all children’s toys containing phthalates in April 2008. House Bill 5601 banned children’s products containing lead, phthalates or bisphenol-A. Shortly thereafter, the U.S. Congress passed the Consumer Product Safety Improvement Act (CPSIA), which placed tight restrictions on allowable lead and phthalate levels in children’s toys and childcare articles.
The future for phthalates continues to be questioned as more studies are published correlating phthalates with negative effects on human health and the environment. As a class, phthalates have often been described as moderately persistent with the potential to bioaccumulate in fat tissue. Some may be broken down in the body, although degradation and excretion rates differ between adults and children. In addition, phthalates have been shown to strongly absorb into the soil and biodegrade slowly.
Along with stricter regulations resulting from REACH, manufacturers are required to place EU warning labels to warn of reproductive hazards and potential toxicity to humans and the environment. This will only serve to increase consumers’ health concerns and focus more attention on the environmental impact of phthalates.
The REACH initiative requires potentially harmful chemicals to be classified by their degree of perceived risk. Based on the studies and negative publicity, many phthalates - including DEHP and butyl benzyl phthalate (BBP) - have been prioritized as substances of very high concern (SVHC). This means that manufacturers that previously relied on phthalates must decide whether to accept the added liability and limitations of using an additive that has already been classified as potentially dangerous or identify a viable, safer alternative.
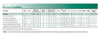
Table 1. Plasticizer Compatibility
Dibenzoate Plasticizers Provide an Alternative to Phthalates
Although phthalates offer many benefits in the manufacturing process, a number of alternatives offer equal performance, as well as substantial safety, legislative and environmental advantages. Dibenzoate plasticizers are an attractive option. Unlike some newer alternatives, such as diisononyl cyclohexane-1,2-dicarboxylate (DINCH), dibenzoate plasticizers have a proven track record of performing safely and reliably. They have been in use for a variety of applications worldwide for more than 40 years. Dibenzoate plasticizers are highly solvating monomeric plasticizers that decrease processing times and lower processing temperatures. In addition, they offer superior resistance to extraction by solvents such as kerosene, cotton seed oil and soapy water. From a health and environmental perspective, the European Chemical Agency (ECHA) listed dibenzoate plasticizers as a preferred alternative to phthalates in May 2009.Certain grades of dibenzoate plasticizers are more environmentally friendly than others. Many require no warning labels and are even approved by the FDA for use in food packaging.
Other benefits include the following.
Compatibility with a variety of polymers and applications.Dibenzoate plasticizers are compatible with many polymeric materials, including ethylene vinyl acetate (EVA), polyvinyl chloride (PVC), styrene-butadiene rubber (SBR), ethyl cellulose (EC), nitro cellulose (CN), cellulose acetate butyrate (CAB), polyurethane (PU) and acrylics (PMMA). Although no one material is universally solvent or compatible in every resin type, dibenzoates offer a good balance of compatibility, as shown in Table 1.
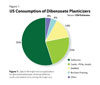
Figure 1. U.S. Consumption of Dibenzoate Plasticizers
Low in toxicity, non-mutagenic and non-carcinogenic.The U.S. EPA High Production Volume Information System (HPVIS 2009) lists both diethylene glycol dibenzoate (DEGDB) and dipropylene glycol dibenzoate (DPGDB) as non-mutanogenic and non-carcinogenic. Furthermore, the ECHA 2009 assessment lists DPGDB as not persistent, not bioaccumulative and not toxic, making it a “non-PBT” material.
Biodegradability.While many materials are not readily biodegradable, dibenzoate esters will hydrolyze in water and biodegrade under certain conditions. The US HPVIS 2009 indicates DPGDB is ultimately biodegradable under anaerobic conditions when tested in accordance to USEPA Method 796.3140. DPGDB is also readily biodegradable under the aerobic conditions of the OECD guideline method 301B. The Danish QSAR calculated the half-life of DPGDB to be 78 days.
21CFR food-contact approval.Many materials are not cleared by the U.S. Food and Drug Administration (FDA) for food contact applications; however, dibenzoates have clearance for certain applications, subject to restrictions. In fact, the choices of plasticizers become increasingly narrow, particularly as the anticipated food contact or potential for extraction increases. Very few plasticizers are approved for direct contact applications. Both DEGDB (CAS 120-55-8) and DPGDB (CAS 27138-31-4), and mixtures thereof, are among the chemicals the FDA allows to be used in the following specific applications:
- 21CFR § 175.105(c)
- 21 CFR § 176.170
- 21 CFR §176.180
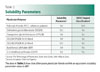
Table 2. Solubility Parameters
Lower production costs based on ability to operate lines at lower temperatures.The energy required to perform heat seal and drying operations of packaging and other coated materials is directly related to the Tgand MFFT. Lower energy consumption can lead to cost savings and reduced greenhouse gas emissions. Effective plasticization, which can be achieved with dibenzoate plasticizers, will lower the MFFT, Tgand energy consumption, as well as deliver the desired physical properties.
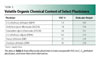
Table 3. Volatile Organic Chemical Content of Select Plasticizers
As a result of these benefits, adhesives plasticized with dibenzoate esters are ideal for the following applications: carton sealing/forming in the packaging industry; book binding and labeling; fibers and non-woven fabrics in textiles; and forming decorative wall panels, window frames, mastics and caulking compounds in construction. To a lesser degree, these high-performance plasticizers are also used to produce furniture, luggage, shoes and flooring.
End users who have traditionally relied heavily upon phthalates have looked carefully at alternatives in recent years. The flooring industry is one such example. The Toxic Use Reduction Institute at the University of Massachusetts-Lowell (TURI) indicated that DPGBD was an effective substitute for DEHP in resilient flooring. This conclusion was made after consideration of the performance and function needs of the manufacturer and customer, as well as the health, safety, environmental, and financial assessment of alternative plasticizers and functional replacements. Similar testing conducted in Europe to evaluate alternatives to the BBP plasticizer primarily used in flooring applications also concluded that DPGDB provides a good technical replacement.
Evaluations have also been conducted in other applications, such as medical devices, neonatal care products, toys and wall covering. In each case, careful consideration was given to the end performance needs of the final article, the other components used in the product, processing and end-use conditions, regulatory requirements, and cost considerations. While no single product meets every need, the final selection is based upon achieving the optimal balance in each case.
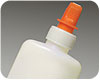
The Future of Manufacturing and Regulations
Regulations are expected to increase worldwide. REACH has set a precedent in Europe, but given the global nature of our economy, nearly all manufacturers are affected. Other countries and governing agencies are already generating similar initiatives. Whether future studies confirm or negate current theories regarding the adverse health and environmental impact of phthalates, in our precautionary culture the questions that have been raised to date will likely be sufficient to cause additional legislative restriction and avoidance by “informed” consumers. Today, largely as a result of instant access to online reports, press articles and community blogs, consumers are better educated and more active in demanding “safer” ingredients.Manufacturers need to be prepared to respond with responsible chemical selections. In the phthalate replacement arena, dibenzoate plasticizers offer a safe, reliable, cost-effective alternative.
For more information, contact the authors by e-mail at Shamsi.Gravel@emeraldmaterials.com or Emily.Mcbride@emeraldmaterials.com.