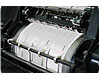
MACtac's InFusion product features hot-melt adhesive technology.
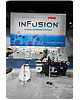
Hot-melt adhesive technology is quickly becoming a popular alternative to acrylic acid. MACtac's InFusion™ hybrid adhesive system uses this technology in the labels and labeling industry.
Despite the anticipated-and in some cases realized-improvement in the global economy, many acrylic acid suppliers are not in a position to return capacity that was rationalized in recent years due to the economic downturn. Unplanned outages throughout 2010, including facility fires, labor issues, and maintenance concerns, led to a shortage of acrylic acid monomers and, in turn, adhesive polymers.
Further straining this already limited capacity is growth among other huge consumers of acrylic acid, such as diaper, paint and clear sheet manufacturers. These applications are often more strategic to acrylic acid suppliers, offering growth and higher profit margins than those associated with adhesive applications. The end result is limited raw material availability and rising raw material costs for adhesive manufacturers.
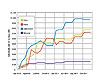
Figure 1. Recent Inflation Rates for PSA Raw Materials.
Addressing the Shortage as an Industry
For those adhesive manufacturers serving the labels and labeling industry, this limited availability and fluctuation in cost affects the production of labels, stamps, and other applications requiring these adhesives. As much as manufacturers work to offset and absorb costs when possible, industry-wide price increases or surcharges continue to be issued, and research and development efforts formerly dedicated to acrylic adhesive development may be minimized.However, aside from internal process improvements and supply chain diligence, some adhesive manufacturers have taken an entirely different approach to helping customers counter these increasing costs by recommending product solutions that feature an alternative to acrylic-based adhesive technology.
Enter Hot-Melt Adhesive Technology
Hot-melt adhesives are typically a mixture of a polymer (thermoplastic rubber), tackifying resins and a hydrocarbon diluent (wax or oil plasticizer), which is heated until flowable. The hot-melt adhesive is then coated on a web and cooled before being wound into a roll.Hot-melt adhesives typically exhibit high tack and peel, forming a strong bond quickly during the cooling process, and excellent adhesion to a variety of substrates and facestocks, including non-polar, low-energy surfaces such as polyethylene and polypropylene, making them suitable for packaging and labeling applications or product assembly. They demonstrate very good coatability and are lower in cost than most solvent-based adhesives, including acrylics. The most advanced formats, known as 100%-solids (no water or solvent), set quickly and are heat resistant once cured.
Drawbacks of hot-melt adhesives generally include processing challenges, as well as limitations performing at high temperatures (more than 150°F/66°C). They sometimes exhibit limited effectiveness when exposed to certain chemicals and ultraviolet (UV) rays. They are also more susceptible to oxidation and may darken, lose their tack and become brittle if overexposed.
Acrylics provide excellent temperature, UV and oxidation resistance, and thus are often the preferred choice for outdoor applications. They hold up well to chemical exposure, are very durable, have clarity and color stability, and bond well to polar surfaces like metal, glass, polyesters, and polycarbonates. Some disadvantages of acrylics include poor adhesion to low-energy surfaces and lower overall adhesion compared to hot melts, unless the adhesive is highly engineered.
Given these characteristics of hot melts and acrylic adhesives, hot-melt adhesives do serve as a viable-and, in some instances, superior-alternative to acrylic adhesives when used in the appropriate applications.
Sustaining a Solution
For the short- to medium-term, adhesive costs will continue to rise based on availability. Added acrylic feedstock capacity is not anticipated to come on stream, and unplanned upsets in the supply chain could have major repercussions for adhesive manufacturers that have not performed due diligence by integrating operational, sourcing and formulation innovation buffers. In addition, new, higher growth/higher margin applications, such as super-absorbent polymers for diapers, will continue to assume a larger share of the existing limited acrylic acid supply.But breakthroughs in adhesive development, such as the introduction of hybrid adhesives, which maximize adhesive performance while improving conversion and processing efficiency, have led to adhesive manufacturers transitioning customers, where applicable, from an acrylic adhesive to a customized hot-melt or hybrid adhesive. These transitions are often a sustained solution when the recommended adhesive alternative offers proven performance enhancement, cost efficiencies and supply stability.
By focusing research and development efforts on advancing hot-melt and new, hybrid adhesive technologies, and formulating these adhesives in-house, adhesive manufacturers may recognize certain competitive advantages such as a good cost position and the ability to more effectively customize adhesive performance to specific customer and application needs, enabling them to mitigate the effects of the shortage on themselves, customers and end users.
For more information, visit www.mactac.com.