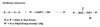
Figure 1. Urethane Structure
Keep in mind that adhesion is not a property of a material; it depends on many factors, including substrates (mainly the surface, not bulk), surface preparation, adhesive type (chemistry), specimen geometry (joint design), test method and environment. In the case of bonding zinc-coated steel with aluminum, for example, it is the aluminum and zinc surfaces that have to bond, not the steel.
Due to the growing concern over the toxicity of organo-mercury compounds in the environment, there is a universal effort to replace mercury-containing polyurethane (PU) adhesives. Organo-mercury compounds are used as catalysts in PU adhesives. The PU adhesives described in this paper represent 100% solid, two-component (2K) systems.

Figure 2. Polyurethane Structure
Polyurethane Systems
In general, a urethane bond is formed when a hydroxyl group reacts with an isocyanate group (see Figure 1). Similarly, a reaction of a diol with a diisocyanate gives rise to a polyurethane structure, as shown in Figure 2. The reactions of diisocyanates are usually more complicated than those of monoisocyanates. The initial reactivity of a diisocyanate is similar to that of a monoisocyanate substituted by an activating group (in this case, another NCO group). In the case of aliphatic diisocyanates (isophorone diisocyanate, IPDI) or aromatic diisocyanates (toluene diisocyanate, TDI; or methylene diphenyl diisocyanate, MDI), where the phenyl rings are separated by one or more CH2 groups, one NCO group has a lesser effect on the other. Nevertheless, the minor reactivity difference still exists.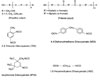
Figure 3. Structures of Various Polyols (Diols) and Diisocyanates
In adhesives, oligomeric (mol. wt. 300-4000) polyols are generally used. These polyols are based on either glycols (polyether polyols) or the ester condensation product of a diol and a diacid with OH end groups. The ester-type polyols are called polyester polyols. The reactivity of the OH group influences the kinetics of the PU reaction; for example, the primary OH group reacts three times faster than the secondary OH group and eight times faster than water. The general chemical structure of various polyols and diisocyanates is shown in Figure 3.

Figure 4. Density Data of PU Adhesive Hardeners
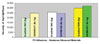
Figure 5. Viscosity Data of PU Adhesive Hardeners

New PU Adhesives
Huntsman Advanced Materials has developed three new PU hardeners that are free of mercury catalysts. (RD2008-017 is a replacement for the commercial Araldite® 2041 hardener, RD2008-050 is a replacement for Araldite® 2042, and RD2008-053 replaces Araldite® 8685.) All three hardeners are formulated compositions. The mix ratio of these adhesives, by weight and by volume, is shown in Table 1.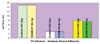
Figure 6. Gel Time Data of PU Adhesives
As is evident from the data, the properties of non-mercury adhesives are similar to the previous mercury-containing adhesives. It is clear that, barring slight variations, gel time, viscosity and density of mercury-free PU adhesives match that of the mercury-containing versions, which suggests that the bulk properties remain similar. One of the challenges in this PU hardener development was to match the gel time of the mercury and non-mercury versions. As shown in Figure 6, both versions show similar cure behavior, though mercury-bearing PU hardeners exhibit a unique cure profile that will be discussed later. It is interesting to note that, although the bulk properties seem to be unaffected by the change in the catalyst, some changes occur in the early part of the curing process, as seen in Figures 7 and 8.
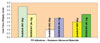
Figure 7. Cure Time to Reach LSS of 145 psi
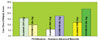
Figure 8. Cure Time to Reach LSS of 1160 psi
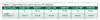
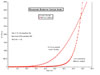
Figure 9. Cure Profile of Mercury and Non-Mercury Catalyst in PU Systems
As can be seen from the data, a subtle difference exists in the initial stages of the cure (i.e., reaching the green strength of LSS > 145 psi or LSS > 1160 psi). However, no significant difference is seen in the ultimate LSS of these adhesives, with or without mercury-containing catalysts. Though green strength values do not indicate the ultimate strength of the adhesive, these values nevertheless allow the user to set the bonding part for the next stage of production.
Safer Alternatives
Three new mercury-free adhesives have been developed to replace previously mercury-containing versions. The bulk properties and the ultimate performance of mercury and non-mercury versions are similar. The new safer alternatives enable users to easily switch from the mercury version to the non-mercury version without worrying about a loss of performance in the final bonding.For additional information, contact the Huntsman Advanced Technology Center, 8600 Gosling Road, The Woodlands, Texas 77381; phone (281) 719-7913; fax (281) 719-7500; e-mail hans_kaul@huntsman.com; or visit www.huntsman.com.
For Further Reading
1. Irving, Skiest, Ed.,Handbook of Adhesives, Third Edition, Van Nostrand Rheinhold, 1990.2. Hartshorn, S. R., Ed.,Structural Adhesives, Chemistry and Technology, Plenum Press, New York, 1986.
3. The Adhesive and Sealant Council, Inc.,2005-2007 North American Market Study for Adhesives and Sealants, 2006.
4. Saunders, J. H., Frisch, K. C.,Polyurethanes: Chemistry and Technology, Interscience Publishers, New York, 1962.
5. Wiltjam Abbate, F., Ulrich, Henri, “Urethanes. I. Organometallic Catalysis of the Reaction of Alcohols with Isocyanates,”Journal of Applied Polymer Science, Vol. 13, pp. 1929-1936.