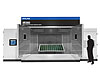
Adhesives and sealants are used by the solar energy industry in applications such as bonding photovoltaic solar panels, preventing moisture ingress into modules or electrical junction boxes, and adhering mirrors to tracking mounts in concentrating solar power applications. The building and construction industry also uses adhesives and sealants for attaching and waterproofing curtain-wall systems and fenestration.
These diverse applications share two key commonalities: the expectation of a long life performance (e.g., 20 years or more), and direct exposure to a variety of harsh environmental and end-use stresses.
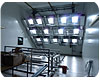
The need and willingness is increasing to test larger or full-scale products or mock-ups to better reproduce real-world conditions in accelerated testing.
Predictive Testing
To understand (and hopefully predict) the long-term weather durability of certain materials, a number of small-scale, materials-level accelerated stress tests have been devised, including UV and moisture condensation, water immersion, and thermal cycling and laboratory-accelerated (xenon arc) weathering, among others. These tests are in addition to the requisite real-time-testing (RTT) that helps to validate the accelerated tests.Available time, money and resources comprise the necessary tradeoffs in any test. Designing appropriate tests typically requires detailed knowledge about specific failure modes and causes, as well as RTT data for validation of the accelerated tests (both of which are often missing or incomplete). Tests that involve the use of known factors apply stresses that are as similar to the real-world environment as possible.
Cured-in-place waterproofing sealants for curtain-wall cladding are exposed to frequent cyclic movements during their cure, which can result in permanent and detrimental changes in sealant bead geometry and performance characteristics. During their service life, these sealants are exposed to environmental degradation stresses and cyclic joint movement, which can lead to sealed joint failure.
RILEM has developed a durability test method1that alternates between laboratory-accelerated weathering, thermo-mechanical cycling and optional fatigue cycling. According to theHandbook of Sealant Technology, “Durability studies of construction sealants specified for outdoor applications should be based on 5,000 to 20,000 hours of artificial weathering and ideally include joint movement during cure as well as during the artificial weathering of the specimen.”2
A Matter of Size
Another key aspect of testing is sampling. It is important to know whether a small test sample of a material or product truly represents that product in use and whether the stresses it will encounter are accurately represented in the test. Sealants typically need to be tested under tensile, compressive or shear stress for the results to be valid. But do small test jigs adequately represent the mechanical load of a large curtain-wall panel or the edge seal of a solar panel subjected to solar and ambient thermal cycling, wind load, and other stresses? The need and willingness is increasing to test larger or full-scale products or mock-ups to better reproduce real-world conditions in accelerated testing.Solar panels in use experience temperature changes from ambient conditions as well as unidirectional solar load (as do building panels). These temperature changes can produce mechanical stresses very different from either steady-state conditions or climate chamber tests without solar load. Moisture stress (as relative humidity) changes daily with ambient and product temperature, and condensation, saltwater, wind-blown rain sprays, or even acid rain may be present and can affect a full-size product differently than a small test sample.
Other industries, such as the automotive industry, have learned these lessons from experience. Today, the suitability of an item such as basecoat-clearcoat car paint or the skin of an instrument panel is first validated by small-scale accelerated tests and RTT weather-durability tests. Next, mid-level testing of intermediate assemblies is often performed. This step adds processing and manufacturing stresses to the mix, as well as different materials in combination or proximity, such as everything that goes into an auto’s instrument panel. Then intermediate-scale tests (e.g., DIN 75-2203) are conducted at elevated temperatures and full-scale solar simulation or in special solar tracking test boxes under natural sunlight in the Arizona desert.
Unfortunately, these trials do not eliminate the need for larger or full-scale product testing, as a complete product may behave differently in the field or a laboratory test than a smaller specimen. The automotive industry routinely exposes cars outdoors in known harsh climates such as Arizona, the Kalahari, and subtropical south Florida. In addition, some manufacturers perform larger scale weathering chamber tests in drive-in solar/climate chambers or solar/wind tunnels.
Until recently, adhesives and sealants manufacturers or users had few options for accelerated weather durability testing on 3-D or full-size products or test fixtures. However, advances in large-scale full-spectrum solar simulation (in combination with climatic tests) are now available as commercial testing services or equipment. For example, several large solar simulation climate chambers can be used for accelerated weather testing of photovoltaic solar panels. The chambers permit rapid cycling of full-spectrum solar load, temperature, and humidity in both daily and seasonal (including freeze/thaw) cycles according to a number of benchmark climates, or a hypothetical worst-case global ”composite” climate, to better understand product durability issues.
Testing Realities
In testing, only two opportunities really exist for acceleration. The first isoverstress acceleration, whereby stress levels greater than those that will be encountered in service are used. However, this practice may result in failures that would not naturally occur, and, in some instances, the overstress (such as low-wavelength UV) has skewed the degradation mechanisms and did not produce the failures seen in the field.The other acceleration opportunity istime compression, which may involve a more rapid thermal cycling than is normally seen in a 24-hour period. This approach is best used for single-stress cause-and-effect failure modes that are primarily physical in nature, since chemical degradation mechanisms may not be as easily accelerated.
An additional caveat to accelerated testing is that failure mechanisms that result from simultaneous or time-dependent sequential degradation processes may not be uncovered in tests that use only a limited number of the stresses that the product will encounter. In solar panels, for example, a “hot spot” can develop in one of the cells, and this can lead to electrical arcing and even a fire. A hot spot may result from the corrosion of the transparent conducting oxide (TCO) electrode layer, which causes high electrical series resistance. In turn, the corrosion may be the result of sodium-ion electrochemical migration out of the cover glass under conditions of current flow in the presence of moisture in the panel. Moisture ingress may be the result of UV degradation of the polymeric edge seal in the module; hence, that would be the root cause. Tests that do not combine solar radiation (for the UV degradation and electrical current production), moisture (for the ingress) and thermal cycling (for the moisture pumping action) would most likely not be able to reproduce this sequential failure mechanism.
Dual Nature of BIPV
A marriage of solar products and building materials in building integrated photovolatics (BIPV) presents new challenges for testing adhesives and sealants when solar panels are incorporated into building products (such as curtain-wall louvers and canopies or solar windows). The large size and integrated functionality of these products demands large-scale testing, including laboratory-accelerated weather testing, to accurately determine long-term durability and performance.These issues are beginning to be addressed now that large-scale, laboratory-accelerated weathering chambers, once the exclusive domain of the automotive industry, are becoming more common in the solar energy industry. In addition, commercial testing laboratories and building product manufacturers are also showing more interest in large-scale testing.
Conclusion
While traditional small-scale materials-level accelerated tests have been convenient, they do not subject adhesives and sealants to either the simultaneous and cyclic stresses of the service environment or the in-use stresses of large complex products such as solar modules or building façade panels. However, as these products become more common and the expectations for long-term durability are increased, more comprehensive and realistic testing needs to be performed.For more information, contact Atlas Material Testing Technology LLC at 4114 N. Ravenswood Ave., Chicago, IL 60613; phone (773) 327-4520; fax (773) 327-5787; e-mail info@atlas-mts.com; or visit www.atlas-mts.com.
References
1. RILEM TC 139-DBS, “Durability Test Method-Determination of changes in adhesion, cohesion and appearance of elastic weatherproofing sealants for high movement façade joints after exposure to artificial weathering,”www.rilem.net.2. Wolf, Andreas T.,Handbook of Sealant Technology, Chapter 13: Construction Sealants, CRC Press, 2009.
3. DIN 75 220, Aging automobile components in solar simulations units.