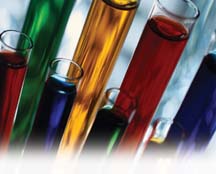
When it comes to obtaining the desired performance properties of adhesive and sealant formulations, purchasing, modifying or adjusting process equipment is not always economically feasible. This is especially true when you consider the large and ever-growing variety of raw materials available. Therefore, it becomes imperative to properly select the most appropriate raw material to fit the current processing capabilities. This article will discuss how the proper selection of additives - particularly fillers, rheological control agents and reinforcing agents - can lead to their optimum dispersibility, enhanced performance, and formulation cost reductions in such processes.
Additives are generally used as a primary contribution to the existence of the end product, or they act as auxiliary or secondary functions. The range of additive substances used in the adhesives and sealants industry includes plasticizers, thickeners, fillers, curatives and emulsifiers. To optimize their influence in the formulation, additives must be homogeneously mixed or dispersed throughout the system. For powdered additives often used in large loading levels (such as calcium carbonate, silica, talc and mica), optimum dispersibility is even more important because of inherent particle agglomeration during the manufacturing process. To deal with these issues in light and heavy body formulations, e.g., low to high viscosity systems, these materials require medium- to high-shear energy dispersion equipment. The proper choice of equipment is dependent on the unfilled formulation viscosity and the required shear needed to achieve optimum homogeneity of the additive(s) in enabling its maximum effectiveness.


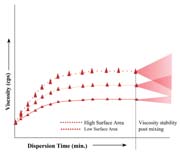
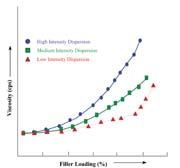
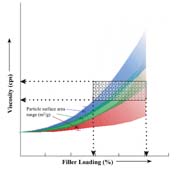
This article is based on a paper presented at the Spring 2004 Adhesive and Sealant Council Conference in Cleveland.
For more information, contact Material Apps LLC, 408 Shipwrighter Way, PO Box 1571, Lansdale, PA 19446; phone (215) 855-5902; fax (215) 855-5946; or visit http://www.materialapps.com .