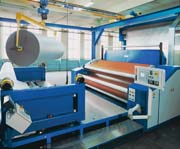
For its high-end automotive customers, the challenge for K&L is to apply high-quality laminations to ensure optimal, long-term bonding of diverse materials contained in a variety of interior components, including door paneling, head liners, side panels and seat heaters. The thermal bonding capability of hot-melt adhesives is applied to meet the special requirements of K&L's automotive interior applications.
Because automotive interiors require large amounts of adhesive, the hot melt is applied by way of a powder scattering process on any of four laminating units. These include one unit with a coating width of 180 cm and two units with a coating width of 2 meters and a maximum capacity of approximately 26 Mio.m2 (at a speed of 50 m/min - always practical for high strength textiles). A fourth unit has a 3-meter working width and operates as fast as 50 meters per minute. The company also uses an extruder unit for direct melt-on of granulates and application in bonding seams.
In choosing hot-melt adhesives for its automotive applications, K&L requires a product that will scatter well in powder form and grain sizes that best suit its laminating machines. As a result, K&L primarily uses VESTAMELT® hot-melt adhesives from Degussa's High Performance Polymers Business Unit, Marl, Germany.
VESTAMELT adhesives are copolyamides based on the essential monomer laurolactam (PA12). Predominantly used for high-performance bonding in the textile industry, the adhesives are particularly suited to the high-temperature requirements of automotive interior applications. Relevant performance features include the following.
- Excellent adhesion properties with a range of interior materials that may need to be bonded, including nylon, soft PVC, leather and chrome.
- Thermal resistance as high as 110°C. Depending on the required resistance to heat, several grades of the adhesive with different melt viscosities can be applied to bond head liners, door paneling and seating upholstery, and for fastening seat heaters.
- Strong thermal stability over the lifetime of a car.
The hot-melt adhesives are non-toxic and, unlike other reactive systems, have absolutely no harmful effect on skin, which is especially beneficial for car seat applications.
Choice of Grades
Because each interior product is an application in itself, K&L is able to capitalize on the different melting points and viscosity levels available with various grades of adhesive. In addition, laminations with VESTAMELT are separable due to the thermoplastic nature of the polymer PA12 - an advantage for the automotive industry, which requires that laminations have recycling properties.Another criterion K&L examines in its consideration of hot-melt adhesives is fogging behavior - the tendency of a plastic material to volatilize the aforementioned variety of materials used in auto interiors. Fogging behavior of VESTAMELT adhesives has been demonstrated to be very good, particularly at high temperatures, which minimizes the chances of interior materials getting brittle or hardening and resulting in material fatigue and premature aging.
Strong Technical Support
K&L has been applying hot-melt adhesives for nearly a decade. However, automotive interiors are constantly being redesigned to keep up with changing styles or consumer preferences, thus making the choice of an effective adhesive a never-ending challenge. For this reason, it is imperative to work with a hot-melt adhesive supplier that can provide not only good products but also the strong technical support essential to help address the special requirements each new application brings. Degussa's High Performance Polymers Business Unit's technical expertise is based on the special knowledge gained from manufacturing its own material.Each new bonding application entails a lengthy development phase, during which technical personnel from K&L and Degussa examine the specific materials to be glued together. A catalog of requirements is then compiled, and a VESTAMELT grade chosen for initial trials. Fortunately, these trials need not be run on K&L lines, but instead at Degussa's Technical Center in Marl. There, coatings can be made using typical application methods (e.g., paste dot, powder dot, double dot, meltprint, scattering-line), after which bonding strength is tested, the necessary coating weight is qualified and optimal processing parameters are defined.
Once the optimum grade is determined, K&L may call on Degussa to modify the hot-melt adhesive powders with special additives should running conditions need to be improved. In this way, the respective technical strengths and expertise of both companies are used to optimal advantage.
For more information on Kaschier und Laminier GmbH, e-mail or visit http://www.kaschier.de. For more information on VESTAMELT hot-melt adhesives, e-mail info@vertamelt.de or visit http://www.vestamelt.com.