When choosing a pressure-sensitive adhesive (PSA) tape for your application, it’s critical to understand the materials you want to bond together and the application operating environment. The level of adhesion, bond strength, and durability will vary depending on the combination of substrates and the type of PSA tape you choose. Here are five important questions to ask before you make a selection.
1. How rough is the surface texture?
The adhesive tape you choose depends on the roughness of the surface. Smoother surfaces can be easily bonded with a thinner adhesive, but rougher, irregular surfaces can require a thicker adhesive that has a better flow. Firm adhesives or very thin adhesives may not wet into the surface of a material, failing to form a secure bond if one or more of the substrates has a rough or uneven surface. Instead, such surfaces require PSA tapes with a thicker layer of soft, viscoelastic adhesives that flow into the smallest valleys of a surface. The flow of the adhesive, given ample dwell time, is enough to securely form a bond between two rough surfaces.
Choosing the right thickness and flow of your adhesive is a matter of starting with a few good candidates and testing them out on the surfaces being bonded to see which tape provides the optimal bond.
2. What is the contour of the surface?
The contour of the surface directly impacts the type of tape that will be most effective. Similar to surface texture, it decides the thickness and firmness of the tape that should be used. Running pressure-sensitive adhesive tape along a flat surface differs greatly from running it along a contoured surface. The greater the curve, the more flexible the tape will need to be in order to correctly bond to the surface. Depending on the rigidity of the secondary surface, the tape thickness becomes an important consideration as well. If the tape is too thin or firm, it can cause internal stress on the tape and/or minimize surface contact (resulting in tearing) and flagging (lifting at the edges). A thicker, more flexible tape with a softer adhesive allows for maximum surface contact and bond strength.
3. What is the surface energy of the substrate?
A substrate’s surface energy is a relative measurement of the excess energy on the surface of a material, and its importance in the bonding process cannot be understated. The surface energy of a particular material mainly affects the wetting of the adhesive on PSA tape. This phenomenon is how quickly and how much the adhesive spreads out on the bonding surface, affecting the strength of the attraction. The higher the surface energy the greater the attraction, which in turn causes more wet out, meaning the surface is easy to adhere to. Conversely, the lower the surface energy, the lower the attraction and the less the PSA wets out the substrate.
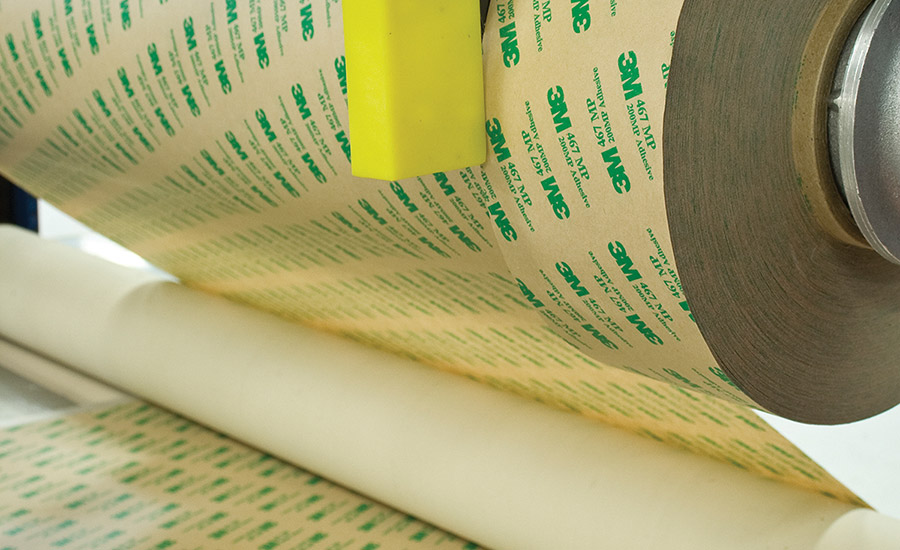
High-surface-energy materials that have an excellent adhesive wet-out include:
- Aluminum
- Copper
- Stainless Steel
- Tin
- Glass
- Porcelain
Medium-surface-energy materials, including a range of plastics and paints, typically demonstrate very good adhesive wet-out, such as the following:
- PVC
- Acrylic
- Nylon
- Polyester
- Polyurethane or epoxy paints
- Kapton (polyimide film)
- Phenolic
- ABS
Low-surface-energy materials are harder to adhere to because the attraction is not as strong. Low-surface-energy materials with poor adhesive wet-out include:
- Polystyrene
- Polyvinyl acetate
- Acetyl
- EVA
- Powder paints
- Polyethylene
- Polypropylene
- UHMW
- Tedlar (PVF)
- Teflon
The material surface energy will dictate what PSA will provide an adequate bond to your substrates.
4. Is there surface contamination?
Solid and liquid contaminants often cause a poor bond between the PSA tape and the substrate. Contaminants like grease, oil, and moisture can form a barrier between the surface and the adhesive on the tape, causing the bond to fail. Particles like dust, talc, and fibers can impact the tackiness of the PSA tape and reduce the contact surface area, which will also cause the bond to fail over time.
It is important to understand what surface contaminates may be present and to ensure that proper cleaning and priming techniques are used to ensure that a proper bond can occur. While a 50:50 mix of isopropyl alcohol and water is the most commonly suggested cleaning agent, sometimes more aggressive cleaning and surface preparation is required.
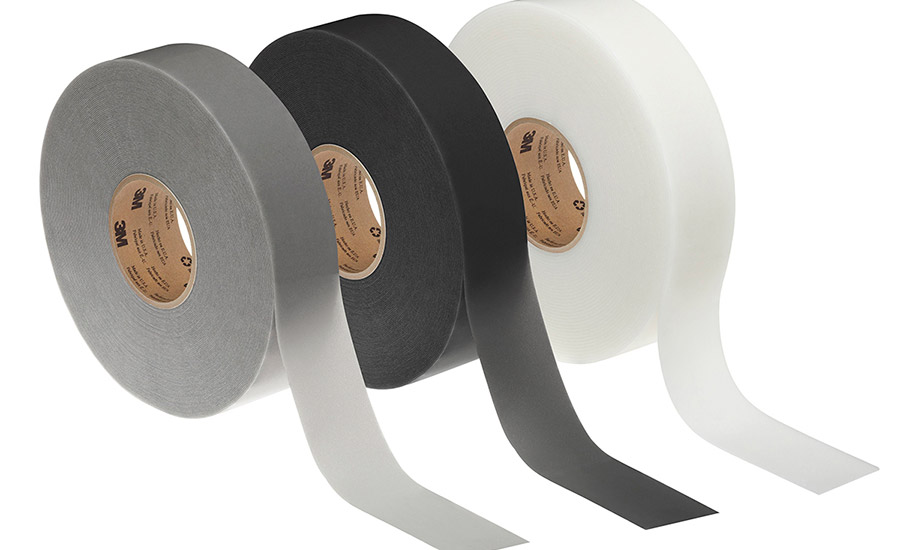
5. What is the operating environment?
The final application environment of the part is just as important as the substrates themselves. Different environmental conditions create challenges for certain adhesive tapes, often resulting in weaker bonds or even bond failure. It’s important to ask what conditions your PSA tape will be exposed to. These may include:
- Solvents and chemicals can cause adhesive tapes to swell, soften, and even dissolve. If your substrates are often exposed to chemicals, it’s best to consider acrylic adhesive tapes, which have a high cohesive strength that makes them resistant to many solvents for extended periods.
- Plasticizers can cause adhesive tapes to soften, turn stringy, or become discolored over time. Choose a tape that is resistant to plasticizer migration, which prevents the tape from softening. Acrylic adhesive tapes are better than rubber tapes in this application.
- UV light exposure causes PSA tapes to become discolored and brittle over time, and it can also cause chemical degradation and a failure of the adhesive. Different PSA tapes have different levels of UV light resistance.
- Low temperatures/cold air causes some adhesive tapes to harden and become brittle. This not only reduces the adhesive tack, it can also lessen resistance to impact shocks. Cold-temperature-performing PSA tapes are ideal for low temperatures.
- High temperatures/hot air causes adhesive softening and reduces the shear and cohesive strength of the tape. If you are bonding surfaces that are exposed to heat or high temperatures, use PSA tapes that can perform well in this environment (like silicone foam tapes).
Selecting the right PSA tape product can be a straightforward process when you understand the texture, contour, and surface energy of the substrate, as well as the environment in which it will operate.
Learn more about Engineered Materials Inc. at www.engineeredmaterialsinc.com.
Article images courtesy of Engineered Materials Inc.