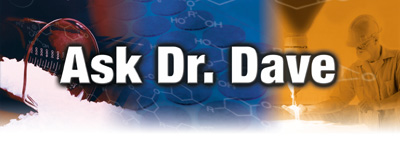
Question
We manufacture electronic water meters out of high-density polyethylene and need to fill a 1?inch-deep groove with a sealant. The meter is used outdoors, and the joint must be totally waterproof. What do you recommend?Answer
Because the meter is used outdoors it will be exposed to the extremes of weather. The sealant will need to be flexible to accommodate the expansion and contraction of the meter caused by changes in ambient temperature. A butyl sealant is an obvious candidate here. It will be quite flexible and have outstanding resistance to both liquid water and moisture vapor.Question
We make tin-plated steel cans and are urgently trying to replace lead-based solder for assembling the seams and attaching the nozzles. Silver solder is an alternative but is too expensive. Are there adhesives available that will be strong enough and able to resist the wide range of chemicals that are packaged in the cans?Answer
You must be an overseas manufacturer because lead-based solder has been phased out of U.S. and European products for several years now. Most U.S. manufacturers removed it voluntarily from food containers prior to government legislation, and I believe that it has been removed from all other types of cans. Most manufacturers have changed to welded joints, silver solder or have redesigned their cans to not require any solder.Changing to a silver-based solder (typically alloys of tin, silver and copper) is definitely a cost issue for a relatively low-value item like a can. I did in fact do work in this area several years ago and found that specially formulated epoxy adhesives and polyamide hot melts were two serious candidates to replace solders. Polyamide hot melts are quite difficult to handle, requiring application temperatures of 400 deg F and higher, but give outstanding adhesion to tin-plated steel. The epoxies proved valuable in that they were very resistant to most paint-related or automotive chemicals, with the exception of methylene chloride (which subsequently has been phased out of almost all such products).
The major stumbling block to this project proved to be devising a system that could bond the cans quickly enough to be compatible with modern high-speed manufacturing where hundreds or even thousands of cans per hour are made. For a new and small manufacturer of specialty cans who does not desire to invest large amounts of capital, adhesive bonding is definitely worth considering.
Incidentally, the major use for lead-based solder is now in the manufacture of electronic circuit boards, and there is a major push to eliminate this hazardous metal from all operations by 2004.