
Temperature Requirements
The process is best accomplished at the lowest possible temperature to avoid boiling, off-gassing, loss of solvents and possible premature curing of sensitive products. Conventional processes have employed slow, gentle batch-mixing processes for these reasons. It has not been unusual for these mixing and agitation batch processes to take many process hours - sometimes days - to bring the formulation to completion. This tried-and-true method was able to accomplish the end result with low temperatures and little evaporation or loss of solvents due to long process or batch cycle times.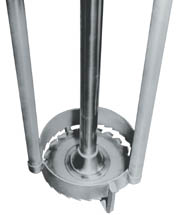
Single-Shaft Machines
For light- or medium-viscosity products, high-speed rubber cutters are typically supplied as a single-shaft machine (see Figures 1-2). Variable speed control of the mixer shaft RPM is a necessity. The use of a variable-frequency drive is preferred. The drive, whether it is a variable-frequency type or a mechanical adjustable variable speed, should have the capability to provide a maximum tip-speed of the rubber cutter blade in the range of 5,000 FPM. After particle size reduction has taken place, recirculation of the batch (contacting the particles with the solvent material) becomes the primary objective. High tip speeds are no longer needed for the batch turnover process, and it is desirable to reduce the mixer RPM to a level where maximum mixing efficiency is realized without a buildup in batch temperature.The rubber cutter blade should be equipped with sharp, saw-like teeth. In some processes, depending on the raw materials and the formulation requirements, the blade can be "open" and configured much like standard high-speed dispersers typically used in the coatings industry. Most rubber cutter arrangements include a stationary shroud around the blade, similar to a rotor stator or homogenizer-type arrangement. The shroud directs flow and funnels the circulating solids/solvent suspension back into close contact with the blade and the shroud, where further size-reduction takes place. When higher viscosities are involved or other parameters become factors, it becomes appropriate to consider a dual-shaft machine with a jacketed mixing vessel for heat-transfer needs.
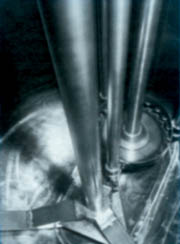
Dual-Shaft Machines
The addition of a second shaft to a single-shaft machine benefits most applications (see Figure 3).
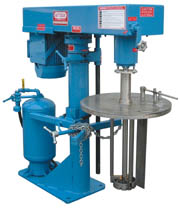
For more information on high-speed cutting and dissolving, contact Myers Engineering Inc., 8376 Salt Lake Ave., Bell, CA 90201-5816; phone 323-560-4723; or visithttp://www.myersmixer.com .
Sidebar: Advantages
The high-speed rubber cutter and dissolver process offers the following advantages over conventional methods.- Production time can be cut by 75% over conventional agitation or dispersion methods (see Figure 4)
- Reduced preparation time as chunk rubber or strips of rubber can be directly added to the batch
- The rubber additions are quickly reduced to "crumb" size by the mechanical shredding action of the high-speed cutter
- Crumb-size particles have larger total surface area per unit volume, allowing more intense solvent contacting
- The high-speed rubber cutter in a dual-shaft configuration can handle extreme swings in viscosities, from water-like in consistency to fluids of a heavy, syrupy consistency
- The process can be completed in a closed tank keeping the solvent vapors contained and out of the working environment
- Airborne vapors in the mix tank can be recycled to the liquid phase of the solvent through a cover-mounted re-flux condenser, thus recapturing valuable solvent for re-use and offering environmentally friendly benefits
- Mixing temperatures are kept under control through the use of a tank-cooling jacket, which can circulate coolant or chilled water to maintain the solvent at a manageable, non-flashing temperature
- In a single- or dual-shaft machine, the high-speed rubber cutter does the work of producing crumb-like particles and circulating the solvent-laden rubber crumb particles for further contacting and eventual dissolving into the batch. The second shaft of a dual-shaft machine is a slow-speed anchor/bow tie mechanism with vertical risers that can be equipped with scrapers that contact the tank sidewalls and bottom head. This assists in reducing material buildup, which can be detrimental to efficient heat transfer. If the rubber compound builds up on the internal tank walls, it prevents heat transfer from the jacket and permits the batch to heat up. If not controlled, with repeated cycles, the batch temperature will rise, drawing off more solvent vapors with an increase in fluid viscosity of the batch. As the batch viscosity increases, an increasing energy demand is made on the mixers and the cycle repeats itself, compounding the problem
- High-speed rubber cutters and dissolvers must be designed for the process and a specific range of batch sizes. Typical batch sizes range from 10 to 15 gal to 1,500 gal and larger (see Figure 5). The design requirements critical to the process are the batch size, type of rubber, size of rubber, solvent type, density and viscosity of the adhesive, and the process time requirements