Magnum Venus Products (MVP) is a Florida-based company that manufactures resin-based compounds such as syntactic foam core bonding putty, ceramic shield, syntactic foam core resin and DCPD/isophthalic polyester resin, among others. The company’s products are used in the marine industry and by other fiberglass product manufacturers to enhance the cosmetic appearance, rigidity, and speed of fiberglass reinforced plastic products, bond fiberglass parts, and fill strakes and tight radii.
When MVP decided to produce its resin-based line in 1998, it faced the challenge of finding an effective method of filtering the finished products from a high-viscosity mix. Since many of the company’s customers used spray guns in the application process, it was critical that the products be consistent in texture and particle size.
MVP Facility Manager Jim Kurtz solved the problem by installing a Spencer Self Cleaning CIP Filter manufactured by Spencer Machine & Tool Co., Jeffersonville, IN. Comprised of 316 stainless steel, the filter is AMSE coded and uses a wedge wire screen as a filtering element. The unit uses a number of different micron-size screens depending upon the products that are being manufactured. These screens are easily replaced and keep setup costs low.
“Since we installed the filter five years ago, we have had virtually no problems filtering our products,” Kurtz says. “Maintenance cost is at a minimum, and we have never replaced a filter screen.
“During the last five years we have purchased two additional Spencer Filters to accommodate our increased production requirements,” he says. “The Spencer Filters are fantastic. Without these filters we would not be able to maintain our high operating efficiencies.”
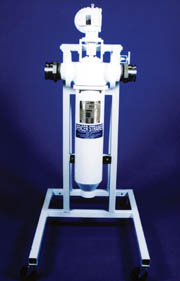
Durable Design
Spencer Filters have been implemented in a variety of industries, from paint manufacturing to orange juice and peanut butter processing. Al Hublar, national sales manager at Spencer, credits the filter’s unique design and reliability with its widespread use.“I don’t know of anybody who’s actually worn one out,” Hublar says. “Those (filters) will go forever if you maintain them.”
Process flow to the Spencer enters from the top where it is directed into the filter housing surrounding the outside diameter of the wedge wire element where the unwanted solids are deposited and the fluid passes the element and flows upward through the inside of the screen and exit port located at the top of the housing.
The wedge wire element is continuously rotated by an electric or compressed air driver. Two durable wiper blades are statically located and positioned with constant tension applied against the rotating filter element. The self-compensating blades remove unwanted solids from the screen where internal fluid flow path and turbulence directs them toward the bottom area of the filter housing.
Removed solids can be manually or automatically flushed from the housing as they accumulate in the bottom of the filter. Automatic flushing of the solids can be accomplished using a pressure-sensing device that monitors the differential pressure across the filter inlet to its outlet. Smaller batches with lower solid percentages may be manually purged.
The Spencer element can withstand differentials much higher than nearly all bag or cartridge media. And though the Spencer unit is designed to operate at low or virtually nonexistent differential pressures, accumulated solids can present a rise in pressure. To avoid “pushing” of soft, gelatinous solids through the screen openings, it is imperative that flushing be accomplished at a pressure well below those established.
About Magnum Venus Products
Magnum Venus Products maintains relationships with a network of over 200 individual service-oriented distributors throughout the world, providing equipment solutions for all operations. MVP took the first step in reducing styrene emissions in the spray-up process by introducing FloCoating technology. The company’s newly patented FIT (Fluid Impingement Technology) reduces emissions below that of the FloCoat technology, with the added benefit of waste reduction and increased transfer efficiencies.
For more information, visit http://www.magind.com, call (727) 573-2955 or e-mail info@mvgind.com.
About Spencer Machine & Tool Co.
Spencer Machine & Tool first entered the filter market when Glenn Spencer helped a toothpaste manufacturer develop a filter to replace disposable bags that were costly to maintain and held up production. Spencer’s solution was a self-cleaning filter system that could handle a high flow rate as well as viscosity while lowering the risk of exposure to hazardous materials for workers in the chemical manufacturing industry. Many food manufacturers have experimented with the Spencer Filter in the past, and have succeeded in replacing static screens that require maintenance and cause downtime in production.For more information, visit http://www.spencerstrainer.com, call (800) 801-4977 or e-mail spencer@spencerstrainer.com.