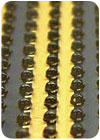
Photopolymer material chemistries were introduced in the 1960s as an alternative to solvent-based material chemistries. Their advantages were so readily apparent that they were quickly adopted for many industrial applications. Photopolymer chemistry offers an attractive replacement for solvent-based adhesives because it eliminates the volatile organic compounds (VOCs), fumes, complexity and risk associated with mixing materials to initiate hardening. The adhesives industry has pioneered many new fast-growing applications enabled by UV-curable adhesives, including dental composites, electronic "glob top" coatings, medical and optical adhesives, and DVD bonding adhesives.
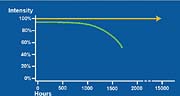
Environmental, health & safety concerns. The plasma in medium-pressure mercury lamps generates considerable heat, and the bulbs are vulnerable to breakage that can expose the environment to toxic materials. Disposal of mercury-based lamps is a significant and growing problem. Mercury lamps emit short wavelength UV, which can cause skin and eye damage if not operated properly. They also generate toxic ozone that must be exhausted.
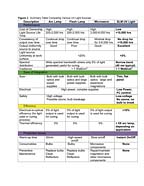
Cause process variability. Use of lamps can cause heat damage to parts, while degradation of light over life and bulb-to-bulb variability can produce inconsistent process results.
Over the years, semiconductor devices have replaced most other bulb- and tube-based technologies. For instance, vacuum tubes have long since been replaced with transistors, and LEDs are rapidly displacing light bulbs in indicators, traffic signals, and vehicle tail lamps. Semiconductor lasers have replaced arc lamp sources in many production processes, but have had little impact in industrial UV-curing applications. Recent developments with semiconductor light sources are providing a new alternative with significant advantages in operating cost, processing speed, quality of illumination, reliability, and safety, thus enabling new applications to be implemented for the first time.
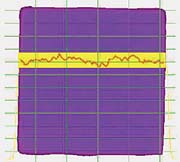
Semiconductor Light Matrix (SLM) Technology
SLM technology is implemented with an array of thousands of light-emitting semiconductors (see Figure 1) configured into a system that performs the following function:- Light is efficiently collected and directed at the target using tiny lenses.
- The heat generated by the array is managed with conductive packaging technology.
- Electronic control allows on/off, pulsing and light-intensity control, and is insensitive to failures of individual semiconductor devices.
- The uniformity, intensity and size of SLM arrays meet or exceed production requirements at acceptable cost.

Benefits of SLM UV Light Sources
There are several cost and performance benefits to using SLM light sources as opposed to other technologies (see Figure 2). These include the following.
Low Cost of Ownership and Operation
Semiconductor UV light sources use far less power (and require less cooling water) than bulb-based curing systems while providing an equivalent amount of light energy. Since there are no bulbs to burn out, the cost of consumables is less, as is the labor cost required to maintain the equipment is less.
Arc lamps have well-known failure modes and a characteristic power drop with time. Failure may result from several causes, including contamination of the quartz envelope encasing the ionized gas, and degradation of the electrodes of arc lamps. Unless the bulb breaks, the output of arc lamps will gradually decrease in radiant output, and the relative intensity of each wavelength will change during this degradation. This can effectively limit the use of arc lamps in many applications to less than 1,000 hours (see figure 2), which results in not only significant cost in replacement of bulbs, but also significant cost in lost productivity due to the time required to cool the bulbs before they can be physically removed and replaced at the end of their lifetimes. There is also a hidden design cost since engineers specify their systems with a certain amount of "padding" (i.e., they specify a bulb that is brighter than it needs to be) to ensure that the rated output of the bulb will remain above the required specification for its expected lifetime.
In contrast, SLM light sources show virtually no degradation over as long as 15,000 hours of operation (see Figure 2).
SLM light sources' ability to be turned on or off during the curing cycle saves money by reducing electrical use. This enables the use of curing "recipes" that can significantly improve curing performance including thermal load into the workpiece.
SLM sources also eliminate the need for shutters, Faraday cages, heat filters and spinning or cooling stations in the integrated solution. In most cases, the cost of ownership is 60-80% lower with SLM sources when compared to traditional light sources.
Uniform Coverage over Wide Areas
SLM light sources have an impressive range of control that makes them uniquely beneficial for UV curing applications that require uniform illumination. The output intensity can be set at any value between the minimum and maximum by simply adjusting the current that is supplied to the array. The intensity varies almost linearly from zero to maximum output with no variation in the uniformity of light distribution.
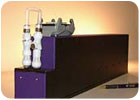
Light from a typical mercury arc lamp is distributed over the spectrum, from deep UV to the infrared (see green plot in Figure 5). Some of the long IR is due to the fact that the surface temperature of an ultraviolet lamp under normal operating conditions is 600-800°C, which means these lamps waste energy and can cause significant heating of the work piece, which may result in deterioration and damage.
By contrast, the spectral distribution from the SLM is concentrated in an intense narrow spectral range (see yellow plot in Figure 5). Since the photons generated by SLMs have a narrow spectral distribution (typically 40nm), all the light produced is useful for initiating the desired chemical reactions.
While some photopolymer systems available today use photoinitiators that are not designed for SLM light sources, it is easy to develop a new photopolymer system for such a uniform, high-intensity source. Internal studies have confirmed that there are significant advantages to increasing the intensity at the same dose for any given material, and that longer UV wavelengths allow deeper penetration and inside-out curing. There are other curing advantages when using SLM technology that go beyond the scope of this article.
UV curing is typically done in the presence of air, and oxygen inhibition has been a persistent problem.5 Several techniques are used to overcome this challenge, with pulses of high-intensity light and inert gas envelopes being two of the most common. The ability of SLMs to pulse the light source allows the user to program "recipes" that might, for example, involve a high-intensity pulse for deep cure and overcoming oxygen inhibition, followed by a less-intense, continuous dose of a lower amplitude to cure without generating heat; this is followed by a turn-off between cycles. Sensitive components like medical or optical media can be cured without significantly heating the parts above ambient temperatures (see Figure 6).
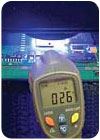
SLM systems are also significantly easier to integrate than lamp-based illumination systems because they are smaller, lighter and allow complete computer or PLC control. Additionally, the light sources are modular, so several can be grouped to match a desired curing area.
Safer and More Environmentally Friendly
Modern, high-power arc lamps typically use mercury and generate ozone and significant heat and light. Arc lamps require users to protect themselves from the toxic materials and known carcinogens, and wear safety equipment to protect from burns and eye damage.
SLMs present no inherent health risks for personnel using them, beyond the obvious and necessary requirement that proper eye protection be used to guard against their bright light. SLMs use no mercury, produce no damaging or carcinogenic wavelengths, do not produce ozone, and do not generate or contain any toxic waste products.
A Cleaner Process
The extreme temperatures on the mercury lamps quartz surface require continuous cooling. This is ordinarily accomplished by pulling or pushing air across the bulb using blowers. The cooling air is disruptive to the process environment, frequently causing contamination by stirring up airborne contaminants. SLMs require cooling at the mounting surface but not at the source's face. No air movement between the source and substrate eliminates contamination.
The lack of moving air and the low heat output of SLMs allow the source to be placed extremely close to the curing surface, if desired - an impossible arrangement with traditional lamps.
UV Curing Results on Adhesives and Coatings
SLM-based curing has been applied to over 120 different coating materials, and customers have verified that SLM sources cure better, faster, or as well as other UV light sources.Conclusion
Mercury-based arc and microwave lamps are the traditional and well-established source for UV, and will continue to be required for certain material formulations and applications. However, semiconductor light-matrix sources that match or exceed the curing performance, enable new applications, and exceed the characteristics of arc lamps in a variety of production applications are already in full production. These include electronic, optical and medical device assembly; protective coatings; and heat-sensitive applications such as optical media.For more information on curing equipment, contact Mark Owen, Phoseon Technology, 7425 NW Evergreen Parkway, Hillsboro, OR, USA 97124; phone (503) 439-6410; or e-mail mark_owen@phoseon.com.
A sample list of adhesives and coatings that have been cured with SLM arrays can be found on our website at www.adhesivesmag.com.