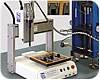
Additional questions to ask include: What type of application is this, a shot (fill) or a bead application? Will the dispense valve be mounted on a robot, gantry or pedestal-mounted so the part can be presented to the valve, or will it be manually held? What is the flow rate of the material to be dispensed? All of these questions will help you understand the material and application requirements, as well as what valve is best designed for the specific process demands.
In the process of dispensing and mixing the two components, it is critical that both components are introduced into the mixer at precisely the same time, on-ratio and at the correct flow rate. If these conditions are not met, the mixed material may not cure, leaving a “soft spot” in the encapsulant or a place where the material does not adhere. This can result in failed or scraped parts and loss of production. With today’s tight delivery schedules and thin operating budgets, no quality or production manager can afford these types of problems.<
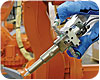
Chemistry
It is essential to know the attributes of the materials to be dispensed; much of this information can be found on the Material Safety Data Sheet (MSDS) and the Tech Data Sheet (TDS), which are supplied by the material manufacturers.Today, epoxies, silicones, urethanes, methacrylics, and other adhesive and sealants offer a wide range of physical properties. Chemistries are constantly being modified to meet a particular manufacturing process, and it is important to have a good understanding of the material you are going to dispense before selecting the dispense valve.
With so many different material chemistries available, consideration needs be given to the components of the valve that will come in contact with the material. Knowing the chemical composition of the materials that are to be dispensed allows for the correct selection of the hard and soft goods found in the dispense valves.
Some materials are corrosive or have aggressive components, while others may be abrasive and can cause premature wear if not given proper attention. Certain materials require a specific stainless steel to ensure that the curing agent is not negated and the material rendered ineffective. Other materials will cure or crystallize when exposed to ambient moisture. Proper handling of these materials is commonly understood, but it is important to remain mindful and avoid their exposure to moisture.
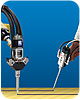
Power static-mix dispense valve mounted on 6-axis robot with manual
two-component valve dispensing adhesive beads.
Viscosity
The viscosities of the materials to be dispensed can vary widely, from thinner than water (1 cps) to as thick a heavy tar (greater than 1,000,000 cps). If you are dispensing two thin or two thick materials, the materials can often feature similar dispensing properties and affect the back-pressure and dispensing process similarly. However, if the two materials have widely different viscosities, like olive oil (84 cps) and peanut butter (250,000 cps), a new set of conditions needs to be addressed.It is critical that both materials come together in the mixer at the same time, on-ratio and at the correct flow rate, so thought needs to be given to valve selection. The lower-viscosity material will flow more readily and with less back-pressure than the thicker material. It is therefore important to design the dispense valve so the thinner material does not come out of the valve sooner than the thicker material. This condition is called “lead-lag” and can cause problems with the mixed material’s cure properties.
To resolve this difference, forethought must be given to the sizing of the valve exit ports so that the back-pressure and flow rates of the two materials allow proper flow and a uniform, homogenous mix. Finally, if the problem cannot be resolved, a dual-valve, static-mix manifold can be used. Most two-component valves are designed so the resin and catalyst are allowed to flow simultaneously when the valve opens. The dual-valve, static-mix manifold is designed so the resin and catalyst valves operate independently. With this design, the valves can be opened at separate intervals to offset the lead-lag condition.
Viscosity can also influence how the material stops flowing when the dispense valve is shut off. Ideally, the flow of the material should stop cleanly once the valve is turned off to prevent material waste and mess (such as if the mixed material strings or oozes on the outside of the parts or on the process line). Thinner materials that seek their own level need to be dispensed from a drip-less ball-and-seat-style dispense valve, which shifts the ball onto the seat to impede the flow of the material.*
Thicker materials that cause greater back-pressure in the mixing chamber and can be stringy (or otherwise difficult to cleanly shut off) require a spool-style valve.** This type of valve draws a spool back to shut off, which eliminates the pressure in the mixer that would bleed out if it was not reduced.
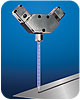
Dual-valve, static-mix manifold dispensing a wide-ratio adhesive for
metal bonding applications.
Ratio
The material’s resin/catalyst ratio can vary from 1:1 to beyond 100:1. Not all valves are designed to dispense ratios greater than 5:1, so it is important to know the volumetric ratio of the material to be dispensed and make sure the valve is capable of operating at that ratio.Wide-ratio materials can present a unique set of conditions. Not only does the dispense valve have to be designed to dispense wide ratios, but the metering equipment needs to be capable of maintaining the correct ratio at the necessary flow rate(s) to the dispense valve. Because one part of the material will flow at a higher rate than the other, the size of the orifices in the valve outlet needs to compensate for the difference in flow rate and the back-pressure.
The wide ratios can also create a problem with the proper mixing of the two materials. Some wide-ratio applications can have a low flow rate as little as a trickle and a high flow rate that is a steady stream. In this case, how and where the low-volume side is introduced into the stream of the high-volume side can have a significant impact on the mix quality of the two components; the dispense valve has to be selected with that in mind.
Flow Rates
The flow or fill rate of the process dictates the size of the dispense valve. As a result, the valve must be capable of providing the mixed material at the volume needed for the process. If the sizing on the valve is too small, the back-pressure can have an adverse affect on the metering equipment and could possibly influence the performance and ratio of the equipment. Low-, standard- and high-volume dispense valves are available to match to specific process flow rate requirements.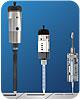
High-, medium- and small-flow rate dispense valves applying different
size bead profiles.
Static-Mixing Valves
In the past, choices were limited when dispensing a two-component adhesive or sealant. One option was to use a mix manifold block along with an inline static mixer(s) that had to be solvent-flushed or resin-purged to prevent curing. The other option was a dynamic mixer, but, like the mix manifold block, dynamic mixers had to be broken down and cleaned at the end of production. Since the introduction of static disposable mixers, the design of two- component dispense valves has evolved a great deal. Today, static disposable mixers are used in most applications and can be easily disposed of when production is finished.Static mixers are designed to work when the two materials are introduced into the mixer from the dispense valve. They are cut in half and folded as they pass over each individual mixing element so that the material is completely blended by the time it passes through the mixer. Static mixers are available with different numbers of elements in order to address the necessary degree of mixing. In addition, a variety of diameters are available that can be matched to the material being dispensed and the process parameters. Static mixers can also be adapted for Luer-Lok needles and high-pressure “stream” insets.
For processes that require additional blending, static mixers have been designed for use on power static-mix (PSM) valves. With a PSM valve, the mixing elements in a rotary static mixer are spun within the mixer tube. The mixers can be properly disposed of during production breaks, thus alleviating the need to break-down and clean the dynamic mixing valves.
PSM mixers are available with either pneumatic or servo-drive power heads. Pneumatic power heads are typically set at the preferred rotational speed necessary to achieve the desired material blend; servo-driven power heads operate at higher speeds and offer the most consistent mixing speed and material blend. To determine the proper static mixer size, tests typically have to be run with the two-component material at the flow rate and shot size required by the application.
Mixer Shrouds
Once the static mixer has been determined, the matching static mixer shroud can be selected. The shroud serves several functions, such as retaining the mixer on the dispense valve, keeping the mixer in a repeatable location, and protection in the event that the mixer is partially cured and the force of the incoming material causes the side of the mixer to burst.Simple Selection
The process of selecting the correct dispense valve for two-component dispensing applications can seem overwhelming. Simplify the selection process by having all of your material and process information available when you consult a valve expert. This will leave you with fewer worries and, ultimately, a dispense valve configured for your specific application.For more information regarding two-component dispense valves, contact the author at (734) 459-8600 or mruhlmann@sealantequipment.com, or visit www.SealantEquipment.com/Valves.