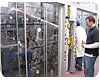
This development agreement follows a 2007 cooperation agreement and an investment by DSM Venturing in Novomer. The joint development project is expected to benefit from DSM’s market access and technologies, along with Novomer‘s CO2 polymerization technology.
Novomer will develop the chemistry and process technology for producing polymers from CO2 and propylene oxide (PO), while DSM will convert the polymers into resins and formulate them for applications such as coatings, adhesives, and graphic arts. The companies have found initial results to be encouraging and suggest that this project might lead to new and improved coatings application properties.
Once developed, the polycarbonate resin will first be used for applications such as paint, adhesives and certain inks. The resin will consist of up to 50% by weight of CO2; thus, it will not only eliminate CO2 from the atmosphere, but it will also need less fossil fuel-based raw materials and require less energy to produce than existing alternatives.
Production of the new material could begin as early as next year and, while initial volumes will be necessarily modest, it is technically feasible that the new polycarbonate resin will become a mainstream ingredient of coatings as well other applications where conventional polycarbonates are used.
Rob van Leen, chief innovation officer of DSM, said, “DSM and Novomer are looking to develop the first polymer in more than a decade to enter the mainstream of the coating industry. This exciting development may lead to a breakthrough that could change the industry. Besides cost issues, these innovative coating resins address environmental and performance issues. Therefore, they fit in perfectly within DSM’s ‘People, Planet and Profit’ approach.”
A Material Benefit for the Future
DSM and Novomer’s development project offers a fascinating glimpse into the future of manufacturing.Climate change is a reality, and forward-looking producers are hoping to replace fossil fuel-based building blocks with more efficient alternatives that reduce-and ideally avoid-greenhouse gas emissions.
This may mean developing products and processes that produce the same end result for lower GHG emissions, or a more fundamental shift away from fossil fuels in favor of biologically based materials such as plant matter. This has already resulted in biofuels and other materials that come from biorenewable sources.
While the jump from fossil fuel-based materials to biologically based materials represents one evolutionary transformation for the chemical industry, DSM and Novomer’s collaboration goes a stage further, as the polycarbonate resin being developed by the two partners actually uses CO2, which does not need to be ‘grown’ but can be extracted directly from the atmosphere.
How the Science Works
The resin is produced through a chemical process that enables polymerization using only CO2 and PO. These polymers are then converted into resins and formulated for target applications such as coatings, which is the initial target market.This conversion technology is not new; in fact, it has been around since the 1970s. The innovation comes with the combination of Novomer’s expertise in developing the catalysts to enable the polymerization and DSM’s ability to convert the polymers into resins and formulate them for particular applications, such as coatings, adhesives, and graphic arts materials. DSM’s industrial scale and market access will also be crucial in helping the new material achieve critical mass in the marketplace.
“We are very enthusiastic about our relationship with DSM, as they bring a wealth of skills and industry knowledge to help drive the commercialization of our technology,” said Peter Shepard, vice president of Business Development at Novomer. “In addition, this product development relationship with DSM leverages our ongoing technical development work that has been supported by the New York State Energy Research and Development Authority.”
While this does not mean that polycarbonate resins made in this manner will initially be competitive on a like-for-like basis with similar, traditionally made alternatives, it is possible that costs will be comparable once manufacturing economies of scale are achieved. Given that the new polycarbonate resin is expected to score highly in terms of greater performance, environmental footprint and the exclusion of bisphenol-A (a potentially harmful substance) from the resin, it is expected that production will be commercially viable.
Future Plans
For practical purposes, the companies’ plan is to use CO2 waste streams from other industrial processes rather than extract it straight from the air; however, the end result is still a reduction of CO2 in the atmosphere.This latest step by DSM marks a major milestone since the company made its initial investment in Novomer in 2007. It also reflects a wider strategy by the company to develop next-generation, high-performance products and processes with better environmental qualities while delivering significant performance improvements. To this end, along with a number of other new materials it has in development, DSM and partner Roquette will open a new bio-succinic acid operation this year in Lestrem, France. When up and running, the facility is expected to be the largest bio-refinery in Europe.
In terms of the polycarbonate resin, while application will initially focus on high-end coatings, a number of future applications could present themselves once production reaches scale.