Functional polyamide oligomers, the low molecular versions of nylons are being used in different ways in the plastic industry. Although their volume is quite a bit less than their higher molecular weight versions, which has been ranked the top 6-8 polymer on the market by volume, functional polyamides are being applied high value applications including process aids, dispersants, moldable products, self-healing polymers and many others. Recently waterborne polyurethane coatings were added to this list as several products based on N-alkylated polyamides became commercially available in the past few years.
Polyurethanes are one of the most versatile plastic materials, and their coatings represent one of the fastest growing markets worldwide in the paints and coatings industry. Their excellent durability, resistance to corrosion and abrasion, aesthetic value and structural flexibility makes them suitable for a wide range of applications.
Polyurethanes are segmented polymeric materials with alternating hard and soft segments and thanks to the nature of the chemistry that allows them to be adapted to solve challenging problems, they are one of the most versatile plastic materials. The hard segment, which is formed by the reaction of isocyanates and chain extenders creates cohesion, the soft segment, which is a low glass transition temperature oligomeric segment, provides flexibility in the material. The paints and coatings industry have many different isocyanates, but most applications use mostly three polyol types: polyesters, polyethers and polycarbonates. Other chemistries are being used or considered for specialty applications, including, polyolefins1, polysiloxanes2, polyisobutylene3-10.
Incorporation of polyamides into urethane systems has been tried in the past with limited success. The main issues were processability due to the high melting point and crystallinity of the polyamides11, but side reactions between the active hydrogen of the amide groups and isocyanates also occurred5. In some cases, polyethers or staging the polymerization12-13 helped to mitigate these issues but N-alkylated polyamides, described decades ago in high molecular form14-17 were not exploited in modern polyurethanes.
Polyamide-based polyurethanes have not yet been available commercially and their properties were largely unknown until we reported the first suitable polyols and characterized their behavior in waterborne polyurethanes18-26. Recently Lubrizol commercialized a series of coating products under the trade name Aptalon™ using polyamide polyol technology. In this paper, we show our continued work in waterborne polyurethane dispersions and also demonstrate the applicability of this technology in solvent-borne coating, epoxies and thermoplastic polyurethanes.
EXPERIMENTAL
Coatings from Reactive Polyamide Oligomers
Synthesis and Formulations
The synthesis of the polyols in this study has already been described18-26.
Solvent-borne epoxy formulations were made according to specifications. Modifications with reactive polyamide oligomers were made based on the amine hydrogen equivalent weight (AHEW) of the oligomer and the hardener.
Polyurethane solvent-borne formulations were made using Desmodur N-3200 at 1.1 NCO/OH ratios using Cyclohexanone/DB acetate 50:50 solvent mixture, BYK 333 and R-706 white pigment dispersion. Chemical resistances were determined with 16h spot tests. Samples were tested after 85 °C force drying for 1h.
Testing
Impact testing was carried out according to ASTM D2794. König hardness was determined according to ASTM D4366. Pencil hardness was determined according to ASTM D3363. Gloss was determined according to ASTM D523 Taber abrasion was determined according to ASTM D4060. Impact was measured according to ASTM D2794. Adhesion was determined according to ASTM D4541. Dry and wet adhesion were determined by crosshatch, wet adhesion was taken with no recovery time.
Chemical resistances were obtained by spot tests and the ratings were determined based on the following descriptions:
10: No effect
9: Slight loss of gloss (less than 50% by visual estimate) or slight staining
8: Significant loss of gloss (50% or more by visual estimate) or significant staining
7: Swelling has occurred, but no softening of the paint film
6: Surface softening has occurred
5: Film is significantly softened
4: Film can be removed by scrapping with dull implement
3: Film shows isolated blistering or cracking
2: Film shows significant blistering or cracking
1: Film is destroyed
Thermoplastic Elastomers from Reactive Polyamide Oligomers
Several TPU formulations were produced using hexamethylenediisocyanate (HDI), butanediol (BDO), and different polyols as soft segment polyamide diol (XPD 1000x630 or PA), polycaprolactone diol (PCL or CAPA), polytetramethylene ether glycol (PTMG), and polycarbonate diol (PC). Hard segment content in each formulation was adjusted to achieve a final hardness of 85+/-1 Shore. All formulations were produced in the laboratory by mixing all the components at 120-130 °C for around 1 minute in the presence of 40 ppm tin catalyst. The formulation details are shown in Table 1.
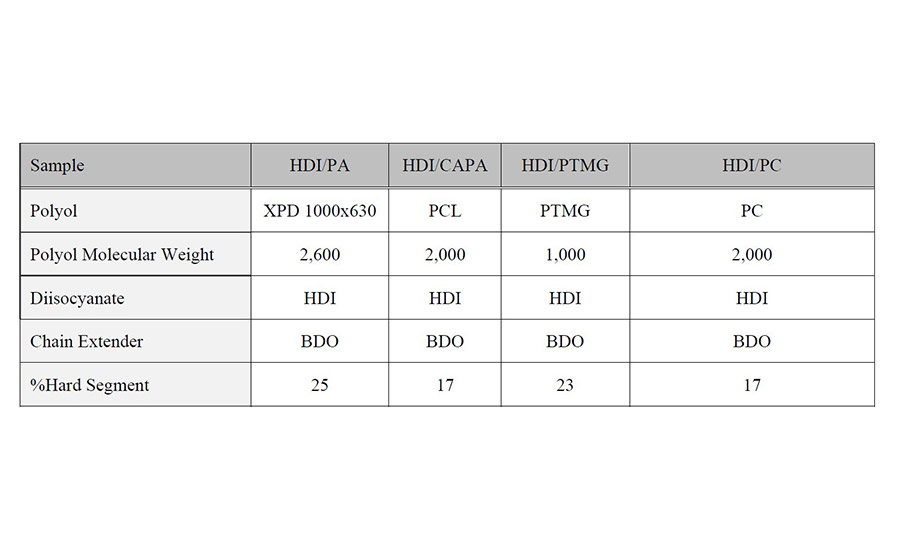
Tensile strength and elongation were measured according to ASTM D-412 and Shore hardness by ASTM D-2240. Abrasion loss was measured according to ISO 4649. Rebound resilience test was carried out under conditions described in ISO 4662; DIN 53512, with Zwick device model 5105. Haze was measured in 2 mm thick molded plaques with a digital hazemeter (BYK Haze-gard plus).
Thermal resistance of each formulation was evaluated using a dynamic mechanical analyzer and determining the temperature at which tan delta equals 1 at 1 Hz frequency and 0.2% strain, heating ramp was done at 4 °C/min from -150 °C to 150 °C.
Hydrolysis resistance was measured by exposing samples of injection molded plaques to 80 °C and 95%RH inside a climatic chamber for three weeks. Tensile strength and elongation were measured according to ASTM D-412 and retention percentages were calculated (Retention% = 100 x Aged Value / Original Value).
UV resistance was evaluated by an internal Lubrizol method using a xenotest instrument and UV-A, 10h, 80 °C, 550W conditions. Yellow index (YI) was measured with a colorimeter Color Flex A60-1010-615 according to ASTM E313.
RESULTS AND DISCUSSION
N-Alkylated Polyamide Polyols
Our focus in developing these novel reactive oligomers has been from the very beginning their use in urethane systems and one of the main challenges of incorporating polyamides into urethane systems is processability. Due to the presence of strong intermolecular hydrogen bonds, polyamide oligomers are high glass transition, crystalline polymers with high melt viscosities and poor processability at most polyurethane process conditions. Therefore, common polyamide segments made of ordinary diacids and diamines are not suitable as soft segments for the synthesis of segmented polyurethanes. We realized that polyamides without hydrogen bonds have weaker intermolecular interactions, which leads to suppressed crystallinity and lower glass transition temperature27 and that can be useful when applied in polyurethanes. N-alkylated polyamide oligomers can be synthesized by two methods, alkylating the polyamides themselves in polymer analog reactions, or using secondary amines in the synthesis of polyamides. Although polymer analog reactions can be carried out on a great variety of polyamide oligomers, they require solvents and strong alkylating agents. Preserving the end-group functionality would represent additional complications, therefore we focused our efforts on polyamides synthesized from secondary amines. Scheme 1 shows the synthesis of an N-alkylated polyamide followed by a chain end modification reaction. The amine monomer is piperazine, a secondary diamine manufactured in large quantities as a side product of ethylenediamine production.
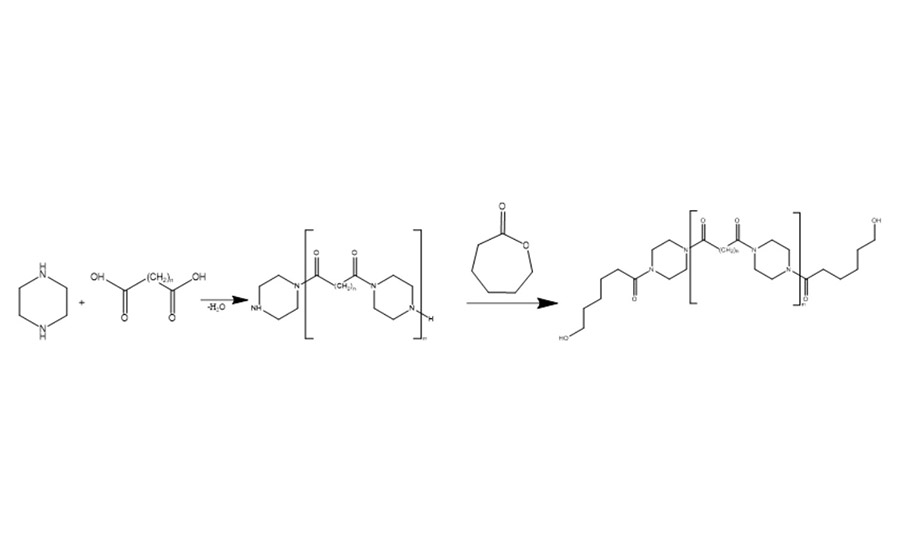
Piperazine forms N-alkylated polyamides when polymerized with diacids and is a suitable monomer for polyamides to be used in urethane systems due to its broad availability and high reactivity. The chemical industry uses several secondary diamines, most of those can be easily reacted with the majority of diacids used in polyol manufacturing; therefore, this is a very versatile synthesis method for the synthesis of N-alkylated polyamides. Depending on the monomer used in excess, the oligomer is amine or acid terminated. Although both potential end groups react with isocyanates, neither of them is the most common functionality used in the polyurethane industry. Isocyanates react with secondary amines slower than with primary amines, however, the rate is still too rapid for most, if not all processes, moreover the formed linkage is a higher melting point and more solvent-resistant urea, which exacerbates the processability issues. Primary alcohols are used more commonly, and we developed several chain-end modification methods that lead to primary alcohols. One of them is the reaction of caprolactone with secondary amine end group, which yields primary alcohols with high efficiency (80-98% primary alcohol end-groups). Although the caprolactone reacts significantly faster with most secondary amines than with primary alcohols, esters also form in small quantities. The reaction is essentially complete in about 8-24 hours at 180 °C. In the presence of alcohols, amines and amides, transesterification and transamidation may occur as well. Therefore, at longer reaction times the reaction can reach a thermodynamic equilibrium between the amide hydroxyl end group reaction and the ester amine end group reaction. In the case of piperazine and aliphatic diacid monomers this is not changing the conversion of the amine to hydroxyl reaction significantly due to the higher relative stability of the amide group.
Low viscosity and low glass transition temperature are essential for good processability in urethane systems and the elimination of hydrogen bonding in polyamide polyols leads to the desired properties. Table 2 shows the viscosity of different molecular weight polyamide polyols with and without sebacic acid comonomer at 60 °C.
![Viscosity of amine-terminated poly(piperazine dimerate-co-sebacate) (see reference [18]) and hydroxylterminated poly(piperazine-dimerate) (see [18]) at 60 °C at different molecular weights. Brookfield viscosity values were obtained at 5 rpm using spindle 6.](/ext/resources/ASI/2023/oct/lubrizol/Table-2.jpg)
Typical processing temperatures in urethane systems are 70-200 °C and the table shows that although the higher polarity sebacate-dimerate copolymer has significantly higher viscosity than the poly(piperazine dimerate) oligomer, they both have quite low viscosities even at 60 °C, which is a good indication of excellent processability for most coating and thermoplastic elastomer applications. At higher temperatures, the viscosity drops sharply as expected from a low molecular weight polymer due to the breaking of the weak secondary interactions from the polar non-hydrogen bonding amide groups and the much weaker hydrogen bonds of the end-group alcohols/amines28. The above described poly(piperazine dimerate) is a good representation of N-alkylated polyamide oligomers, but the scope of this technology is much broader: just like in the case of polyester polyols, a large number of mono and polyacids can be combined with the secondary di- or polyamines to modify the molecular weight, the crystallinity, the glass transition temperature, the functionality, the branching, and various other properties of the N-alkylated polyamide polyol. Although we have started to evaluate the physical and chemical properties of these novel materials, most compositions remain unexplored and at this point only a few are offered commercially, which are listed in Table 3.
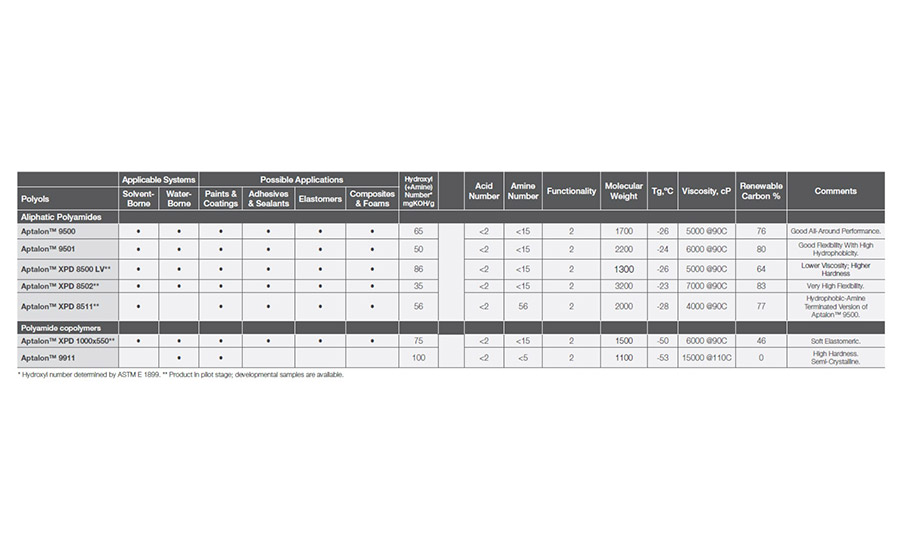
Waterborne Urethanes of N-Alkylated Polyamides
Polyurethane coatings have several different forms, solvent-borne, moisture cure, waterborne, solventless systems, etc. Due to their lower solvent requirements and low overall toxicity levels, waterborne resins have been growing consistently faster than other polyurethane coatings in the industry. Waterborne urethanes are colloidal systems with 30-300 nm particles stabilized in water. One of the main differences compared to the two-component (2K) urethanes is that they possess fully extended high molecular weight polymer chains and a built-in dispersant to stabilize the solid particles in water. Scheme 2 shows the basic components of waterborne polyurethanes. Although the above-described polyamide polyols may be used in various polymeric structures, including epoxies, powder coatings, UV-cured compositions, and many others, we primarily explored this technology in urethanes and coating applications. Urethanes used in other applications including elastomers, foams, adhesives, and sealants have essentially the same chemistry as in coatings however, the differences in compositions, processes and additives can be significant and our findings below may or may not be reflected in those applications.
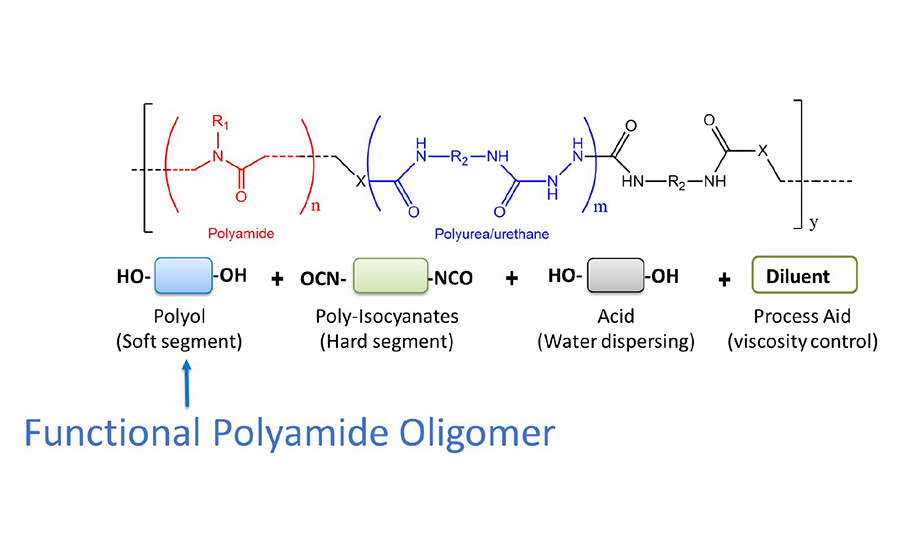
The synthesis of waterborne polyurethanes has two stages, the prepolymer stage and the dispersion stage. In the prepolymer stage, the hydroxyl terminated components, the polyol and the dispersant are reacted with the isocyanates. Although the carboxylic groups can react with isocyanates, the temperature of the prepolymer is controlled to a level where this is minimized to avoid crosslinking and reduction in acid functionality. The limitation in reaction temperature often necessitates the use of diluents or processing aids, since even low molecular weight polyurethanes can build up prohibitively high viscosities. Diluents and processing aids can be solvents that remain in the dispersion (N-methylpyrrolidone), solvents that are removed at the end of the process (acetone) or reactive diluents that can be polymerized at a later stage (acrylics). At the end of the prepolymer stage the dispersant acid is neutralized with a tertiary amine and the dispersion stage starts. During dispersion, the prepolymer forms particles with the hydrophobic polymer chains aggregated inside the particles surrounded by the hydrophilic charged acid groups, which stabilize the particle in a waterborne system. The mole ratio of acid groups throughout the polyurethane chain compared to the soft and hard segments combined dictates the size of the particles produced and influences several coating application properties. After the dispersion of the prepolymer the oligomeric urethane is extended with a diamine to build molecular weight.
The soft segment has a significant effect on various key performance parameters beyond the mechanical properties. Figure 1 shows the structure of the most used soft segments along with the novel polyamide polyol.
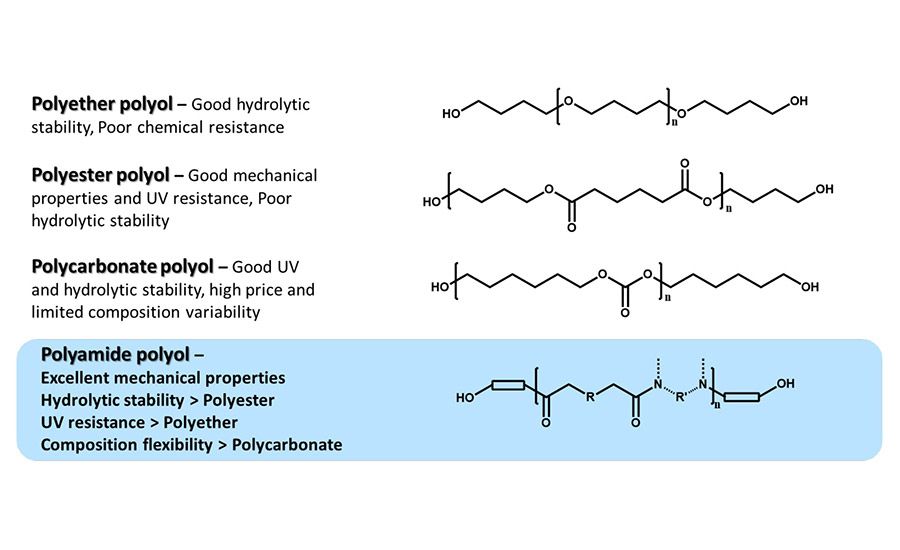
Polyester based polyols are the most common choice for most coatings having the largest market share; their urethanes have excellent mechanical properties, good UV resistance but they are hydrolytically unstable. Polyesters are versatile and various aspects of the polyols can easily be controlled by monomer composition, including crystallinity (extent and melting point), hydrophobicity, viscosity, aromaticity, etc. Polyethers are used if high flexibility/elongation or better hydrolytic resistance is needed but they suffer from poor heat, and chemical resistance. Only a few polyether versions are available commercially. Polycarbonates are useful polyols for UV-resistant polyurethanes but their sensitivity to certain chemicals can be a drawback.
We wanted to understand how polyamides are different from the commercially available polyols therefore we started a series of studies where we synthesized and characterized waterborne polyurethanes different only in their soft segment compositions18. Figure 2 shows one of such experiments depicting the stress strain curves of polyurethanes prepared with polyester, polyether, polycarbonate, and polyamide soft segments.
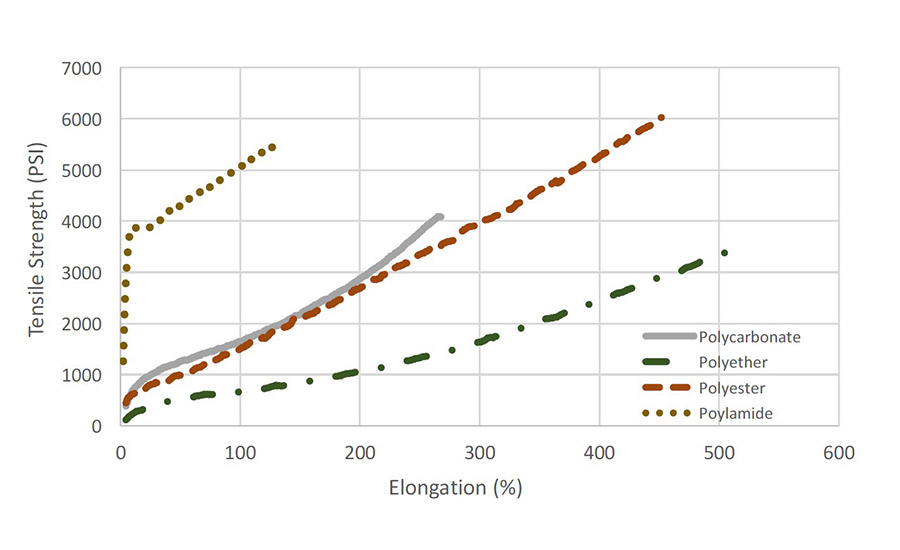
The polyamide-based polyurethane shows high modulus and strength and lower elongation compared to the other samples. This can be explained by the high phase mixing between the polar polyamide soft segment and the hard segment, which leads to lower ultimate elongation and higher tensile strength. Although a material with this type of tensile-elongation curve is not suitable for low modulus elastomers, it can be beneficial for protective applications where a coating needs to absorb and dissipate mechanical energy from impact.
In recent years, N-alkylated polyamide oligomers have been incorporated into several waterborne coating products, which have been marketed under the Aptalon trade name. The list below contains some of the most important characteristics of these products and their intended markets.
Aptalon W8060 – Clear waterborne self-crosslinking polyurethane dispersion
- Performance matching or exceeding 2K waterborne finishes without the need for external cross-linkers
- Excellent hardness, and extremely durable – great scratch, abrasion, and chemical resistance, renewable content 35%
Aptalon W8030 – Self matting waterborne self-crosslinking polyurethane dispersion
- Natural, matte appearance – 60° gloss less than 15 with no matting additives30
- Superior hardness and abrasion resistance compared other low gloss systems
Aptalon M8100 – Pigmentable waterborne self-crosslinking polyurethane dispersion
- Superior hardness, durability, and chemical resistance that outperforms competitive WB systems
- Capable of high gloss levels
Aptalon 8080HS – High solids waterborne self-crosslinking polyurethane dispersion
- 50% solids content that forms hard films (vs 35 – 40% for most conventional urethane dispersions)
- Reduces number of coats needed and coating dry time, renewable content 35%
Aptalon M8120 – Waterborne self-crosslinking polyurethane dispersion
- High performance one-component waterborne direct-to-metal (DTM) coating with superior hardness and durability31
- True DTM adhesion - greater protection from a single coat system
- Corrosion resistance comparable to market leading DTM systems
Although these have been formulated for a variety of applications, due to the unique chemistry of the soft segments, they all share some common properties, which originates in the N-alkylated polyamide component.
One such property is hydrolytic resistance: polyamide-based urethanes resist hydrolysis and have comparable hydrolytic resistance to polyether-based urethanes. In polyesters, the equilibrium is shifted towards the reactant side, the diol and the diacid and given enough time and the ability to equilibrate, a polyester will depolymerize completely even in the presence of small quantities of water. In the case of the amide groups, the equilibrium is shifted towards the amide, and it takes excess of water to hydrolyze polyamides.
Regarding chemical resistance, nylons typically have excellent barrier properties and we saw similar behavior for polyamide-based urethanes. Chemical resistance in pure polyamides is due to the extensive hydrogen bonded network connecting the backbones. All amide groups are great hydrogen bond acceptors, but hydrogen bond donor groups may or may not be present in polyamide polyols, which is necessary to create a hydrogen bond network. However, when copolymerized with isocyanates, the formed urethanes/ureas provide hydrogen bond donor groups that can interact strongly even with N-alkylated amide groups essentially recreating the hydrogen bond network present in pure polyamides.
We found that the hardness of polyamide urethane can be high due to the strong compatibility between the polyamide polyols and the hard segment, polyamide urethanes have by far the highest hardness among all urethanes and although the difference is smaller, they have better mechanical properties across the board as well.
The heat resistance of polyamides, particularly aromatic polyamides exceeds other urethane soft segment chemistries, polyesters, polyether, and polycarbonates. This is evident in the pure form of the polymers as well, i.e., without urethane.
The polarity of the amide group usually leads to improved adhesion to more polar substrates. This effect is taken full advantage of in hot-melt adhesives, which often contain smaller urethane segments and amide linkages. We found that the adhesion benefit of N-alkylated amide structure represents itself in crosslinked polymers with higher urethane content as well, albeit to a lesser extent. Thus metals, metal oxides, wood, polar plastics like epoxies, phenolics, etc., show good adhesion to polyamide-based urethane coatings.
Solvent-Borne Coatings of N-Alkylated Polyamides
In recent years solvent-borne (SB) urethane coatings have been under constant regulatory pressure due to their high VOC content, however they still represent one of the largest coating markets. Requirements for the most demanding coating applications can often be met only with the use of SB urethanes. We found that solvent-borne formulations of N-alkylated polyols have good solubility and low viscosity in typical solvents of the industry, and they can be formulated similarly to acrylic or polyester based urethanes. Surprisingly, SB formulations were quite tolerant to the presence of hydrogen bonding polyamides if they were accompanied by molecular segments that efficiently disrupted the crystallinity of the polyamide oligomer or were dissolved in solvents that effectively eliminated their interactions. The application testing of these materials revealed that SB polyamide coatings generally outperformed WB polyamide urethanes most likely due to better film formation under the force drying condition and the fact that WB components (dispersants, diluents, etc.) with adverse effects were not part of the formulation. Tables 4A and 4B show the mechanical properties and chemical resistance of polyamide-based solvent-borne urethanes with a performance balance similar to solvent-borne acrylics or competitive polyols.
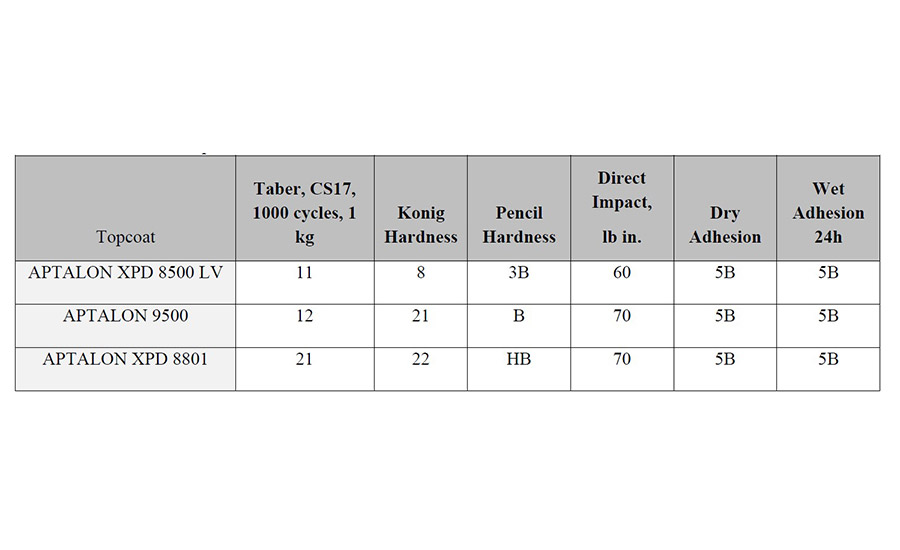
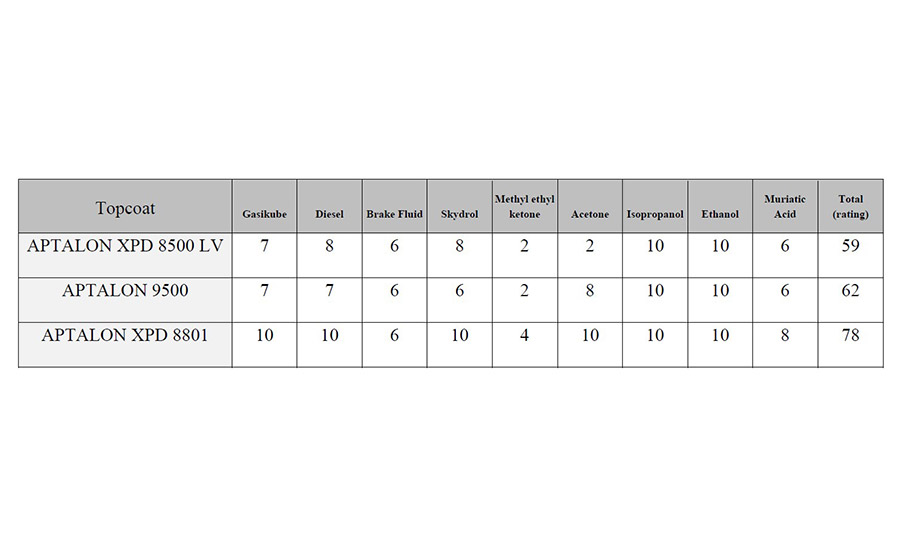
Table 4A and 4B: The mechanical properties and chemical resistance of solvent-borne polyamide-based polyurethane coatings. Films were made with drawdown at 3 mils thick. Values have a range of 1-10, higher is better and the total rating for a resin is the sum of the ratings for various chemicals (see the chemical resistance rating guide in the experimental section).
Oligomeric amine hardeners are often used in epoxy coatings. However, these are typically high AHEW components intended to balance the formulation for resistance related properties, hardness or curing rate adjustments. The amine functional versions of the oligomers we discussed before have a much higher molecular weight and are more suitable to act as a soft segment of the epoxy coating, much like it does in polyurethanes. A concept study with APTALON XPD 8511 showed that the “flexibilizing” effect is measurable although some properties of the original epoxy coating deteriorated slightly (see Table 5A and 5B).
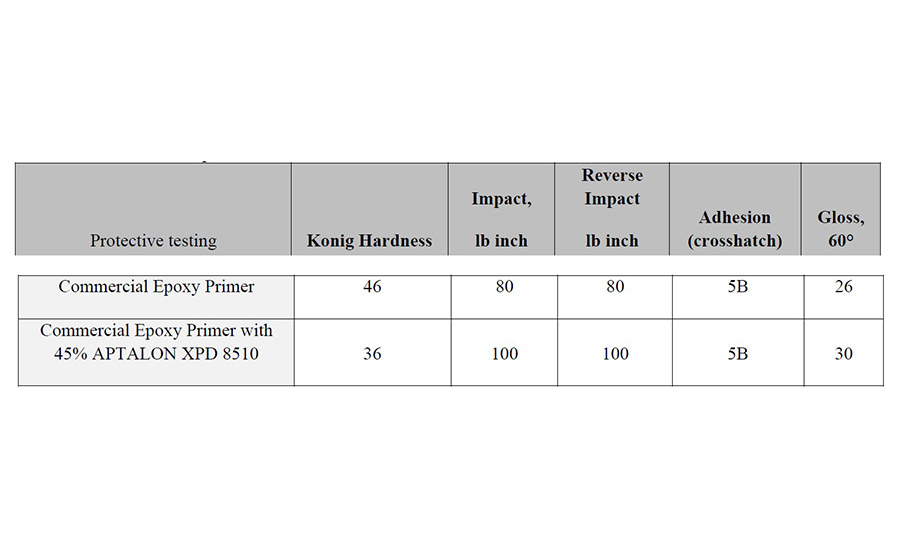
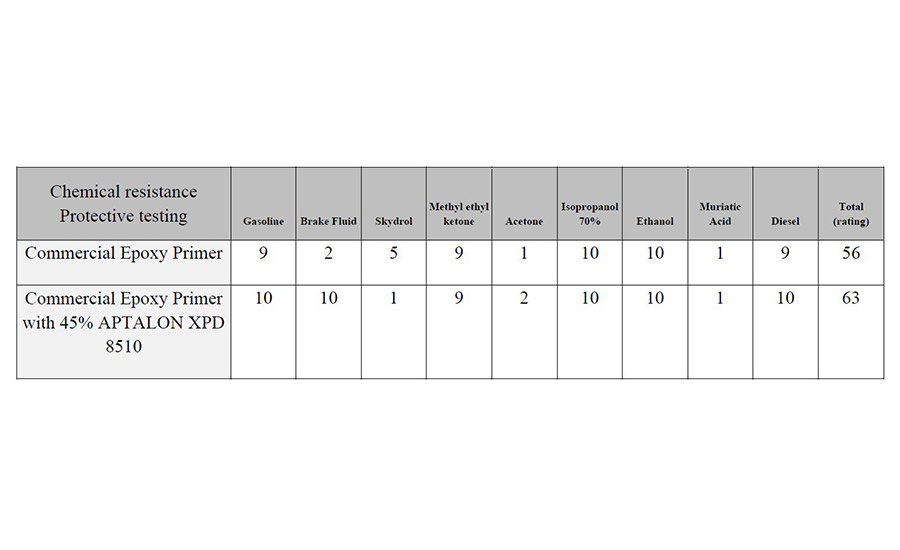
Table 5A and 5B. The mechanical properties and chemical resistance of solvent-borne polyamide-based polyurethane coatings. Films were made with drawdown at 3 mils thick. See the chemical resistance rating guide in the experimental section. Values have a range of 1-10, higher is better and the total rating for a resin is the sum of the ratings for various chemicals.
Polyamide-Based Thermoplastic Elastomers (TPUs)
Thermoplastic polyurethanes (TPU) are useful materials well known in the art. They are generally prepared by reacting a polyisocyanate with a polyol and optionally a short diol (called chain extender). The resulting materials have many useful properties and are used in a wide variety of applications. When aliphatic diisocyanates are used, the resulting TPUs are light stable and provide high durability without discoloration in outdoors applications. TPUs contain hard segments and soft segments, where the soft segments are typically polyester-, or polyether-based. TPUs made from polyester polyols render good mechanical properties and UV and heat resistance, but they suffer from poor hydrolysis resistance. Polyether polyols have better hydrolytic stability than polyester polyols but fall short in UV and heat resistance. Polycarbonate polyols offer improved hydrolysis and thermal resistance over polyester polyols with some degree of increased hardness. There is an ongoing need for TPU materials that have the expected useful properties20, but which also provide improved hydrolytic, oxidative and/or thermal stability.
Hydroxyl terminated polyamide oligomers were made with low viscosity, low glass transition temperature, suppressed crystallinity, low acid number, with various nitrogen or amide:hydrocarbon weight ratios (or hydrophilic/hydrophobic balance), with a controlled number of hydrogen bonding or non-hydrogen bonding amide groups. The new polyamide diols were explored for the production of aliphatic TPUs, and their properties were compared to those achievable with common commercial polyol diols. In the present study, the polyamide polyol XPD 1000x630 was used, which is the higher molecular weight version of the polyamide APTALON XPD1000x550 listed in Table 3.
Table 6 shows the mechanical properties of the new polyamide-based TPU compared to the TPUs of the other polyols. Abrasion loss and rebound resilience values for the new TPU are very similar to the values with other polyols as those properties are highly determined by the hard segment type and content.
When comparing tensile strength, we can observe a lower value in the polyamide-TPU. However, a post annealing treatment at 120 °C for 24 hours led to a much higher tensile strength due to an increased level of hard segment crystallinity that developed during the treatment. This transition did not occur with other polyols or was minimal.
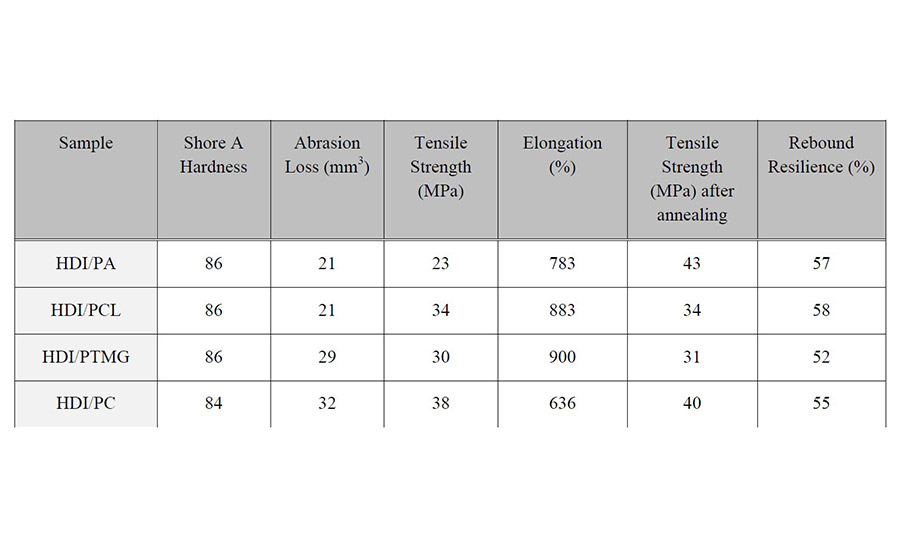
Injection molding was done using an Engel injection machine 50T L=23D 3:1, and molded parts were produced with dimensions 120x120mm and 2mm thickness. During the injection molding process, the total cycle time was determined by adding the times for each of the four stages involved in the production of the molded plaques: clamping, injection, cooling and ejection (see Table 7). In Aliphatic TPU grades, cycle time is highly dominated by the time required for the cooling of the part inside the mold cavity until the material is fully solidified.
The new aliphatic TPU with polyamide diol showed a 20% reduction of the total injection molding cycle time as compared to other polyol technologies. This allows for a higher productivity and efficiencies during parts manufacturing. In addition, the new polyol showed a lower haze percentage that indicates a more transparent appearance.
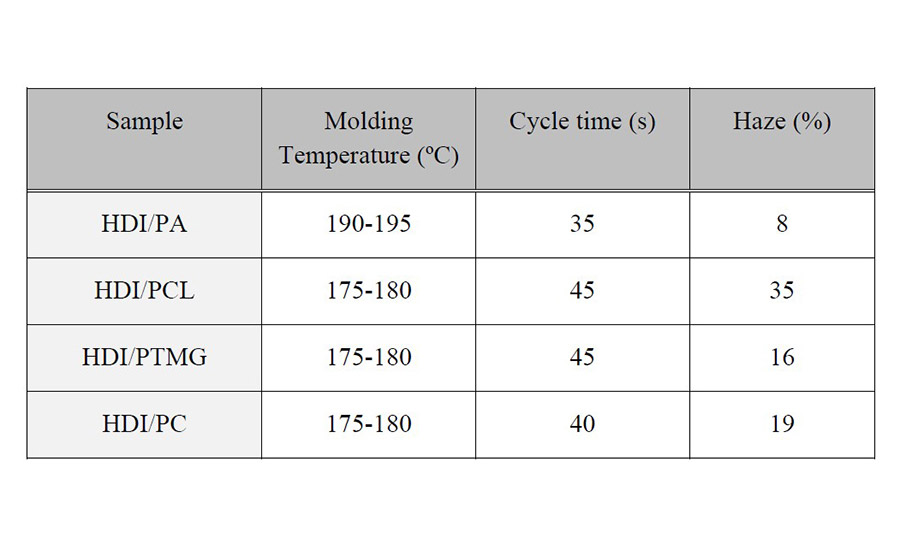
Dynamic Mechanical Analysis was used to evaluate the low and high temperature behavior of the new TPU. As can be clearly observed in Table 8, the polyamide-based TPU outperforms polycarbonate-based TPU in heat resistance while adding better flexibility. The high temperature difference between Tan Delta Peak and Tan Delta=1 can be understood as a higher phase separation happening in the polyamide-based TPU which can only be partially explained by the higher molecular weight of the polyamide polyol.
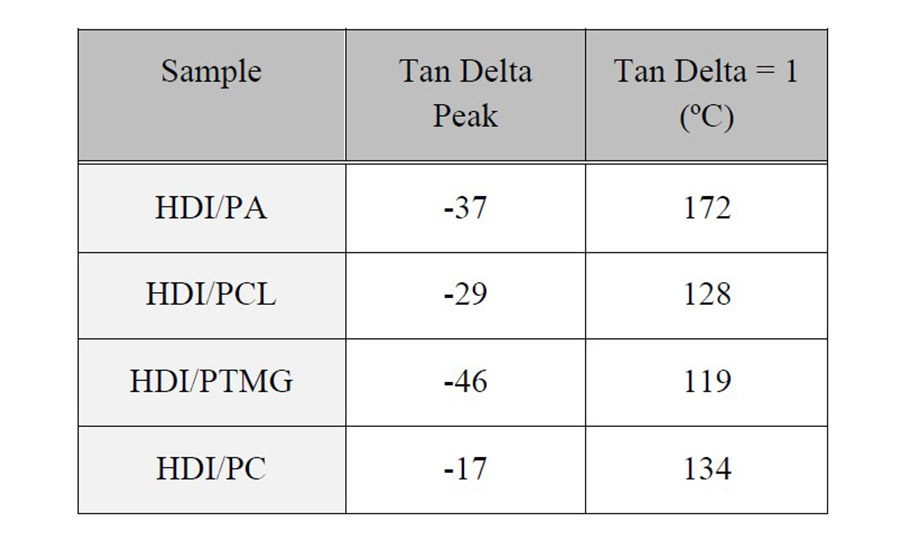
Weatherability data is necessary for the selection of materials to be used in outdoor applications and the main weathering forces that may cause material degradation are sunlight, temperature changes and moisture. Since aliphatic polyurethane grades are mostly formulated for exterior applications, the weatherability was a highly relevant property to test for.
Table 9 shows the color measurements, as yellow index, before and after exposure of the samples to xenon arc test. The test was carried out at 80 ºC with a 340 nm lamp (550 Watts). A slight improvement in the yellowing tendency under UV radiation was observed in the new polyamide-based formulation as can be understood by the lowest YI value obtained after irradiation when compared to other polyol technologies.
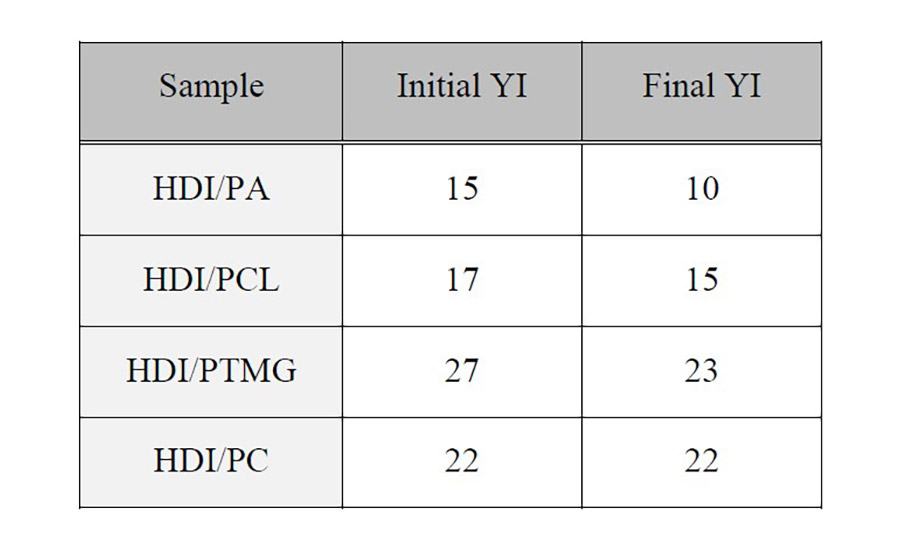
Finally, samples were tested in a climatic chamber at 80 ºC and 95% RH for several weeks. Tensile strength was evaluated after each week to determine the loss of mechanical properties. As expected, the best hydrolysis resistance was achieved in the polyether-based TPUs due to the lack of labile linkages. The polyamide-based TPU still provided much better hydrolysis resistance than the ester-based counterpart, retaining approx. 70% of tensile strength after three weeks. The degradation of the polyamide-based TPU can be explained by the presence of ester linkages that may still be present between amide and ether blocks in the polyol.
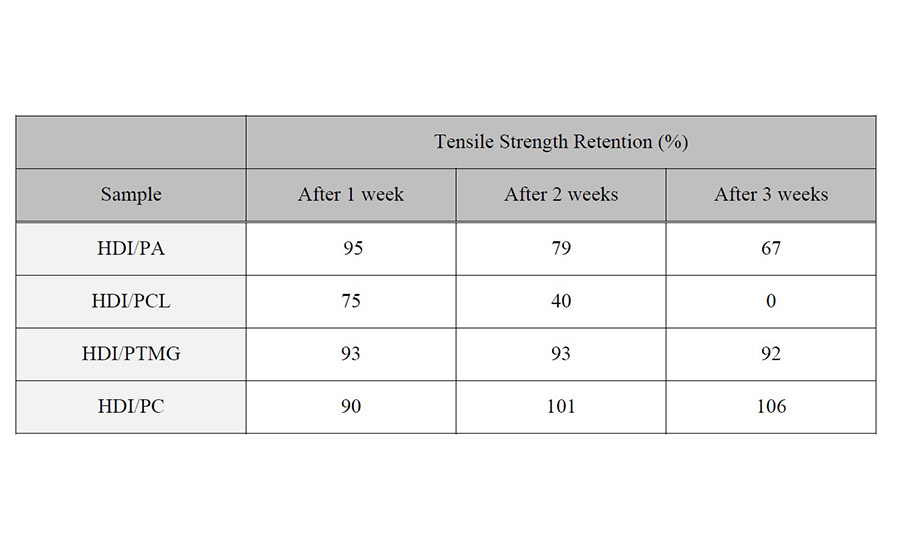
CONCLUSION
Novel N-alkylated polyamide polyols were developed with low viscosity and good processability. The applicability of the polyamide polyols was explored in solvent-borne, thermoplastic elastomer and waterborne urethane systems. A series of novel waterborne polyurethane/urea copolymer dispersions were synthesized by incorporating polyamide segments into the backbone of polyurethanes. The films of the resulting resins were characterized and compared to urethanes of other polyols. We found that the new segmented copolymers exhibit outstanding properties for coating applications with the performance advantage most pronounced in hydrolytic stability, chemical resistance, hardness and adhesion. The properties of commercialized polyamide urethane coatings were discussed for wood and metal coating applications. Potential use in demanding coating applications, where conventional polymers fail to meet some of the performance requirements is suggested.
New polyamide-based thermoplastic elastomers were described and found to have a unique set of properties not achievable with any other commercial polyol. The combination of high resistance when exposed to UV light and moisture, and the high melting temperature and low glass transition temperature enables a broad service window and excellent weathering resistance. The new polyamide polyol also offers a substantial reduction of the molding cycle time with the subsequent manufacturing efficiencies. All these characteristics will grant the possibility of introducing new specialty aliphatic TPU technologies that fulfill the most demanding requirements for outdoor applications.
Learn more at www.lubrizol.com.
“Reactive Polyamide Oligomers for Elastomeric, Adhesive and Coating Applications” 2022 Polyurethanes Technical Conference 05-07 October 2022, National Harbor, MD, USA, Published with permission of CPI, Center for the Polyurethanes Industry, Washington, DC.
References:
1. Padsalgikar, A.D., US20180298139 (2007)
2. Omietanski, G.M.; William, T.C., US3384599A (1964)
3. Jewrajka, S.K.; Kang, J.; Erdodi, G.; Kennedy, J.P.; Yilgor, E; Yilgor, I., J. Polym. Sci., Part A: Polym. Chem., 47, 2787–2797 (2009)
4. Jewrajka, S.K.; Kang, J.; Erdodi, G.; Kennedy, J.P.; Yilgor, E.; Yilgor, I., Polyisobutylene- based polyurethanes. II. Polyureas containing mixed PIB/PTMO soft segments. J. Polym. Sci. A Polym. Chem., 47: 2787-2797 (2009),
5. Kang, J.; Erdodi, G.; Kennedy, J. P., From Journal of Polymer Science, Part A: Polymer Chemistry, 49(18), 3891-3904 (2011)
6. Kang, J., Erdodi, G. and Kennedy, J.P., J. Polym. Sci. A Polym. Chem., 49: 2461-2467. (2011)
7. Kennedy, J. P.; Erdodi, G.; Kang, J., WO 2011060161 (2011)
8. Kennedy, J. P.; Erdodi, G.; Jewrajka, S., WO 2010039986, (2010)
9. Kang, J.; Erdodi, G.; Brendel, C.M.; Ely, D.; Kennedy, J.P., Journal of Polymer Science, Part A: Polymer Chemistry, 48(10), 2194-220(2010)
10. Erdodi, G.; Kang, J.; Kennedy, J. P., Journal of Polymer Science, Part A: Polymer Chemistry 48(11), 2361-2371, (2010)
11. Locko, G.A.; Palvin, M.S.; Harman, N.W.; Robinson, D.D.; Astrologes, G.W., WO 2008/070762
12. Takeichi, T.; Suefuji, K.; Inoue, K., Polymer Journal, 34/6, 455 (2002)
13. Menovcik, G.G.; DePue, J.S.; Turner, H., EP 0595281 (1993)
14. Wittbecker, E. L.; Houtz, R.C.; and Watkins, W.W., "Elastic N-substituted polyamides." Industrial & Engineering Chemistry 40.5, 875-879. (1948)
15. Klebanskii, A. L.; Vilesova, M. S., Zhurnal Obshchei Khimii, 28, 1777-81. (1958)
16. Klebanskii, A. L.; Vilesova, M. S., Zhurnal Obshchei Khimii, 28, 1772-6. (1958)
17. Klebanskii, A. L.; Vilesova, M. S., Khimicheskaya Nauka i Promyshlennost, 2, 660 (1957)
18. Erdodi, G.; Pourahmady, N.; Ta-Yuan Lai, J., WO 2014126739 (2014)
19. Erdodi, G.; Pourahmady, N.; Ta-Yuan Lai, J.; Pajerski, A.D., WO 2014126741 (2014)
20. Pourahmady, N.; Makal, U.G.; Erdodi, G.; Ta-Yuan Lai J., US9809675 (2014)
21. Erdodi, G.; Ta-Yuan Lai, J.; Pourahmady, N.; Skoff, I., WO 2016099726 (2016)
22. Pajerski, A.D.; Erdodi, G.; Pourahmady, N., WO 2016100201 (2016)
23. Erdodi, G.; Pourahmady, N.; Yang, Y.; Bird, J.; Skoff, I.; Rota, D.; Blevins, L.; Pajerski, A. D., WO 2016025300, (2016)
24. Erdodi, G.; Pourahmady, N.; Bird, J.; Skoff, I.; Swech, C., EP3615590 (2016)
25. Erdodi, G.; Nagvekar, D.S.; Schroeder, K.; Pourahmady, N.; Pan, Y.L., WO 2016025319 (2016)
26. Erdodi, G.; Pourahmady, N.; Bird, J.; Skoff, I.; Swech, C., WO 2018201143, (2018)
27. Liu, X.; Wang, Y.; Wang, Z.; Cavallo, D.; Müller, A.J.; Zhu, P.; Zhao, Y.; Dong, Y.; Wang, D., Polymer, 188, 122117, (2020)
28. Macromolecular Engineering Design, Synthesis and Application of Polymers, 2021, Editors: Alex Lubnin, Gabor Erdodi, eBook ISBN: 9780128232576, Paperback ISBN: 9780128219980
29. Musche, N.; Erdodi, G.; Bird, J.; Skoff, I.; Pourahmady, N.; Gibson, R., European Coatings Journal, (7-8), 24-28, (2017)
30. Pourahmady, N.; Erdodi, G.; Gibson, R.; Musche, N.; Bird, J.; Skoff, I., Farbe + Lack, 123(8), 42-47, (2017)
31. Erdodi, G.; Halstead, J.; Li, X., Farbe und Lack (2019), 125(4), 22-27.