As demand for electric vehicles (EVs) grows, adhesive tapes continue to play an important role in the engineering and manufacturing of EVs. Adhesive tape technology contributes to the safety, reliability, and performance of EVs, as well as helping with weight reduction and manufacturing efficiency. Additionally, adhesive tapes offer design flexibility, conforming to complex shapes and surfaces. For the EV market, ATP offers customers the opportunity for off-the-shelf solutions or bespoke developments.
Electrical Insulation Films
For cell wrapping, single-sided self-adhesive PET films can help with electrical insulation. With thin adhesive coating weights less than 20 gsm if necessary, these films offer breakdown voltage insulation values more than 8kV and a CTI (Comparative Tracking Index) of more than 600V. Moreover, these self-adhesive PET films could be used to electrically insulate other metal parts within the battery module as well. Different product thicknesses and tape colors are available, and customer-specific die-cuts can be realized. Additionally, double-coated films can be combined with other materials to achieve electrical insulation.
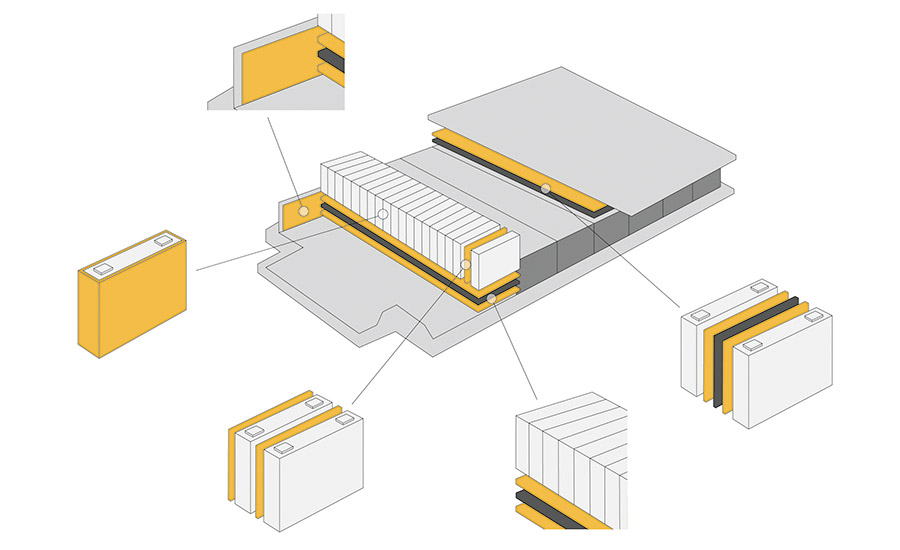
Thermal Runaway/Barrier Material Mounting
For thermal runaway insulation, lightweight double-sided PET or tissue tapes can be coated on both sides with permanent adhesive, or one-side-permanent, one-side-semi-permanent, to aid recycling at end of life. Suppliers of thermal runaway systems rely on mica, glass-fibers, ceramic fibers, and other materials protecting and bonding to cells, modules, and battery packs. ATP’s tapes for this application are suitable for rough, uneven surfaces.
Compression Pad Bonding
Tapes for installation of intercellular compression pads can be thin adhesive coatings less than 50 gsm to suit individual customer requirements. The benefits of using tapes in such applications are guaranteed coating weight, instantaneous bonding, and high suitability for automatic assembly. In contrast to liquid adhesives, these tapes require no curing time.
Component Mounting
For mounting of components within the battery module such as busbars, sensors, cables, and absorber fleeces, self-adhesive tapes can provide support during the application.
Cell-to-Cell Bonding
Double-sided adhesive tapes can be used for bonding of cell housings within the battery stacking process (cell-to-cell bonding). Different coating weights and carriers are available.
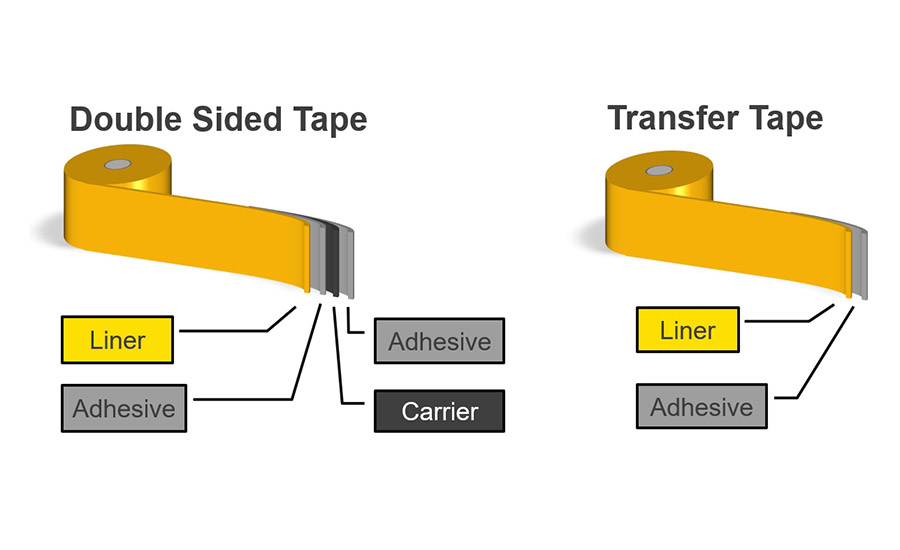
Thermal Interface Materials (TIM)
With thermal interface materials (TIM), customers can buy converted articles including solvent-free thermally conductive films, which act as thermal interfaces between the top and bottom of the battery cell and cooling plates. These films offer thermal conductivity of up to 3W/ mK and high dielectric strength. These TIM pads are silicone-free.
Flame retardant tapes
A range of halogen-free pressure-sensitive tapes are available that can be classified as zero burn according to FMVSS302 and VTM-0, and according to UL-94. UL 94 is the Standard for Safety of Flammability of Plastic Materials for Parts in Devices and Appliances; it is a plastics flammability standard released by Underwriters Laboratories in the United States. The standard determines the material’s tendency to either self-extinguish or spread the flame once the specimen has been ignited. FMVSS 302 specifies the burn resistance requirements for materials used in the occupant compartments of motor vehicles (i.e., passenger cars, multipurpose passenger vehicles, trucks, and buses).
As a long-term and experienced partner to the automotive industry and with a global supply network in more than 60 countries worldwide, the ATP Group is at the forefront of adhesive tape innovation for use in the production of electric vehicle powertrains.
Learn more about ATP Group at atp-ag.com.
Image within this article are courtesy of ATP Group.