In today’s modern environment there is a wide range of applications for silicone release liners with pressure-sensitive adhesives, ranging from release labels to diaper closures, medical applications (e.g., wound dressings), building insulation, and health and beauty products.
Release liners are part of a composite made of — a label with its own adhesive on a facestock facing the release coating on a liner. The release coating allows easy delamination or easy label transfer from the liners onto the object to be labeled.
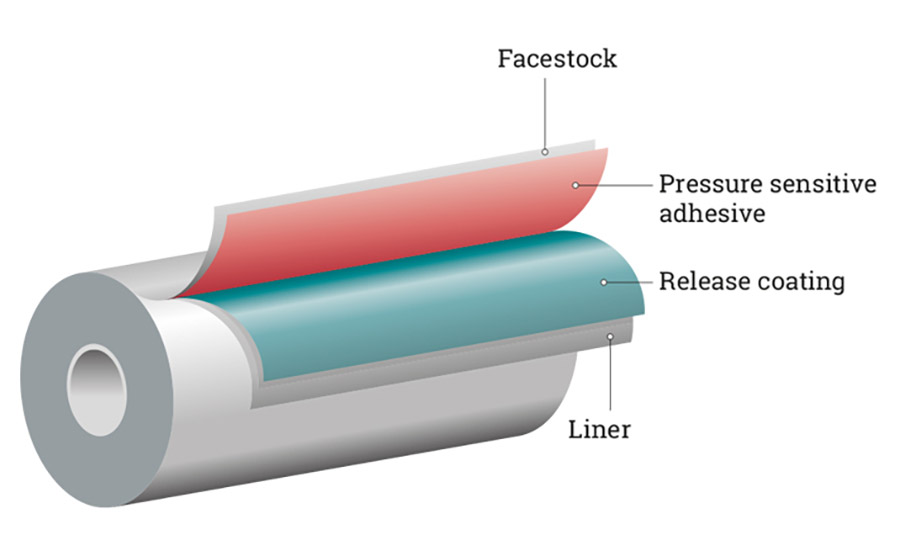
In its simplest form, a release coating is a liquid or solid that forms a weak boundary layer between two potentially interacting substrates. This boundary layer prevents intimate contact and the resulting development of adhesive strength. Any transfer of release agent should not hinder use of the separated surfaces.
There are several chemical types of materials that can be used as a release coating — such as polyacrylates, carbamates, polyolefins, fluorocarbons, chromium stearate complexes, and silicones. Silicones enjoy a unique position because they can be applied and cured into a polydimethylsiloxane (PDMS) network on various backing substrates,limiting migration; They also allow substantially lower release forces than other materials.
Properties for Optimum Release Characteristics
One of the key properties of silicone is its low surface tension. This is a consequence of low intermolecular forces and high chain flexibility. Unlike more rigid carbon-carbon backbones, PDMS polymers, because of their backbone flexibility and because at room temperature they are substantially above their Tg, can easily expose their low interacting/surface active methyl groups to provide low adhesion; or in other words, low release forces against adhesives they are exposed to.
Adhesives used on labels cannot easily wet such a low-energy silicone surface, as there are no groups to interact. This results in ease of delamination and ease of transfer of the label from the liner to its point of use.
But low surface energy is not the only aspect to consider. Even fluorocarbons, despite a lower surface energy than silicones, do not match silicone release performance. Another key component is the rheological behavior of the cured PDMS network applied onto the backing substrate. This rheological behavior helps in developing interfacial slippage in the systems, which plays a key role in the low release values observed on the release of pressure-sensitive adhesives from silicone-release-coated liners.
A high degree of slippage (low friction) is cited as the predominant reason PDMS has lower release force than the lower surface energy (but higher friction) fluorocarbon polymers.
Chemistry of Silicone Release Coatings
Silicone release coatings are typically available in four different categories:
a. Solvent based
b. Solvent free
c. Water-base emulsion
d. UV curable
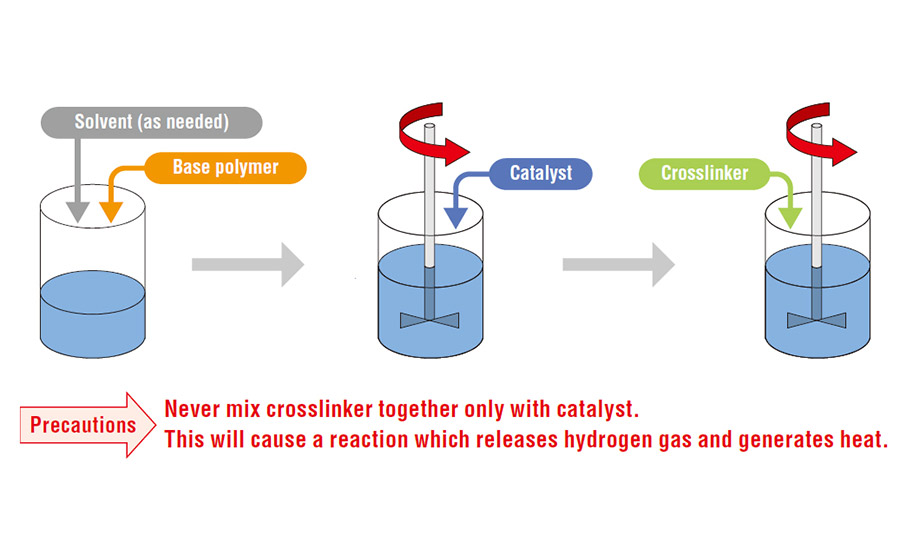
All the above four categories, except the UV curable systems, are cured using the addition cure mechanism, wherein the base polymer reacts with a crosslinker in the presence of a catalyst.
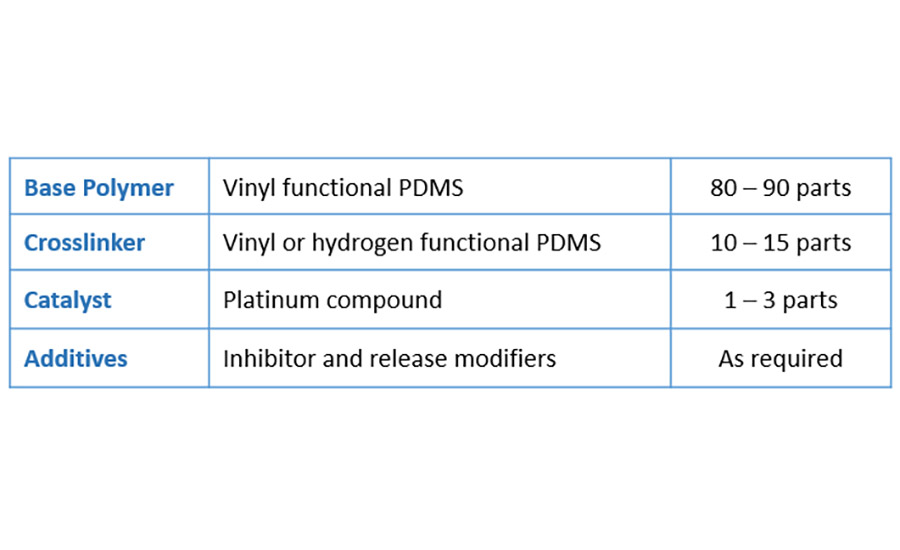
Curing of the silicone polymer is an important process due to the following reasons:
- Prevents silicone migration
- Increases cohesive strength of the release coating to resist pull force from the adhesive layer
- Improves adhesion with the substrate layer
- Facilitates quick drying
Cure Chemistry
To achieve cross-linking of the silicone release coating, the most predominantly used chemistry is via a hydrosilylation reaction. Typical composition of such silicone release coating consists of:
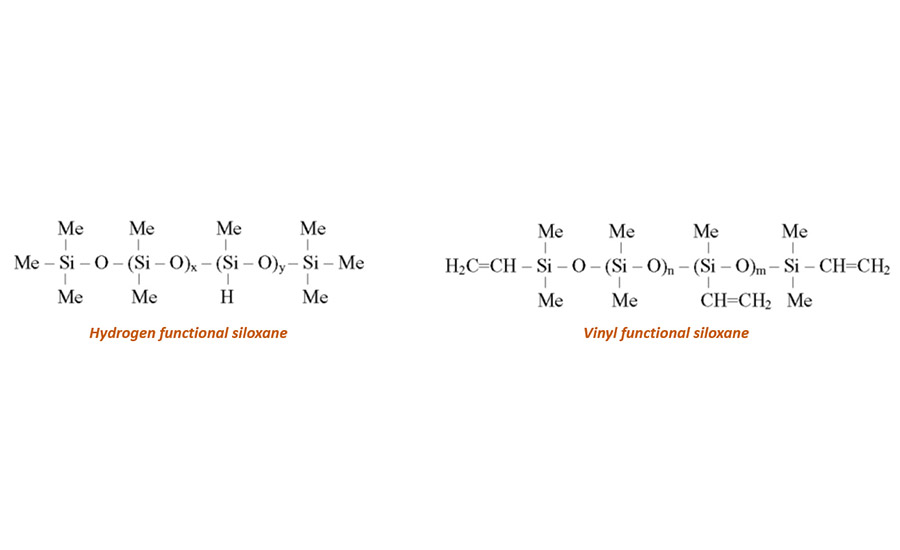
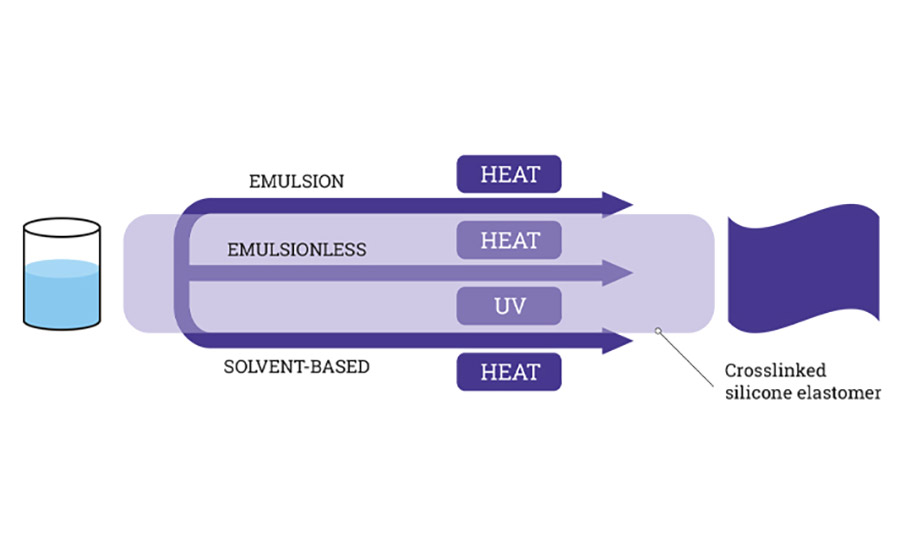
Hydrosilylation is the addition reaction of a silane group (SiH) on a vinyl group (SiCH=CH2) catalyzed by a noble metal such as rhodium or most often platinum. There are basically two different forms of this cure chemistry used industrially, both catalyzed by platinum.
- SiH-functional polymer reacts with a vinyl-functional polymer carrying Si-CH=CH2 groups
- SiH functional polymer reacts with a hexenyl functional polymer carrying Si-CH2-CH2-CH2-CH2CH=CH2 groups
In the hexenyl-based system, the unsaturation has been distanced from the polymer backbone and is therefore less sterically hindered. This allows a release coating material with a slightly faster cure upon application.
Associated with these two different forms of cure chemistry (vinyl or hexenyl), various inhibitors can be used to ensure sufficient bath life and prevent premature cure at room temperature of the coating mixture prior to use and curing. Inhibitors compete with the initial step of the hydrosilylation reaction and the addition of the unsaturated group from the polymer on the platinum catalyst. So, the selection of the platinum inhibitor has a major impact on cure speed. Typical inhibitors employed here are acetylenic alcohols such as 1ethynyl,1-cyclohexanol or fumarate- or maleate-based inhibitors.
Factors to Consider When Selecting Silicone Release Coatings
Many factors influence the selection of coating technologies and materials for liners and laminates. These include end-user requirements like converting, die-cutting and printing requirements, and environmental concerns. If using silicones, some factors are related to them, some not.
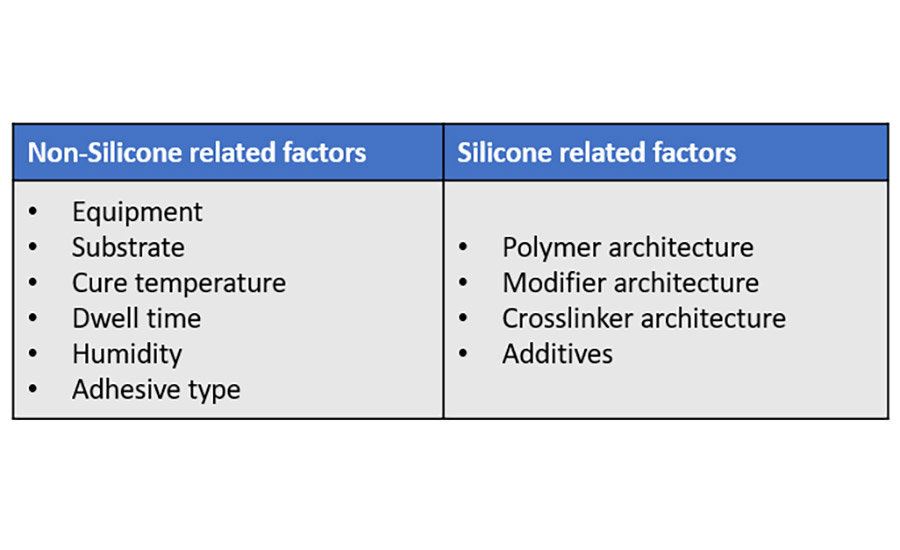
The equipment used may drive the choice of release coating material. The most commonly used are either based on a three-roll differential offset gravure or a five- or six-smooth-roll coating head. Environmental and regulatory pressure may play a role as well, encouraging the selection of solventless or emulsion systems to deliver the required performance.
Substrate type, cure temperature, dwell time, and humidity can affect cure and anchorage of the silicone coating to the substrate. The selection of adhesive required for the application also has a major bearing on release and anchorage characteristics.
In recent years, the use of plastic liners such as polyethylene, polypropylene, or polyester films has increased. Siliconizing such substrates is a challenge because of their low resistance to high temperatures and their variability, as they may contain additives such as antiblocking agents or stabilizers. Some of these are detrimental to the cross-linking of the silicone release coating. But overall these thermoplastic films are difficult substrates as they show poor adhesion and sometimes poor silicone cure to the applied coating.
Formulation Advice
Crosslinker : Coating ratio
Good cure can be achieved with formulations containing from 0.25 to 1.2 percent crosslinker, by weight, based on the silicone coating as supplied. Note that while raising the level of crosslinker (SiH:Vi ratio) in a formulation can bring about more complete or faster cure, it can also raise the potential for adhesive interaction and reduced bath life.
Catalyst
To reduce the temperature of cure or to obtain faster or more complete cure, you may incorporate up to 0.5 weight percent of catalyst. In extreme cases, such as film coating where very low cure temperatures are required, up to 1.0 weight percent silicone solids of catalyst may be added to the coating bath.
Platinum addition should be undertaken with care. The higher the level of platinum in the formulation, the greater the potential for serious bath life reduction. Acrylic lock-up problems may be exacerbated, as well.
The platinum catalyst is sensitive to contamination by compounds containing nitrogen, sulfur, tin, phosphorus, arsenic, antimony, selenium, tellurium, and by some residual solvents or monomers.
Anchorage Additive
To improve anchorage of silicone coatings to difficult paper substrates, incorporate 0.8 to 2.0 weight percent anchorage additive.
Process Solvents
Excellent results have been obtained using ethyl acetate, toluene, hexane, heptane, and white spirits. Solvent choices should be evaluated due to their possible impact on both bath life and cure rate.
To prevent catalyst poisoning and inhibition of cure, handling equipment, transfer pumps and piping, solvents added to the bath or used during cleaning procedures, and the substrate to which the coating will be applied must be free of the above-mentioned contaminants.
Additional information about Texochem is available at https://texochem.com.
Images within the article courtesy of Texochem.
References:
1. Silicone Release Coatings for the Pressure Sensitive Adhesive Industry. S Cray. Dow Corning.
2. Labels and Labeling. Silicone release liner technology.
3. Pressure Sensitive solutions. Dow Corning. Release system Information guide.
4. Silicone Release Coatings for the Pressure Sensitive Industry – Overview and Trends. Dr Alex CM Kuo.
5. Technology of Pressure Sensitive Adhesives and Products. Taylor and Francis. Silicone Release Coating
Technology. Loretta Jones.