A custom machine original equipment manufacturer (OEM) in Canada saw an opportunity in the automotive manufacturing industry and created its own line of robotic pressure-sensitive tape applicators. The new product from Innovative Automation, RoboTape™, is helping tape manufacturers expand business as pressure-sensitive tapes replace more traditional methods of joining, such as riveting.
The robotic pressure-sensitive tape applicator can apply tape faster than humans, up to 10 inches per second, offering better repeatability and less waste than manual application. Robotic application is a favored solution for addressing labor shortages.
From its founding in 1989, Innovative Automation focused on custom automation for the automotive sector, later diversifying into sectors like medical devices and consumer goods. Twenty-five years later, Innovative’s growth allowed for the creation of a small Research and Development (R&D) department. "We always thought it would be great to create a serial (standardized) product," said Michael Lalonde, president, and co-owner of Innovative Automation with CEO Stephen Loftus. "Then we saw an opportunity."
The opportunity arrived when Innovative built a robotic foam taping machine for a customer. That machine operated in steps. First, it pre-cut the tape, and then the robot picked up the pre-cut tape and applied it. Lalonde and a colleague began brainstorming innovations that would allow the company to leverage the experience gained from that project and create a serial machine.
Lalonde remembered, "We looked at each other and said, 'If we could make the tape cut in the robotic head in order to create a seamless and lightning-fast applicator, we'd have a winner.'" One seamless motion meant that tape would have to be routed. "We knew that automotive was the largest market using tape for noise and vibration reduction, sealing and bonding components," Lalonde continued. "Plus, there was a lot of interest from industries such as architectural, appliances, HVAC, and aerospace in tape. There were many market opportunities for this product."
And so, the RoboTape development initiative was born. "Our goal was to develop a flexible tape system that could work for a variety of applications with little to no modifications. We focused on understanding our customer base and what they need now, and will need in the future," said Zac Cutt, lead machine designer.
Innovative identified two areas where inventive engineering was required. Most pressure-sensitive tapes, whether for joining, insulating, bonding, or glazing, are applied manually. A robotic applicator would be a major productivity and labor savings improvement.
Current technologies in the automated taping sphere have limitations. Some can only apply one type of tape or only tape in straight lines or must be purchased with a particular robot. Others use pick-and-place technology, which can damage the tape and is slow. If the tape supply is mounted on the robot, production must stop whenever a fresh supply is needed. Tape mounted on the robotic head requires robust robots and large cells.
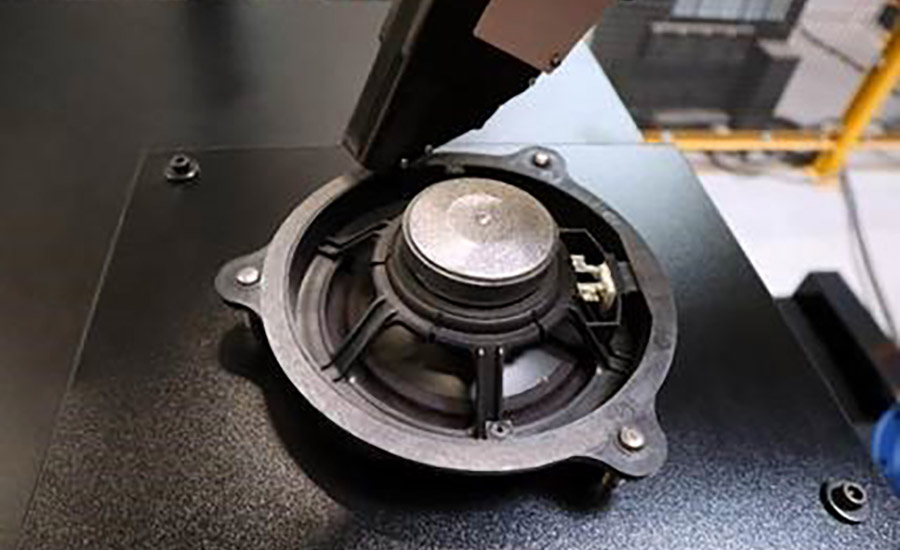
Each RoboTape can be programmed with multiple recipes, for single- or double-sided flat, foam, or felt adhesives. The tape path can range from simple to complex with gradual or sharp curvature. Developing a software interface that consisted of a large number of parameters, recipes, speeds, and feeds, using various tapes with their subtle differences, was a two-and-a-half-year project.
The robotic pressure-sensitive tape applicator's versatility flows from a decision early on to distance the tape supply from the robot. Tape is contained in a mobile cabinet. The cabinet can accommodate large 1,800 m (5,900 feet) wound spools and allows production to continue during a spool change. Remote tape feeding was the biggest design challenge but offered the most customer benefit. With remote tape feeding, the R&D team minimized the size and weight of the end effector, allowing the end effector to swivel in any direction and still dispense tape. The end effector can be operated from a fixed position or mounted on any articulated robot, even a cobot. The robotic pressure-sensitive tape dispenser is agnostic about which robot model customers use.
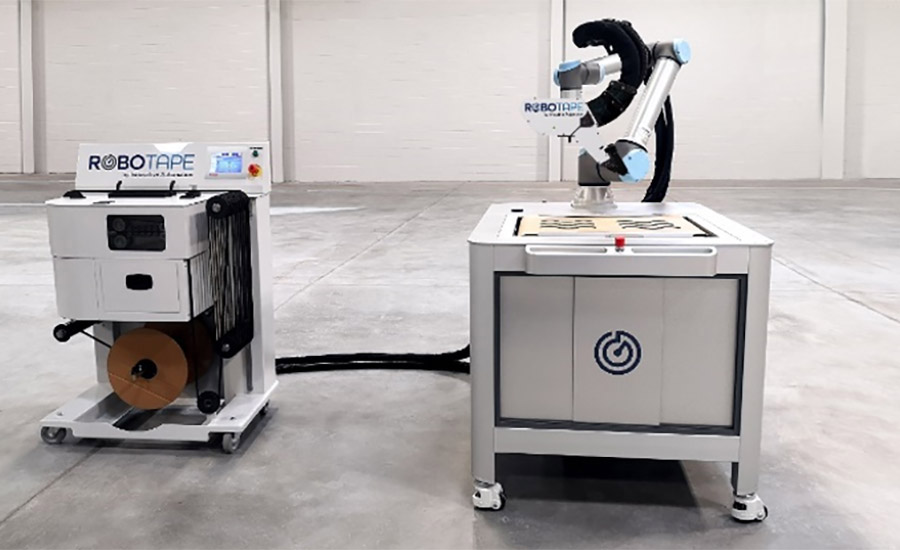
A patented system delivers the tape to the end effector, which performs the peel/affix/cut functions. The system also returns the discarded adhesive liner to the payout for easy disposal. Since the payout will almost always be positioned outside the robot’s safety zone, a new spool can be loaded and spliced without interrupting production.
Pneumatics Is Essential to Success
“Much of our effort was in trying to save space with compact components that could also supply high force,” said Cutt. “We also needed high speed and cost competitive components. Pneumatics checked all these boxes. We discussed pneumatic solutions with Festo, a world leader in pneumatic and electric automation. Festo’s first suggestion was to apply the DMSP fluidic muscle to actuate the tape cutter.”
"Much of our effort was in trying to save space with compact components that could also supply high force," said Cutt. "We also needed high speed and cost competitive components. Pneumatics checked all these boxes. We discussed pneumatic solutions with Festo, a world leader in pneumatic and electric automation. Festo’s first suggestion was to apply the DMSP fluidic muscle to actuate the tape cutter."
The fluidic muscle is a completely new kind of pneumatic drive. The muscle consists mainly of a hollow elastomer cylinder embedded with aramid fibers. When the fluidic muscle fills with air, it increases in diameter and contracts in length, enabling a fluid, elastic movement. Using the fluidic muscle enables motion sequences that approach human movement, not only in terms of kinematics, speed, and strength, but also in sensitivity. The fluidic muscle can exert 10 times the force of a comparably sized pneumatic cylinder. It also is up to 30% lighter than cylinders with comparable force ratios. Reduced weight was one of the design imperatives for the end-of-arm tool. And the fluidic muscle is durable. The original muscles installed in RoboTape beta units in mid-2020 are still in use after more than 10 million cycles. Because of its closed design, the pneumatic fluidic muscle can be used under extreme conditions, such as in sand or dust.
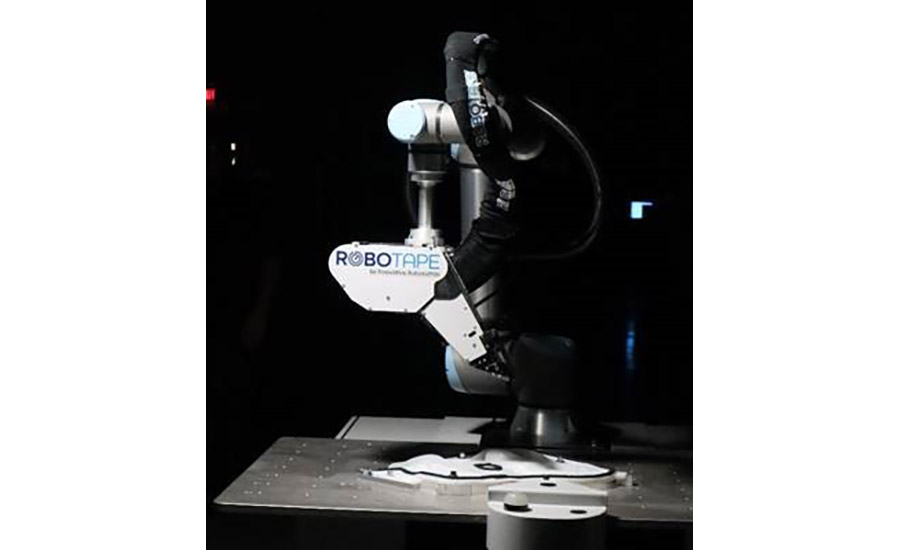
Festo also recommended its new-generation compact valve terminal, the VTUG. The VTUG offers up to 48 valves in the space normally required for 24. It is machine mountable, which brings the valves closer to the actuators and improves response time. Other space-saving Festo components include the DSNU-S compact cylinder and VRPA pressure regulator. Like the fluidic muscle, these components fit snuggly in minimal space, enabling the end effector to maintain its slim profile. The DSNU-S reflects Festo’s focus on addressing the need for miniaturization in machine design. It’s 40% slimmer and 35mm shorter than a DSNU ISO cylinder but is compatible with many of the same applications.
Soon after the robotic pressure-sensitive tape dispenser’s introduction, the company realized that the market for such a product was larger than expected. Among the companies taking an interest in the product was 3M. What followed was months of testing to see if the dispenser could be compatible with 3M products. The robotic pressure-sensitive tape dispenser exceeded 3M’s requirements for a tight start/stop tolerance and an acute bend radius. In the end, the product met 3M’s 5-point performance checklist that includes limited tape stretch, accurate tape wet out, splice identification and disposal, successful liner handling, and repeatable tape placement accuracy.
For 3M, a collaboration provided the opportunity to sell more tape, said Lalonde. "They’re competing against other joining technologies like riveting and gluing and fastening that have been automated for 30 or more years. It’s tough to switch a customer from one of those to tape and revert to a manual process for something they’ve been doing with automation. RoboTape gives 3M the opportunity to offer the same level of automation as those other technologies, but with the cost and performance benefits of tape."
A sales collaboration was formed. The collaboration extends RoboTape’s sales and marketing reach via the 3M tape sales force and by exhibiting with 3M at trade shows.
Learn more about Innovation Automation at www.innovativeautomation.com.
Images within the article courtesy of Innovative Automation.