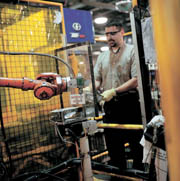
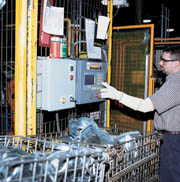
LSC is an independent stamping company that manufactures and assembles hundreds of different parts for automotive manufacturers in North America and Mexico. The company recently installed the new robotic metering workstation to apply a bead of sealant on gas tank filler necks. The new station features a Graco PrecisionFlo™ LT electronic metering and dispensing system. It replaces a manual application that, according to Harnish, was labor intensive, wasteful, and resulted in an unacceptable number of rejects. "We had reached the limit of our capabilities with the manual system. We were operating three shifts, around the clock, seven days a week. It was necessary that we develop a new application method in order to meet our customers' increased production and quality requirements, as well as to meet our target costs."
The manual application required the operator to load a part onto a fixture and manually apply a bead of sealant onto the parts flange with a hand dispenser. The other half of the filler neck would be placed on top of the part with the bead and they would be pressed together to seal the two parts. The two details were then welded. A second person had the chore of wiping the excess material from the assembly.
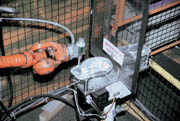
The new PrecisionFlo LT system has eliminated these problems. It dispenses a precise, consistent bead along the edge that completely seals the two parts.
"We haven't had a single reject since we installed the new controlled application system," says Harnish. "We're obtaining the same pattern, dispense rate and volume dispensed every time - part after part after part. It's precise and consistent."
This consistency also means LSC is using less material and has reduced its waste. Being a QS 9000 and ISO 14001 company, LSC keeps records on material usage and reports they've cut the amount of material dispensed at this workstation by 60%. Waste material generated from wiping the excess sealant from around the part, as well as disposing of the rags used to wipe this material off, has been eliminated.
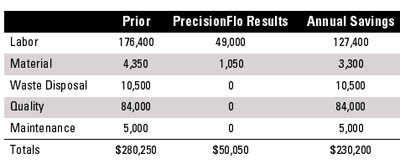
According to Harnish, this has proved important because orders for the filler necks have increased. "We would have had to add another workstation and more manpower to handle the increased workload if we didn't have the Graco PrecisionFlo LT."