
An idealized hot-melt adhesive formulation is comprised of polymer, tackifier, diluent and performance additive (see Figure 1). The diluent may be one or more waxes, oils, plasticizers or processing aids. Such materials may include Fischer-Tropsch, paraffin or microcrystalline wax, polyolefin homopolymer or copolymer, polybutene, or napthenic process oil. Polyolefin homopolymers and copolymers, such as Honeywell’s A-C®polyolefins, are compatible with HMA components and may also offer synergistic improvements by reducing the migration of other adhesive components. Modified or functional polyolefins that have polar characteristics based upon their oxidation, copolymerization, or post-modification are particularly effective at low-use levels. Typically, a use level of 1-5% of an A-C performance additive can also be used to enhance wetting and adhesion, improve cohesive strength, provide rheology control, modify the set speed, and improve heat resistance. In summary, low-molecular-weight synthetic polyolefin waxes can be used as simple low-viscosity diluents or as multifunctional high-performance additives.
A typical wax is a solid at room temperature and can be hard or soft. All waxes will melt without decomposition above approximately 40°C. Wax characteristics include low viscosity above the melting point, low molecular weight, polishability with slight pressure, insolubility in water at room temperature, and crystallinity. The microarchitecture of a synthetic wax may be linear or branched, may include copolymers and modified polyolefins, and may be semi-crystalline imparting a high or a low density, dependent upon crystallinity.
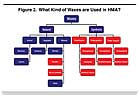
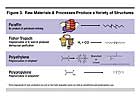
Polymerization of ethylene to produce adhesive raw materials can result in either low- or high-density polyethylene of various molecular weights. The polymer molecular weight and branching control the resultant viscosity, rheology, and density of the material. Low-density polyethylene is branched and may have branches upon branches in a random distribution. High-density polyethylene is an essentially linear polyethylene structure.
Polymerization of propylene results in polypropylene homopolymer of various molecular weights dependent upon processing conditions. Polypropylene may be used as a homopolymer additive in HMA, or may be copolymerized or post-reacted to form functional materials that blend well and add desirable performance enhancements to the HMA due to their combination of hardness, heat resistance, and adhesive qualities.
One of the most important copolymers for use in adhesives is ethylene vinyl acetate (EVA), which is produced by the copolymerization of ethylene and vinyl acetate. Honeywell manufactures low-molecular-weight EVAs with different levels of vinyl acetate to provide compatibility with various adhesive formulations and promote adhesion to a variety of substrates. At very high vinyl acetate levels, the resulting copolymer can be especially useful in low-melt adhesives and can increase permanent tack in pressure-sensitive adhesives.
Another important ethylene copolymer for use in adhesives is ethylene acrylic acid (EAA), where ethylene and acrylic acid are copolymerized to form the EAA copolymer. Honeywell manufactures low-molecular-weight EAAs with different levels of acrylic acid to give excellent “stick and grab” and aggressive tack to difficult substrates while providing compatibility with a variety of adhesive formulations. In addition, at the highest acrylic acid levels, these materials are water-dispersible, thereby increasing their utility in certain applications.
One of the most effective functionalization routes for additives used in adhesives is oxidation. Homopolymers or copolymers may be oxidized to form molecules of increased polarity relative to their initial composition. The resultant oxidized molecule has a random distribution of polar functionality including acid, alcohol and ester groups, which are randomly placed along and at the end of the polymer chain. Oxidized polyolefin products, such as those in the A-C®line, include low-density polyethylene, high-density polyethylene and oxidized copolymers, such as oxidized ethylene vinyl acetate. Oxidized products are described by their acid number, a measure of their acid functionality that is reported in milligrams of potassium hydroxide required for neutralization per gram of product.
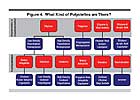
Ionomers result from the metal salt neutralization of ethylene acrylic acid copolymers (EAA). Ionomeric additives can use any one of a variety of cations at various levels of acid neutralization. Thus, the acid functionality on the molecule may be partially neutralized, resulting in an ionomer still containing a level of acid functionality, or the cation may replace 100% of the acid functionalization resulting in a fully neutralized ionomer having no acid number. Honeywell’s AClyn®ionomers can function as low-molecular-weight analogs of ionomer polymers or as adhesion promoters in adhesive formulations.
In summary, the table in Figure 4 outlines the synthetic routes for polymerization and functionalization of polyolefins. The variety of A-C synthetic polyolefin additives available, combined with a variety of microarchitectural and polar structures, offer adhesive formulators many options. Why and how these materials should be selected for specific adhesive formulations will be discussed next month in the second part of this article.
For more information, contact Natalie Merrill, Honeywell International Inc., 101 Columbia Road, Morristown, NJ 07962; phone (973) 455-6309; e-mail Natalie.Merrill@Honeywell.com ; or visit www.honeywell.com/adhesives.
A-C® and AClyn® are registered trademarks of Honeywell International Inc.