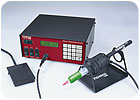
Figure 1. The dispensing system consists of a gun and a control unit, which can be programmed to dispense exact volumes of solder paste. Once the data has been entered, a technician needs only to activate the gun with a foot pedal or a finger switch.
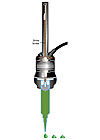
Figure 2. The LDS dispensing gun incorporates a linear-actuator-driven lead screw that threads through a nut. When the gun is activated, the nut rotates between electrically charged poles, causing the non-rotating screw to move up or down linearly, depending on the rotation of the nut. In dispensing paste, the screw moves downward and the plunger at the end of the screw "pushes" the programmed amount of solder paste through the dispense tip.
The linear drive system is just that: a system. The dispensing gun, which can be either held in the hand or mounted to a frame, is the working tool, while the control unit is the “brains” that automatically ensures the precise amount of output from the gun each and every time it is triggered. For the technician, operation of the system has two components: a) programming of the control unit with the essential data, and b) the dispensing of the paste through an actuator switch (typically a foot pad, though a finger switch attached to the syringe can also be used, if preferred).
The first step is to select a dispensing gun that provides the required volume of paste (above 0.001cc, 0.0005cc to 0.001cc, or 0.00025cc to 0.0005cc) for the application. The proper syringe (or barrel reservoir) is then attached to the dispenser and locked in place with a retaining ring, and a dispense tip is installed.
The next step is to program the control unit, which calculates the distance the plunger must travel forward in the syringe for the correct shot size. Because the paste is dispensed volumetrically, temperature and viscosity are irrelevant to the process (unless, of course, the material is so dense or dried out it cannot be moved through the tip). To prevent dripping of paste from the tip after a deposit, a drawback can be programmed in that will cause the material to recede slightly within the tip.
Using screen prompts, the key data to be programmed in are: the syringe dimensions (inner diameter and length); desired dispense volume and rate; drawback; and drawback delay. Once the data are entered, the software does the rest by calculating the “steps” forward and backward to produce the exact dispense amount required, each step being either 3.5 or 7.5 degrees in rotation, depending on the selected gun. A manual mode is available for potting and beads, while an automated mode enables repeated and consistent output for multiple-dot-type requirements.
What does the technician need to do next? Nothing, except position the gun for dispensing and press the foot pedal or the finger switch... or in the case of mounted dispensers, simply activate the system.
For more information, contact Fishman Corp., www.fishmancorp.com.