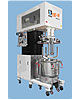
Dual-shaft mixer with three-wing anchor and rotor/stator.

Dual-shaft mixer with three-wing anchor and multiple saw-tooth disperser blades.
These single-shaft devices face a common limitation- viscosity. When batch viscosity rises, localized heating can occur in the area surrounding the blade as product turnover starts to slow down. Meanwhile, materials close to the vessel walls become stagnant and do not benefit from the agitation in the vessel. Eventually, losses from inefficiency, prolonged batch times or poor product quality become too significant to ignore. If any of these mixing problems occur in your process, it is time to consider upgrading to a multi-shaft mixer.
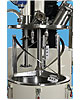
Agitation system of a multi-shaft mixer featuring a three-wing anchor with helical flights and Teflon scrapers, as well as a saw-tooth disperser with slinger to prevent batch material from climbing up the high-speed shaft.
Multi-Shaft Mixers
Multi-shaft mixers comprise two or more independently driven agitators working in tandem. A low-speed anchor complements one or two high-shear devices. On its own, a saw-tooth disperser blade will produce acceptable flow patterns for products up to around 50,000 centipoise (cP); a rotor/stator’s recommended viscosity limit is even lower, around 10,000-20,000 cP. Thus, there is a need for a supplementary agitator to improve bulk flow and deliver viscous product to the high-shear devices.The addition of an anchor agitator allows a multi-shaft mixer to process formulations that are several hundred thousand centipoise. The most common low-speed anchor designs have two or three wings. For added efficiency-especially in terms of axial flow-the anchor can be modified to feature helical flights in between adjacent wings, or the vertical wings can be entirely replaced with helical ribbons supported from the top and bottom.
The anchor provides a means for agitating product near the vessel surface. The horizontal and vertical wings are designed to run at close proximity to the vessel walls. This, in itself, helps to constantly remove product from the sidewalls and bottom so that fresh material can fill those areas. However, as shown in Figure 1, the use of scrapers, which actually contact the vessel surfaces, significantly increases heat transfer efficiency (especially in cooling operations).
Aside from the improved capability of multi-shaft mixers over single-shaft devices from a viscosity and heat transfer standpoint, another design advantage is that they are closed systems and can offer benefits in vacuum mixing. When processed under vacuum, certain adhesives and sealants develop higher densities and achieve better tensile properties as a result of improved shearing and contact of the different components. With other adhesive formulations, vacuum mixing keeps entrapped oxygen to a minimum, which ensures longer shelf-life and improved stability.
Mixing under vacuum also eliminates unwanted air voids that can be produced through agitation under atmospheric conditions. Pulling vacuum during mixing eliminates costly downstream de-aeration steps and shaves overall processing time.
It is fairly common for multi-shaft mixers to function as specialized reactors. In many cases, the efficiency of mechanical mixing has a decided influence on percent yield and end product properties. Multi-shaft mixers are effective in this aspect because the reactants are constantly kept homogenous, and the reaction environment can be carefully controlled for temperature, level, pressure, etc.
To illustrate, let’s look at a case of a one-part urethane sealant formulation that begins with isocyanates and polyether polyols. A company developing such a product used a laboratory reactor to produce the prepolymer for the sealant and used a separate bench-top mixer to prepare the final product. When the time came to scale up for commercial batches, the company’s engineers began looking into glass and steel production reactors. While comparing costs and performance, it occurred to them that a reactor (whether it is a tank, tube or kettle) does not perform any function other than containing the reaction.
Using a 300-gal Ross VersaMix Multi-Shaft Mixer that they already had on site, the company prepared a prepolymer in fewer than two hours. The necessary fillers, plasticizers, thixotropes and adhesion promoters were then added and mixed under deep vacuum. Samples of the sealant tested well, and a production routine was established. The current total cycle time is under four hours, half of which is allocated to polymer preparation and the other half to mixing. One shift is capable of producing 900 gal of sealant.
To confirm whether a multi-shaft mixer suits your application, it would be worth taking a close look at the following key design elements.
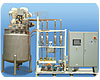
A 600-gal Ross Multi-Shaft VersaMix/Reactor used for the production of polyurethane thermoset resins. This reactor is equipped with PLC-based automated controls and recipe system.
Mixer Configuration
Since multi-shaft mixers can comprise two or more independently driven agitators, one of the first things to determine is the configuration that will serve your process the best. Below are some common combinations and sample applications.Dual-Shaft Mixer Equipped with Two-Wing Anchor and Saw-Tooth Disperser
Dual-shaft mixers are typically used for straightforward dispersion requirements. It is the most economical multi-shaft mixer configuration. The saw-tooth disperser blade enables fast powder wet-out and dispersion, while the two-wing anchor supplies a steady exchange of materials from different parts of the vessel, essentially “feeding” the high-speed blade. Sample applications include glue stick hot melts, pressure-sensitive adhesives, RTV silicon compounds and woodworking adhesives.
Dual-Shaft Mixer Equipped with Three-Wing Anchor and Saw-Tooth Disperser
This configuration is typically more customizable. For instance, provisions can be made for the future addition of a third agitator. The three-wing anchor is also better able to accommodate helical flights than a two-wing anchor.
Dual- or Triple-Shaft Mixer Equipped with Three-Wing Anchor and Multiple Saw-Tooth Disperser Blades
In this configuration, the disperser shaft is equipped with two blades: the bottom blade is fixed at the lowest point of the shaft, and the other blade (of equal or smaller diameter) is usually adjustable along the length of the shaft. This supplementary upper blade helps create a more powerful vortex to quickly draw large amounts of solid ingredients into the liquid phase. It is typically positioned one blade diameter below the liquid surface.
For a more demanding process, a second disperser shaft may be added; thus, the mixer can use a total of four disperser blades. Typical applications include highly filled formulations such as soy-based adhesives, cement pastes, urethane sealants and other caulking compounds.
Triple-Shaft Mixer Equipped with Three-Wing Anchor, Saw-Tooth Disperser and Rotor/Stator
This configuration is popular in the processing of adhesive and sealant formulations when droplet size or particle size distribution is critical. Using a high-speed, saw-tooth blade to incorporate powders into liquid results in acceptable levels of dispersion, but applying a more shear-intensive device such as a rotor/stator mixer typically promotes a finer and more uniform particle size distribution (see Figure 2). The same holds true for formulations involving two or more immiscible liquids; a high-shear rotor/stator achieves a more stable emulsion due to the formation of smaller droplets.
Sample applications include polybutene/water emulsions and pigmented epoxies, as well as rubber cements in which the rotor/stator mixer quickly reduces the size of rubber particles (which in turn accelerates the dissolution process).
Dual-Shaft Mixer Equipped with Three-Wing Anchor and Rotor/Stator
Emulsion adhesives, polyvinyl alcohol solutions and other intermediates with low solids content are commonly batched using this dual-shaft mixer configuration. A candidate formulation may be one that could be processed using a stand-alone rotor/stator but would benefit from improved temperature control or processing under vacuum. The impact could be as dramatic as cutting processing time in half, especially if a cooling cycle is involved.
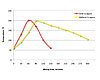
Figure 1. Comparison of Heating and Cooking Times
Seal Arrangements
Unlike mixers with bottom-entering agitators, multi-shaft mixers have no bearings or agitator shaft seals submerged in the product zone, which inherently protects against contamination. A variety of shaft seal designs are available, from cost-effective lip seals to cartridge-type mechanical seals. Lip seals are simple, durable and sufficient for many moderate-duty industrial mixing applications. Mechanical seals utilize specially designed precision sealing faces that run against each other to maintain a seal. They typically provide a longer service life than lip seals and do not wear against the surface of the agitator shaft itself.The agitator shafts of vacuum-capable mixers are often sealed at the cover with single mechanical seals. These seals and the shaft bearings are to be lubricated with a low-viscosity, low-density lubricating fluid. When processing solvent-based adhesives and sealants, it is important to check that the lubricant and elastomers on the seals are compatible with all the solvents present in the formulations. High-temperature applications such as those requiring prolonged heating of the mixer to 300°F or higher benefit from double mechanical seals, which offer better temperature control and lubrication than single mechanical seals.
Sensitive formulations like medical-grade adhesives require enhanced protection against contamination, which could be caused by leakage of the seal lubricant. Dry-running, gas-purged double mechanical seals may be chosen for these applications. Typical barrier fluids used in gas seals include clean air, nitrogen and other inert gases.
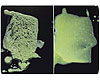
Figure 2. Improved Dispersion and Color Development in a Triple-Shaft Mixer with Three-Wing Anchor, Saw-Tooth Disperser and Rotor/Stator (right), vs. in a Dual-Shaft Mixer with Two-Wing Anchor and Saw-Tooth Disperser (left).
Change-Can vs. Fixed-Tank Design
A change-can design allows semi-continuous operation through the use of multiple interchangeable vessels. The process can be broken down into mixing, discharging, cleaning and preparation. Thus, multiple vessels can be used to extend the production capacity of a single mixer. One vessel would be under the mixer while another would be in the discharge or clean-up stage, and still another would be the loading area being charged with raw materials for the next run.The fixed-tank design is more common on production multi-shaft mixers in the range of 500 gal or larger. The primary disadvantage to a change-can design on a very large mixer is that agitator lift mechanisms of this size add significantly to the mixer cost. Fixed-tank mixers feature hinged covers or large enough access ports to allow for maintenance or cleaning when required.
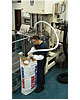
An operator uses a SLIM hose and wand attachment to induct fumed silica from its original sack and into an adhesive product being batched on a multi-shaft mixer.
Discharge Mechanism
After mixing, product can be discharged from a multi-shaft mixer is a variety of ways. The simplest method is to allow the product to flow by gravity through a discharge valve. When scrapers are included, the anchor agitator is typically run at low speeds to assist the flow and wipe product off the sidewalls.A flat-bottomed vessel will naturally retain a layer of material. When a more complete discharge is required, one can opt for a dished or conical bottom vessel. The anchor agitator in this case would be contoured to match the shape of the vessel.
For products that are not very free-flowing, the application of air pressure to the headspace of the mixer may be necessary to help move the material out of the vessel and on to the next production operation. The mixer and vessel must be rated for the level of internal pressure required for this method of discharge.
Another option available on change-can mixers is the platen-style discharge system for efficient transfer of viscous mixtures. With the mix vessel positioned beneath the discharge system, a platen is lowered hydraulically into the vessel. A specially fitted O-ring rides against the vessel wall, literally wiping it clean. Product is forced out through a valve in the bottom of the vessel or through a port on top of the platen. A discharge system eliminates wasted hours of scraping heavy or sticky materials from the vessel.
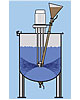
Figure 3. Batch SLIM Mixer with Hopper Attachment
Powder Induction
If the starting viscosity is fairly low, a powder induction system (available on some rotor/stator assemblies) could be of benefit. Specially designed rotors, such as the Ross Solids/Liquid Injection Manifold (SLIM), generate vacuum conditions strong enough to draw powders right into the high-shear zone within the stator. Powders that are difficult to wet out are introduced sublevel, dispersed instantly and do not get a chance to float on top of the batch or form agglomerates (fish eyes).This technique is very operator-friendly and helps to prevent lightweight powders from becoming airborne. Attaching a hose and wand device to the powder inlet of the SLIM allows the operator to simply draw powders straight from within the bulk container. Powders can also be loaded into a hopper and, as soon as the rotor reaches operating speed, the hopper valve is opened to allow the flow of solids into the shear-intense region within the rotor/stator assembly. Powders are quickly drawn into the batch via the powerful vacuum generated by the ported rotor (see Figure 3).
Fumed silica, talc, calcium carbonate, titanium dioxide, carbon black, carboxymethyl cellulose, clay powders, flour, starches, gums, pectin and resins are materials commonly inducted through the SLIM system.
Ease of Cleaning
To improve mixer cleanability, consider:- A CIP-ready mixer with rotary spray nozzles
- High polish on the product contact parts (150-grit or higher)
- A “slinger” on the high-speed disperser shaft to combat Weissenberg Effect (the tendency of some viscoelastic fluids to flow in a direction normal to the direction of shear; manifested by behavior such as the climbing of a fluid up a rotating rod)
- Flush-tank discharge valve
Limitations and Evaluation
Mixers operating with multiple agitators are exceptionally versatile, but they still have limitations in their range of viscosity if one considers the entire spectrum of adhesives and sealants that are currently produced in the industry. The mixers’ versatility mainly results from their independently controlled drives. The agitators can be engaged in any combination and at any speed for any interval during the mixing cycle. Although this sounds complex, multi-shaft mixers are actually engineered to be comparatively simple, effective and economical.When the batch material becomes too viscous to flow freely to the agitators, shifting to a different style of mixer is recommended. For example, the anchor in a multi-shaft mixer may start carving a path through a highly viscous batch as agitation close to the axis of rotation becomes increasingly limited. In these situations, the logical design alternative is a system consisting of agitators that move through all the points in the batch. This is the forte of double planetary mixers and kneaders, which are both also widely used in the industry.
Adhesives and sealants are characterized by properties that are largely process-dependent, and the mixing operation is at the heart of processing. Products with identical formulations that have been batched in different mixing systems can very easily result in dissimilar yield, quality and physical attributes.
Process engineers are encouraged to exercise ample diligence in evaluating mixing solutions that best achieve their specific process objectives. A trusted manufacturer that offers long-term experience, rental and testing resources will make for a very strategic partner whether you are selecting a mixer for a new product, scaling up, correcting a mixing problem or optimizing an existing process.
For more information, contact the author at Charles Ross & Son Company, P.O. Box 12308, Hauppauge, NY 11788 or phone (631) 234-0500.