Cold-bonding aerobic structural adhesives, those that cure “on demand” without heat, allow manufacturers to assemble parts when they want to without being limited by two-component mixing, additional heating and cool down times or oxygen presence within the bond area. Cold-bonding aerobic adhesives provide companies with the ability to bond dissimilar substrates within the production line without having to worry about long fixture times. Because the adhesives experience rapid bond strength development, the parts can continue through the production line without increasing work in process (WIP) times. This means companies who switch to cold-bonding adhesives will improve production efficiencies within their process while experiencing decreased energy costs. All of these are extremely important to companies in today’s current economic conditions. Companies need to explore different methods to become more efficient without sacrificing quality. Cold-bonding aerobic adhesives are one method to help companies.
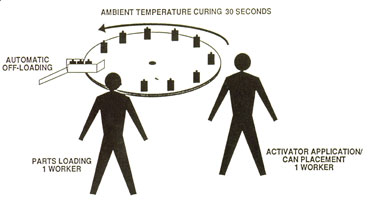
It reminds me of a story of a company who was using an induction heat-curing epoxy to bond magnets into a cold-rolled-steel motor housing. Not only were they experiencing a number of in-line quality issues, but the cool down time to handle the parts added significant WIP and expense to their process. By switching to an aerobic structural adhesive they were able to improve their quality and eliminate any non-valued added steps in their process. This allowed the company to produce a quality assembly quickly while improving their profits.
These adhesives cannot, however, be used in all applications and are only recommended when alternative bonding methods such as ultraviolet light-curing adhesives cannot be used. Aerobic adhesives have been successfully used in DC and brushless DC motor, speaker hardware, and opaque metal and glass bonding applications, in some cases exceeding the strength of one of the substrates.
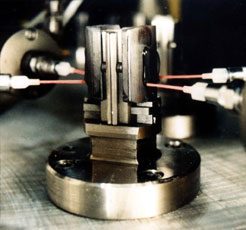
How Do They Cure?
Aerobic structural adhesives are two-component but in a non-traditional manner. Cold bonding technology incorporates a liquid activator and (usually) a gelled adhesive. As shown in the picture to the left, adhesive is applied to parts of a motor, in this case the magnets. Unlike a two-part epoxy where the components are statically mixed together, the activator for the aerobic adhesive is applied to the opposite part, in this case to the motor housing. Once the parts are ready to assemble, the magnets are pressed into the motor housing. The adhesive spreads through the activator, filling any gaps that exist between mating parts. As the adhesive spreads through the bond area and activator, this mixing action starts the curing within seconds and eventually finishes it. Again, there is no need to batch or rack curing parts since the buildup of strength is immediate and ongoing, allowing manufacturers to keep the assembly within the production flow.
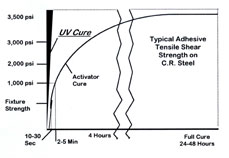
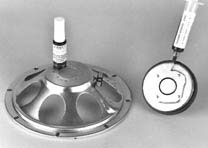
Aerobic adhesives do not work in all applications, but should be selected as an alternative to cyanoacrylates, second-generation acrylics, induction heat-curing and two-part epoxies, and anaerobic adhesives. Each application should be reviewed with the technical staff of the manufacturers' products that you are considering using. Changing to a new adhesive should only be considered after you have thoroughly tested the performance of the assembly to see if it meets your established test criteria.