Historically, the breadth and depth of a person’s shopping experience was defined by a combination of easily found brick-and-mortar storefronts, along with catalogs that would show up in the mailbox. That changed dramatically 20 to 30 years ago when computers started becoming standard appliances in most homes and businesses. Soon after, web-enabled smartphones found their way into nearly every pocket. These revolutionary innovations turned the entire globe into a local department store, supermarket, or pharmacy. Requiring only a reliable Internet connection, consumers now have access to any company’s products and services at the touch of a few buttons.
The increased ability to shop from a desktop or phone was eventually given a name: electronic commerce or, as it is more commonly known now, eCommerce. If eCommerce had become popular before, the COVID-19 global pandemic kicked it into overdrive in 2020. With many brick-and-mortar businesses locked down and the people who frequent them confined to their residences via stay-at-home orders, eCommerce shopping surged, to the point that rare is the day now that an online-ordered package does not arrive at someone’s front door.
What all of these deliveries have in common — whether they contain thumbtacks or diamond earrings, French wine or pharmaceuticals — is that the items arrive in some type of packaging, most commonly a corrugated cardboard box. In fact, corrugated cardboard boxes are recognized today as the world’s most widely used packaging material.
This status is reflected in the fact that, according to various marketing-research companies, the global corrugated-box market had a value of around $67.5 billion in 2021 with expectations that that value will grow to between $80.8 and $82.8 billion by 2028 (which is a 3.5% compound annual growth rate).
What that also means is that corrugated-box manufacturers will need to increase their production capabilities to keep up with the growing demand. Like all manufacturing processes, the one for corrugated boxes is a precise operation, with specific steps needing to be performed error-free each and every time. Industrial pumps play a starring role in one of these manufacturing stages — the transfer of cornstarch glue that holds the cardboard sheets in a corrugated box together. This white paper will illustrate how air-operated double-diaphragm (AODD) and internal gear pumps can be the best option for use in this critical application.
The Challenge
Ironically, while the demand for corrugated boxes has exploded due to a series of technological advances in product ordering, the roots for the corrugated-box manufacturing process stretch all the way back to the less high-tech era of the 1880s. That’s when a Swedish chemist named Carl F. Dahl developed a method that took the raw wood from harvested tree trunks, such as fast-growing pines, and turned it into wood pulp consisting mainly of cellulose fibers, which are the foundational component in a piece of paper. He called his invention the “kraft” process, with the word “kraft” meaning strength in German, which acknowledges the strength of the paper that is produced through the kraft process.
In the kraft process, raw wood chips are treated with a mixture of hot water, sodium sulfide, and sodium hydroxide in order to break down the cellulose, hemicellulose, and lignin in the wood. This treatment turns the wood chips into soft and pliable wood pulp, which is then ready to be manufactured into paper.
Once the kraft paper is produced, it is sent to the corrugating plant where it will be turned into a finished corrugated cardboard box. In reality, only a few materials and stages of production are needed to complete the manufacturing process. As mentioned, one of the most critical is the application of the glue to the various sheets of cardboard that are used to construct the box.
Most larger corrugating plants feature a facility that is unique to box manufacturing: the “starch kitchen.” It is in the starch kitchen that corrugated-box glue is created in a process that involves the mixing of cornstarch, chemicals, and boiling water, resulting in the formation of a thick, pasty liquid. The benefits of using starch-based adhesives in the construction of corrugated boxes are many: good adhesion to wood-based papers, ready availability, easy to apply, inexpensive, resistant to heat, slow curing, non-toxic, and insoluble when used with fats and oils.
Because a large amount of cornstarch is needed at a corrugating plant, it is typically shipped in the form of a dry powder to the plant via railcar. At the plant, it is stored in silos before being transferred to the mixing vessels where the glue is produced. It is at the conclusion of the cornstarch-glue production process that industrial pumps enter the picture.
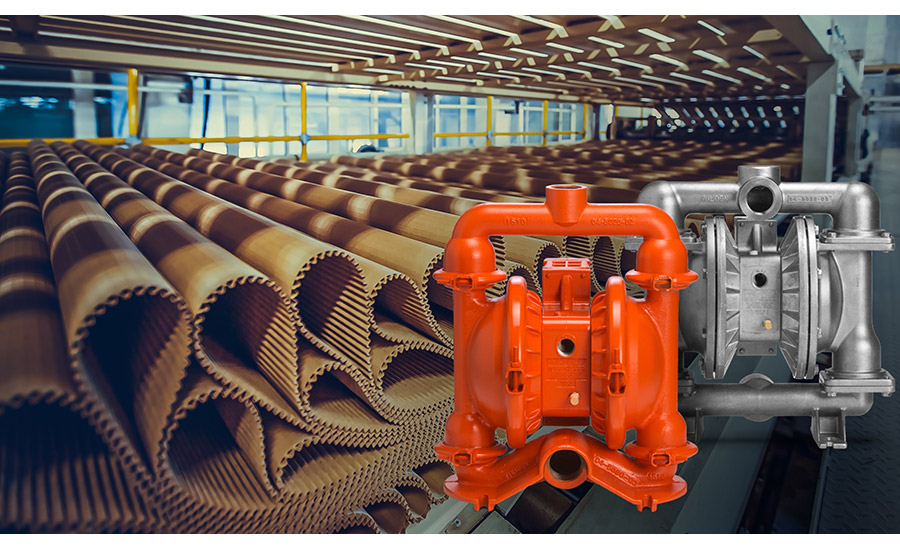
Specifically, pumps are used to transfer the finished glue into the corrugating machine, from which it will be spread over the layers of corrugated medium that will be pressed together to form the completed corrugated cardboard sheet and, eventually, the cardboard shipping or storage box.
The challenge in this process that the pump must overcome is found in the fact that cornstarch glue can be difficult to pump because of its adhesive nature, along with its high viscosity. In addition to being sticky and thick, any liquid cornstarch glue that remains within the pump’s internals when it is not operating will harden. In this case, this hardened glue can cause premature wear that will adversely affect the ability of the pump’s mechanical seals/faces and bushings to operate properly. Even worse, when seals and bushings fail, the pump will be prone to leaks, which not only results in lost product, the cost of which can’t be recouped, but increases safety concerns as well as the need for costly cleanup procedures.
If a pump has failed seals or bushings that can lead to leaks, the choice for the facility operator comes down to whether the seals should simply be replaced or if the pump should be scrapped and exchanged for a new model. Replacing seals can be easy if spare inventory is on hand at the plant, but a pump that has additional performance-dampening damage may need to incur extensive labor and repair costs to get it back to its expected level of performance. In this case, the best option may be to purchase a new pump, though that can lead to longer periods of downtime, which compromises the manufacturer’s ability to meet strict production schedules. In both instances, there may also be a lack of skilled labor readily available to perform repairs or installation, which will lengthen downtime.
Therefore, it is imperative that the corrugating-plant operator identify and deploy a pumping technology that has been designed to confront and overcome the various challenges that are ever-present in the handling of cornstarch glue.
The Solution
As noted above, two of the best of these pumping technologies are AODD and internal gear. Two PSG® product brands offer AODD and internal gear pumps that can be used in cornstarch-glue applications.
Jim Wilden, founder of Wilden pumps, invented the AODD-pumping principle more than 65 years ago. Wilden clamped metal AODD pumps feature Jim Wilden’s original design, which allows them to be easily installed and serviced with only a single tool. The pump features an enhanced flow-path design that can produce flow rates up to 34% higher than competitive models while offering maximum product containment. For both the clamped and bolted models, a ductile-iron wetted path when handling cornstarch glue is recommended, though aluminum and stainless-steel models are also available.
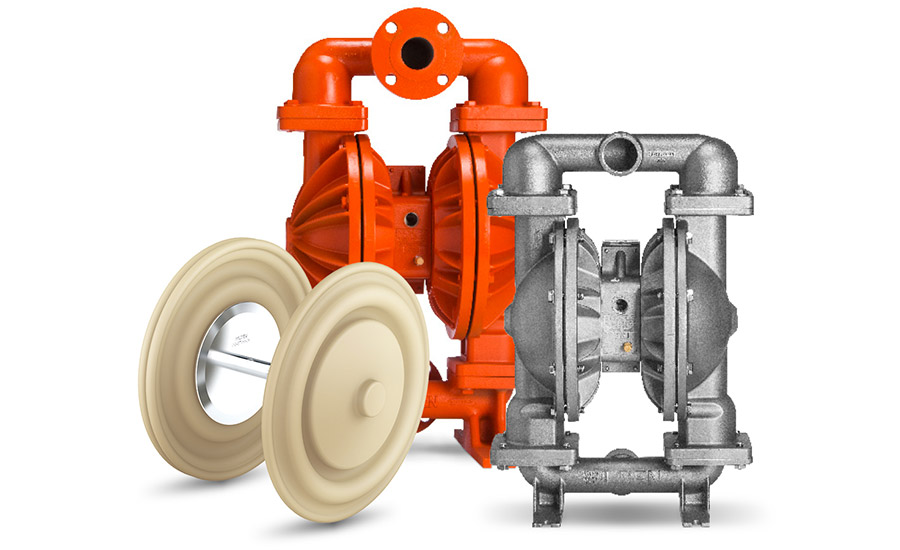
Operationally, all of the Wilden clamped and bolted pumps are portable, self-priming, dry-run capable, and feature no mechanical seals, which reduces the chance that leaks will occur. They are also easy to operate, install, and maintain.
The pumps are also able to be outfitted with an air-distribution system, such as the Pro-Flo® SHIFT Air-Distribution System (ADS). The design features an air-control spool that automatically optimizes and eliminates the overcharging of the air chamber with no reduction in flow rate. This reduction in air consumption helps the pumps achieve up to a 60% reduction in air consumption while simultaneously producing up to 34% greater flow rates compared to other AODD-pump models.
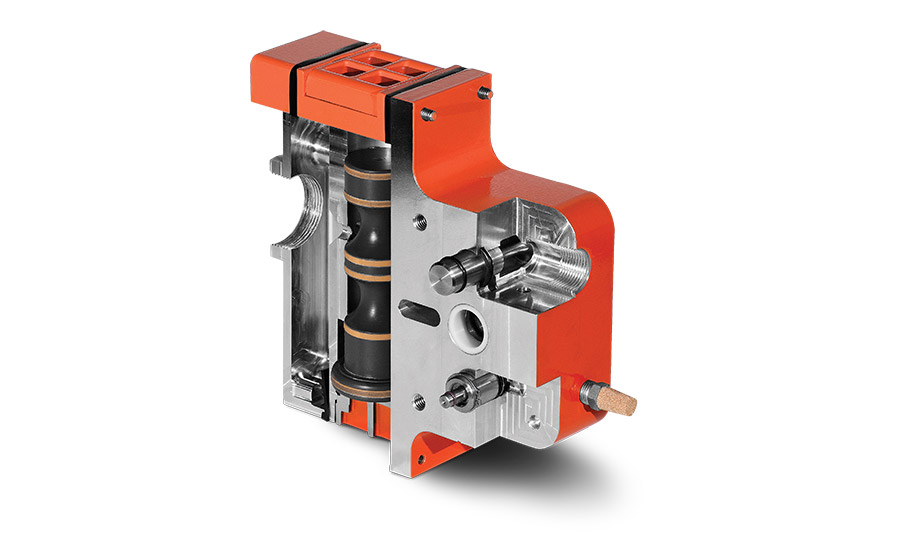
In terms of diaphragms, Wilden suggests its Chem-Fuse Integral Piston Diaphragm (IPD). These diaphragms are capable of delivering 100% increased flow rates and suction-lift capabilities when compared to PTFE-laminate diaphragms. The IPD design eliminates a notorious leak point at the outer piston in traditional diaphragms. This elimination of outer-piston abrasion, and product trap areas, results in longer flex life and increased product containment.
Internal gear pumps are designed to deliver the durability, flexibility, and efficiency needed when handling challenging liquids, such as cornstarch glue. Best designed for cornstarch-glue-handling applications are jacketed cast-iron G Series versions with ANSI flanges, bronze or carbon graphite bushings, with either carbon graphite packing or a Buna-N mechanical seal.
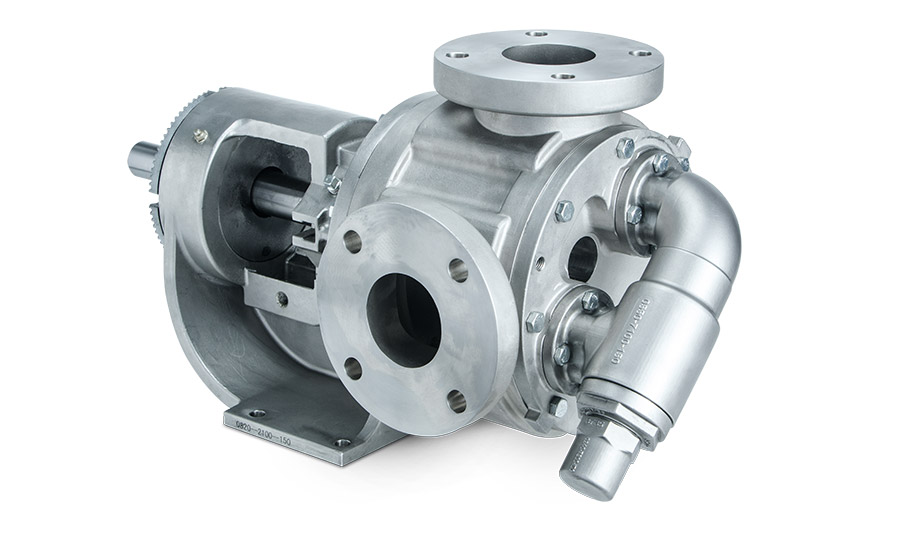
These pumps allow the user to create and maintain turbulence-free laminar flow. A triple-lip seal prevents product leakage in instances when the stuffing box becomes compromised. Direct replacement-part interchangeability with a wide range of competitive pump models gives users added flexibility, and a universally designed seal chamber with an oversized heavy-duty bearing housing can accommodate different sealing technologies. These pumps are standard in many “starch kitchens” because the stuffing-box area on internal gear pumps allows the starch to settle out by displacing the liquid needed to lubricate the seal. The triple-lip seal also provides “dry run” capabilities that help prevent early failure of the seal. Another design alternative is the “behind the rotor” design that positions the seal in fresher product, thus enhancing seal life.
Other optional accessories include an enlarged bearing housing at the rear end of the pump that provides easy drive-end access to the shaft seal and the ability for single-point end-clearance adjustment. Finally, the pump casing also revolves to allow for multiple inlet and outlet positions.
Conclusion
A corrugated box without cornstarch glue is just a pile of cardboard sheets, making the adhesive an indispensable piece of the corrugated-box manufacturing puzzle. However, the glue’s sticky properties, along with its high viscosity, make transferring it a challenge, which requires a specific type of pumping technology. The right type of pump technology for these situations is critical.
Learn more at www.psgdover.com.
Images within the article are courtesy of Wilden.