Over the last several years, many industries have been deeply affected by unprecedented events, and the chemical industry is no different. In particular, the COVID-19 pandemic drastically slowed global material production and decreased the workforce, while Winter Storm Uri disrupted key material manufacturing facilities in Texas in 2021, impacting nearly 78% of the country’s ethylene supply, a critical petrochemical for many materials.1
Today, experts largely agree that the chemical industry is transitioning back to “normal,” having recently enjoyed one of its best years in a decade.2 As recovery continues, it is imperative that manufacturers retain vital lessons learned over the last few years, including the critical need for agility and supplier diversification to weather the storms of unprecedented events and help offset business interruptions. Take, for example, acrylic monomers — critical component(s) of many polymers destined for construction, such as sealants and caulks. Unfortunately, this material experienced volatile swings in pricing and availability in recent years — a scenario made especially devastating for manufacturers who use the monomers across multiple product offerings and lacked viable replacement chemistries or alternatives.
All-acrylic (AA) binders have a reputation for meeting demanding performance requirements, which makes them especially beneficial when used in applications that require excellent exterior durability and ultra-violet resistance, such as ASTM 920 caulks and sealants; or in applications requiring excellent adhesion and strong flexibility, such as ASTM C834 grade binders for caulking and sealing joints in buildings. At the other end of the spectrum, AA binders can also be used in less demanding applications when formulated with increased filler levels. This flexibility allows manufacturers to leverage acrylic monomers as a central building block for many products within their portfolios.
While the flexibility of using a single all-acrylic binder to meet different application needs may sound like an attractive, streamlined solution, it also places your production at risk. The COVID-19 pandemic and Texas Freeze greatly impacted access to acrylic monomers, resulting in significantly higher material prices and low supply. A report from S&P Global showed that the Texas Deep Freeze caused more than 75% of the U.S. ethylene manufacturing capacity to go offline immediately following the storm — concerningly low production levels for a chemical used heavily in acrylic monomers.3 Companies relying heavily on a single material component, such as acrylic monomers, risk losing multiple product offerings, should supply challenges return.
Styrene-Acrylic Binders
The key to remaining agile and creating a resilient product portfolio involves considering new chemistries and materials suppliers. Manufacturers relying heavily on acrylic monomers may want to consider adding styrene binders to their portfolios, which have remained more stable in terms of accessibility throughout the events of the last few years. Compared to the acrylic monomer, a styrene monomer is typically available at a lower price point and can be combined with acrylic monomers when synthesizing a binder. Styrene-acrylic (SA) binders have performance properties similar to an AA latex binder and are a strong alternative for sealant applications.
Styrene-acrylic binders are a proven, reliable chemistry for sealant applications and boast impressive performance properties. SA latex binders offer excellent peel adhesion to common substrates such as concrete and anodized aluminum. Certain SA binders can even outperform an all-acrylic (AA) binder. For example, LIGOS C 9504 is a SA binder designed for various sealant applications. When testing the peel adhesion of a cured-in-place elastomeric joint sealant using the ASTM C794-18 method, the SA binder outperforms the ASTM C 920 Class 25 and Class 12.5 AA control binders in both wet and dry peel strength.4
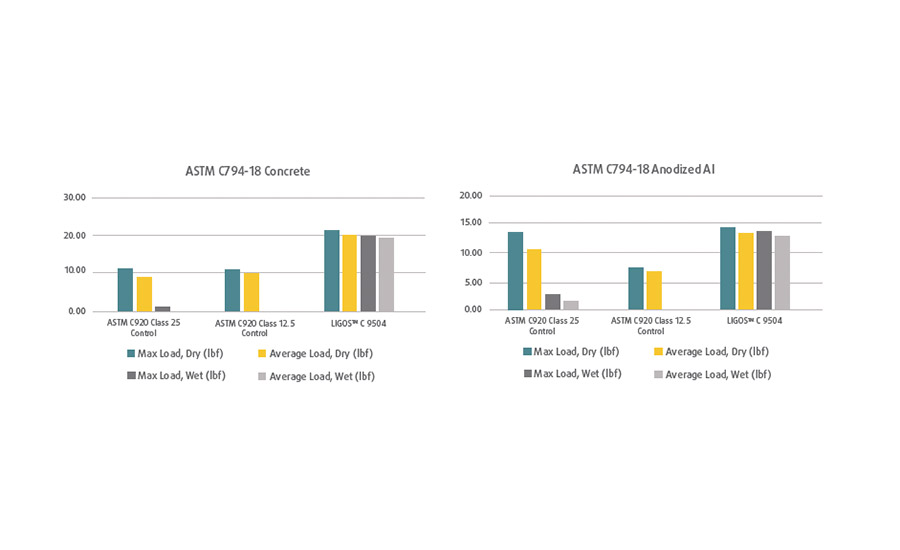
SA latex binders also boast strong flexibility and elasticity. These critical performance properties allow a sealant application to move, expand, and contract at varying temperatures without rupturing the seal. In addition, improved elasticity can reduce maintenance costs as it reduces the need to repair the application.
Styrene acrylic latexes are competitive with acrylic latexes in performance. By incorporating styrene with acrylic monomer, the resulting SA latex can yield a cost-effective solution. These chemistries can play a vital role in a company's product portfolio, as they meet the requirements for a robust sealant application. Diversifying material formulations and suppliers can also assist companies in maintaining product supply, even during an industry-altering event. By shoring up chemistries, companies can do their best to continue manufacturing, reduce financial loss, and develop a strong reputation as a reliable manufacturer.
The Right Partner
It is easy enough to set the intention for diversifying your materials portfolio, but executing this is challenging without the right materials partner. The right partner should collaborate and share their expertise to help you meet your goals. Whether companies are working to alter their existing binders or introduce new solutions, a valuable partner can assist in product development and testing. The right partner can also anticipate trends in the chemical industry and help you adapt to them.
Remaining complacent can place a company's production at risk in the event of another disaster. By prioritizing a more diverse portfolio, such as one that incorporates both styrene acrylic- and acrylic-based latexes, companies can ensure they can adjust their production as needed. Additionally, choosing a solutions partner with the expertise to help companies alter their formulations ensures their products continue to meet performance requirements in an ever-evolving industry. By addressing these concerns now, companies can create a robust portfolio to become agile for uncertainty in the future.
Learn more about Trinseo at www.trinseo.com.
References
- S&P Global. (n.d.). Impact of Winter Storm Uri on Chemical Markets. S&P Global. https://www.spglobal.com/commodityinsights/en/ci/topic/impact-of-winter-storm-uri-on-chemical-markets.html
- American Chemical Council. (2022, December 7). Industry Outlook: Competitive Edge and Sensible Regulations Key to Weathering Recession for U.S. Chemical Producers. Chemistry in America. Retrieved May 15, 2023, from https://www.americanchemistry.com/chemistry-in-america/news-trends/press-release/2022/industry-outlook-competitive-edge-and-sensible-regulations-key-to-weathering-recession-for-us-chemical-producers.
- Hays, K. (2021, March 1). Factbox: Texas petrochemical restarts continue slowly after freeze. S&P Global Commodity Insights. https://www.spglobal.com/commodityinsights/en/market-insights/latest-news/petrochemicals/030121-factbox-texas-petrochemical-restarts-continue-slowly-after-freeze
- Trinseo LIGOS™ C 9504 Fast Fact Sheet. Data on file.