When using solventless laminating adhesives in flexible packaging applications, factors including adhesive selection, coat weight, laminator temperature, and tension settings should be considered to avoid visual appearance issues.
Solventless Laminating Adhesives
Laminating adhesives play an integral role in constructing multilayer flexible packaging by bonding layers of plastic film, foil, and other materials to combine barrier, ink receptivity, structural toughness, and other functional properties needed for the package. The earliest laminating adhesives made consisted of a solvent-based carrier, a two-component resin system, and additives. While solvent-based laminating adhesives are still widely used today, many converters are starting to invest in lamination equipment capable of running solventless laminating adhesives. These adhesives consist of an isocyanate-functional prepolymer and polyol system in the absence of a carrier that cures via an addition reaction to yield a polyurethane adhesive. Since solventless laminating adhesives do not require a carrier, converters that run solventless adhesives increase the sustainability of their operations, as they do not need to invest in driers that consume high energy and require less VOCs and HAPs emission and exposure control.
Troubleshooting Appearance
When handling solventless laminating adhesives, there is always a possibility of obtaining a laminate that fails quality control tests for performance or visual appearance. Sometimes, the underlying issues that contribute to poor performance may also be responsible for impacting visual appearance and vice versa.
Many variables, such as adhesive choices, target coat weights, temperature settings, primary and secondary treat levels, rewind pressures, and taper tension, can significantly impact the visual quality of the laminate. To assist in troubleshooting, the following sections examine common visual issues that solventless laminations encounter.
Voids, outgassing, and bubbles in laminate
Over the years, production line speeds have increased as advances in lamination equipment and adhesive technologies have increased production efficiency. With this efficiency increase, there is a higher chance that laminates result in a mottled appearance that can be classified as having voids, outgassing, or bubbles, as seen in Figure 1 and Figure 2 below.
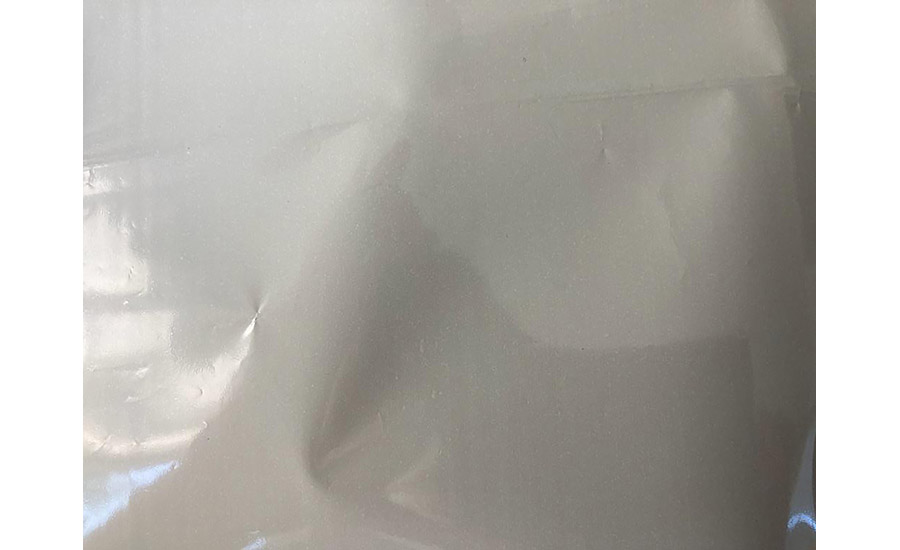
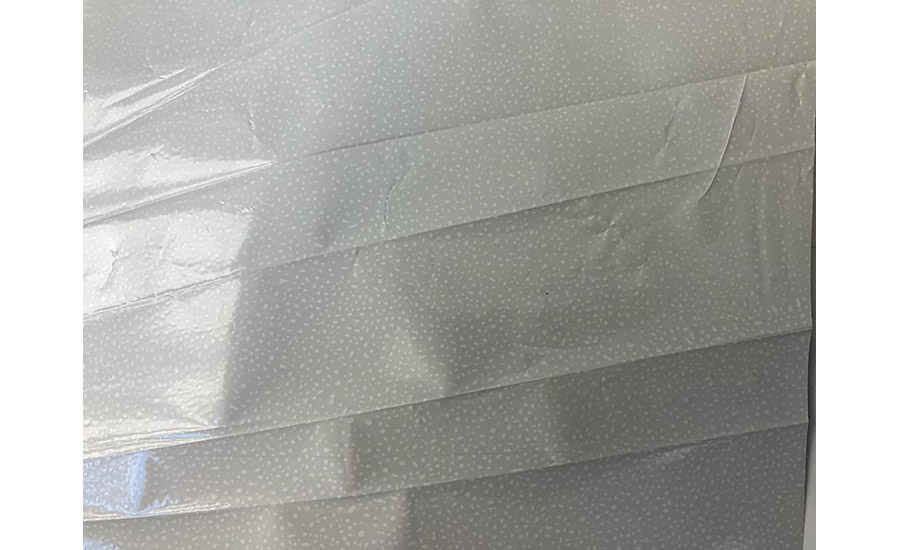
These are typically caused by reduced flow and leveling of the adhesive onto the substrate. Most often, the root cause of this is an imbalance of the wet surface tension of the adhesive and the dry surface energy of the substrate, leading to reduced wet out. Faster line speeds exacerbate this issue since an adhesive has less time to level appropriately on substrates. Typical films used in food packaging laminates have dry surface energies of approximately 39–40 dynes/cm, whereas solventless laminating adhesives typically have 40 dynes/cm of surface tension. Therefore, film pretreatment is often required to increase surface energy to a level above adhesive surface tension to ensure good adhesive wet out. While less common, other causes for these types of appearance issues may include using a nip pressure that is too low, using a nip roller that is too soft, or excessively agitating adhesives during mixing and circulation.
Tunneling
Tunneling creates an undesirable appearance and can result from several factors. Typically, manufacturers of solventless laminating adhesives will provide a suggested mix ratio for the isocyanate prepolymer and polyol. If an incorrect mix ratio is used or if residual ink solvent featuring a hydroxyl group is present, the adhesive may not cure properly and will result in tunneling. In addition, laminator run settings must be optimized. Tunneling can result if there is improper tension of the web being coated with the adhesive or during rewinding. In solventless systems, using an excessive coat weight may also contribute to tunneling. Both examples of tunneling are seen in Figure 3 and Figure 4 below.
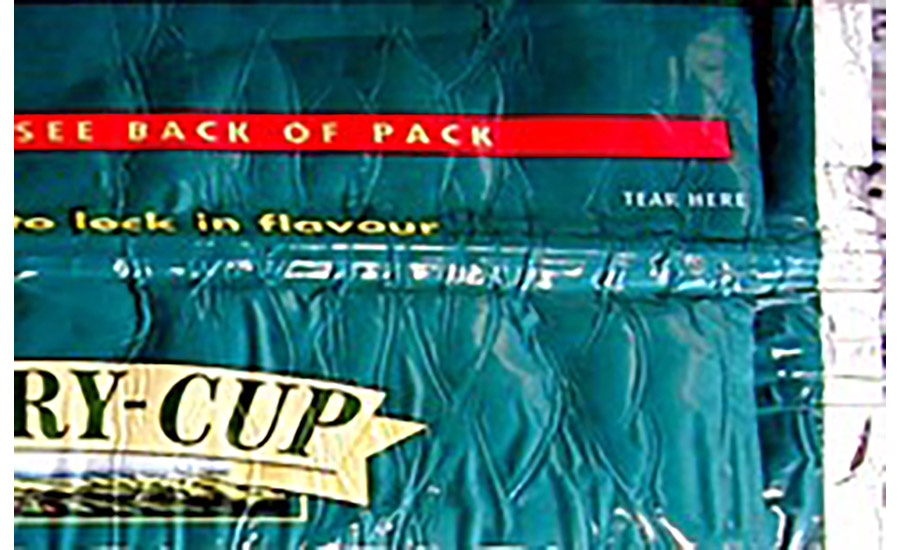
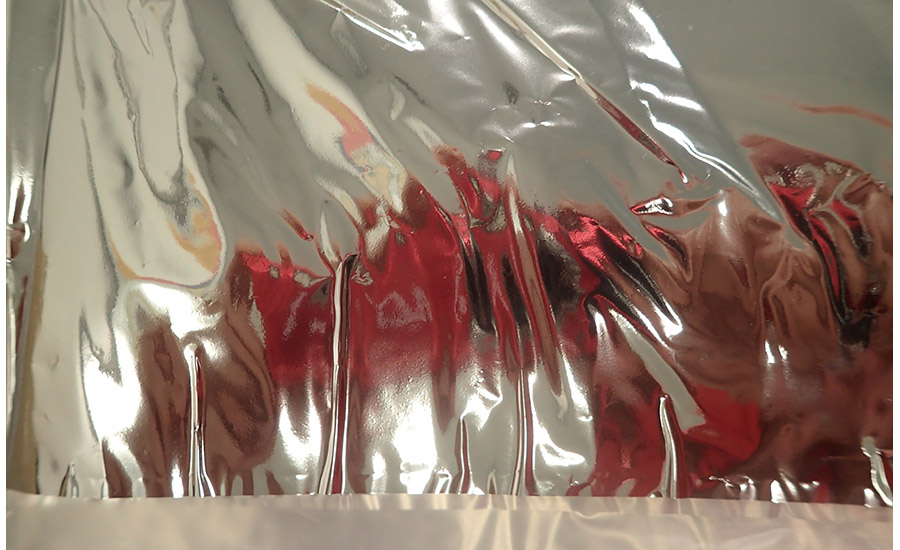
Haze
Certain laminates used in packaging are optically clear and provide barrier properties to oxygen and moisture while maximizing transparency to display contained products. In these cases, haze is an issue that should be avoided. As shown in Figure 5 and Figure 6 below, haze may result from air entrapment in the laminate, which may be caused by excessive agitation of the mixed adhesive prior to mixing or during circulation. Using an adhesive that has gone too far into its pot life may also cause bubble entrapment and haze.
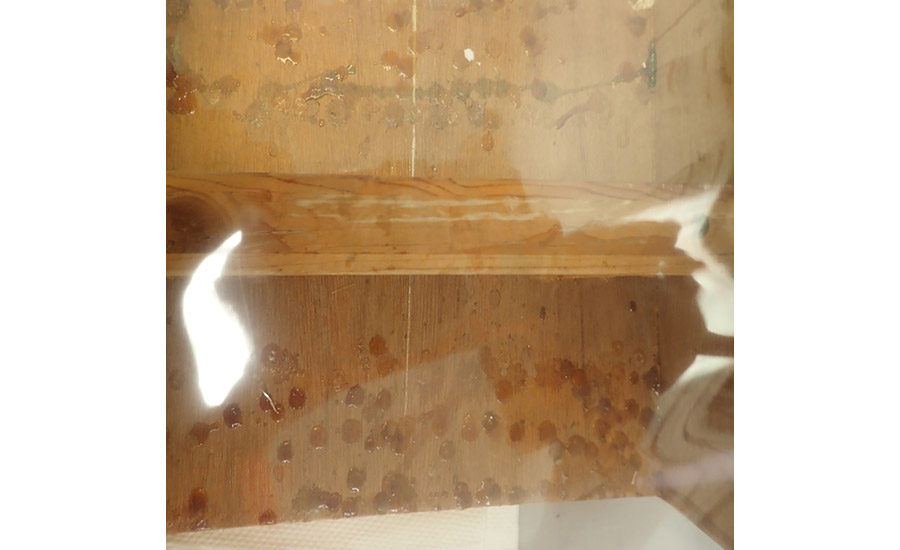
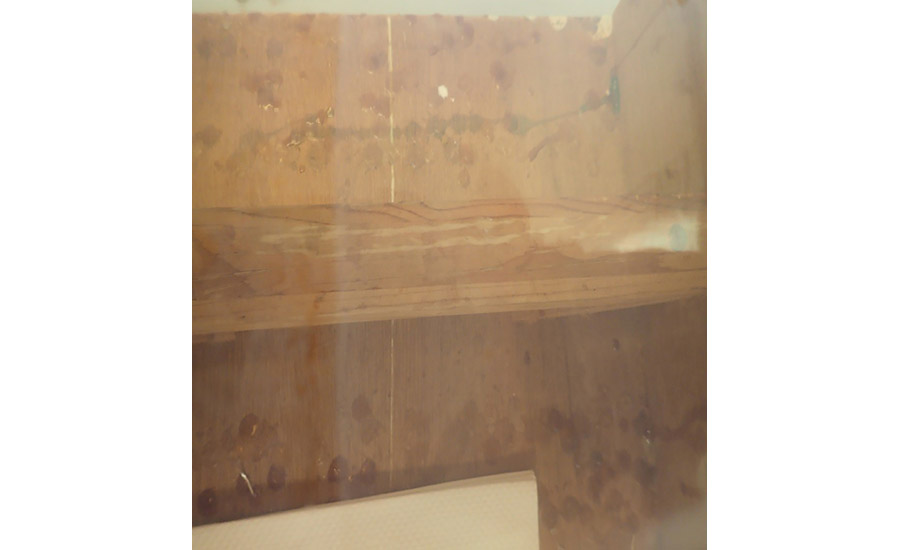
Ink bleed or smear
High-definition print on flexible packaging is critical for manufacturers since it is required to accurately convey branding and other required information about the product. A common issue that distorts print quality stems from an incompatibility with the ink system used for printing, where the adhesive bleeds or smears the ink, as shown in Figure 7. In particular, solventless laminating adhesives are susceptible to incompatibility with the inks used in flexible packaging because their polymers are relatively low in molecular weight and have a high propensity to solvate inks. Additionally, solventless adhesives do not contain solvents and are not dried using conventional driers like solvent-based and water-based adhesives, so they remain in liquid form during the curing process, further contributing to potential ink solvation. For these reasons, it is critical to perform small-scale trials and determine ink compatibility prior to running at full scale.
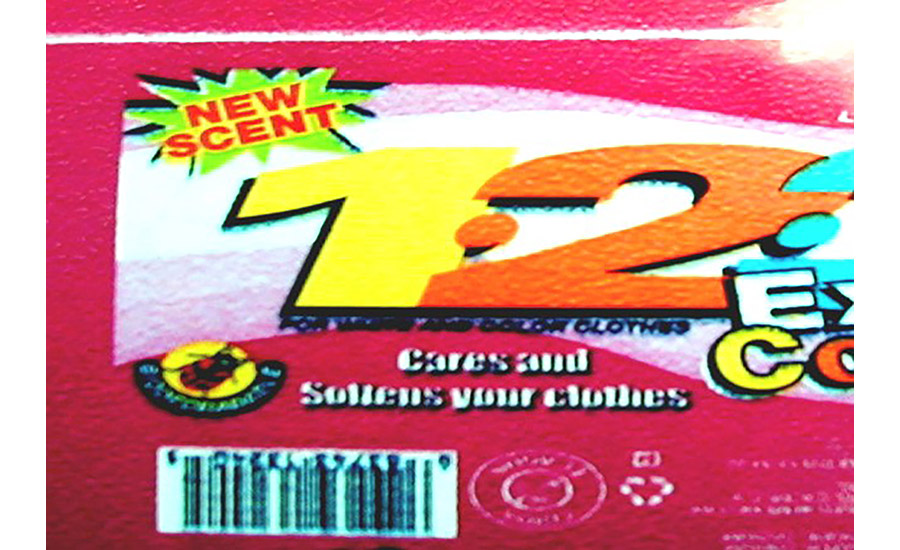
Adhesive Choice and Guidelines
As detailed so far, many settings play a role in influencing visual appearance. Often, one or more adjustments to these settings will need to be adopted, and in some cases, what works for one film or adhesive may not work for another. One way to minimize the number of variables in the troubleshooting process is to work with solventless adhesives that have been studied, developed, and used extensively, such that starting point recommendations and guidelines may be followed to maximize success.
The Dow Chemical Company has focused on improving appearance issues by studying existing solventless adhesive chemistries and using this to manufacture new solventless adhesives that perform and display consistently under a set number of conditions. Recently, Dow launched PACACEL™, a brand of high–run speed solventless adhesives that have shown a marked improvement in appearance at run speeds above 1,200 feet/min on a variety of films, foils, and other laminate substrates. These adhesives feature full cure to FDA compliance in as little as two days, have demonstrated compatibility with various ink systems, and provide excellent bond strength in film, metallized film, and foil structures.
Below are common run settings that are recommended for PACACEL adhesives to ensure the best appearance.
- Adhesive puddle temperature in pan: 105 °F (41 °C)
- Application roll temperature range: 122 °F to 140 °F (50 °C to 60 °C)
- Nip temperature: 120 °F to 130 °F (49 °C to 55 °C)
- Coat weight: 1 pound per ream (1.6 g/m2)
While the coat weight above has established the best visual appearance for many applications, coat weight should be evaluated and adjusted for each new application to determine the optimal balance of visual appearance and performance.
Treat levels should also be closely examined and tested. As mentioned previously, most solventless adhesives show optimum wetting when the substrates have surface energies above 40 dyne/cm. Even if films are newly manufactured, it is often advisable to bump treat at 1-watt density to clean films of surface contamination. Treatment should be verified with fresh dyne solutions; if surface energy is still below 40 dyne/cm, the watt density on the treater should be raised above 40 dyne/cm.
Adjustments on the rewind portion of the laminator have also been shown to improve flow, leveling, and appearance. When laminates are wound tightly and kept warm, the appearance of the laminate typically improves. A rewind tension between 30 and 40 psi, a lay-on-roll pressure at 30–40 psi, and a taper tension at or below 25% are optimal for many machines and solventless laminates.
It is critical to work with both the manufacturer of the solventless adhesive and the laminator to discover the optimum settings for each film structure. Once an effective group of settings has been established for a structure, it can be implemented for production.
Conclusion
While solventless laminating adhesives offer several cost, performance, and sustainability benefits, they sometimes run into issues displaying a good visual appearance in flexible packaging. There are several recommended settings to ensure optimal laminate appearance. Proper adhesive selection, coat weight, laminator temperature and tension settings, and other factors play a large role. Many of these guidelines are offered by solventless adhesive manufacturers who have studied their adhesives extensively to ensure the best visual quality for any application.
ChemPoint is the exclusive distributor of Dow Solventless Laminating Adhesives. For more information, visit www.chempoint.com.
- The wrinkled appearance of this laminate is not a result of voids, outgassing, and bubbles.
- Ink bleed is evident on the black colored print in this image.