Adhesives are currently becoming increasingly important in a wide variety of applications in the medical, industrial, and health care industries. Two-component adhesives are being used more and more because of their special properties, and static mixers are the most frequent choice of device for mixing the two-component material before application.
The advantage of using static mixers is they mix two-component materials consistently regardless of who is operating them. This means reproducible mixing outcomes and high reliability since they contain no moving parts. The first key factor when it comes to achieving a high level of efficiency is the mixer design and mixing method. However, the interaction between the mixer itself and the rheological properties of the material, the specified mixing ratio, and the viscosity ratio of the individual components must also be taken into account.
Relevant Parameters
A wide variety of demands are placed on static mixers by virtue of the wide variety of applications and industries they can be used in. A large-scale project was therefore undertaken to investigate the specific properties of static mixers with the aim to achieve a higher level of efficiency for the individual applications. Dimensionless characteristics were defined in order to obtain a quantitative description of these properties. This makes it possible to evaluate mixing efficiency without reference to the material properties of the components to be mixed or the operating conditions. The characteristics are also intended to describe the properties of the mixer itself rather than the application system as a whole. Thus, the characteristics have been categorized into mixer-specific and system-specific characteristics.
System-specific characteristics are used to describe the dispensing system as a whole; namely the cartridge, dispenser, and mixer in mobile systems, or the container, dosing system, and mixer in stationary systems. However, these characteristics do not describe the specific properties of the various mixer geometries.
By contrast, mixer-specific characteristics can be used to describe mixing efficiency. The mixing efficiency is characterized by pressure drop, shear rate, mixing quality, waste volume, and residence time behavior. This article focuses on the different mixing principles in laminar mixing and the typical mixer geometries derived from them.
Mixing Principles
Laminar flow is almost always present in 2K materials for industrial and dental applications due to the high viscosity of the component. As illustrated in Figure 1, laminar flow means an absence of turbulent eddies, which also enables mixing perpendicular to the main flow direction.
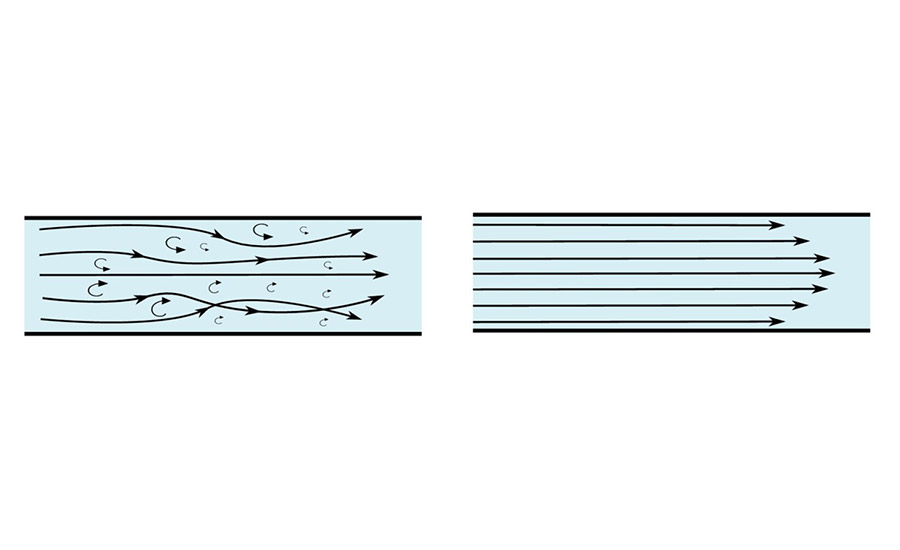
Therefore, in laminar flow mixing happens by convective and dispersive mixing only. Dispersive mixing means the repeating parting of the fluid by the mixer geometry. Convective mixing describes the elongation and folding of the fluid by convective shear forces. A smart mixer geometry combines both processes in an optimal way to generate ever thinner layers of the components and to increase the interfacial area between them. Hardening reactions start where the two components come into contact with each other and depend on the concentration gradients and the size of the interfacial area.
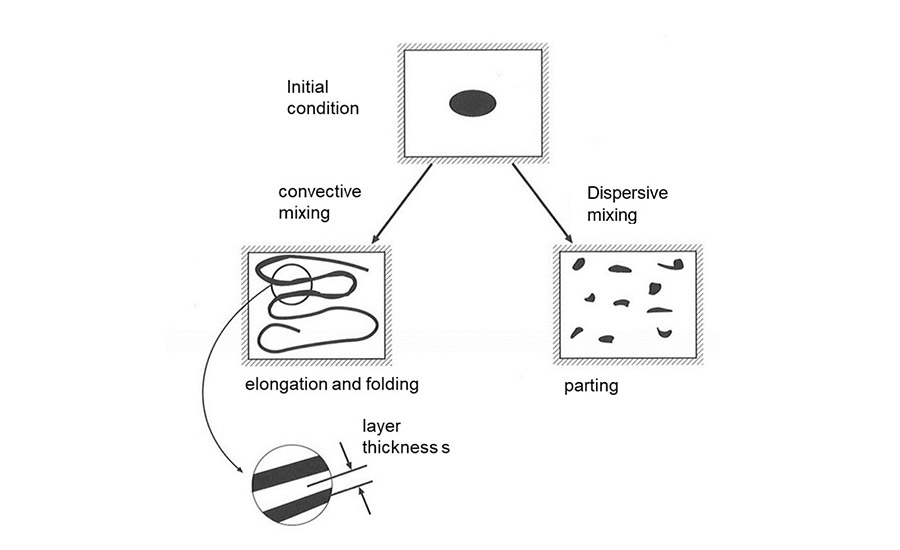
Therefore, both processes (laminar mixing and chemical reaction) must be examined together, as an improved mixing quality caused by dispersive and convective mixing affects the chemical reaction of the hardening process. A better mixing quality yields a faster reaction and better properties of the hardened material.
As a leading supplier of mixing and application solutions for the industrial and dental market, Mixpac® offers a wide range of different mixer types in various sizes.
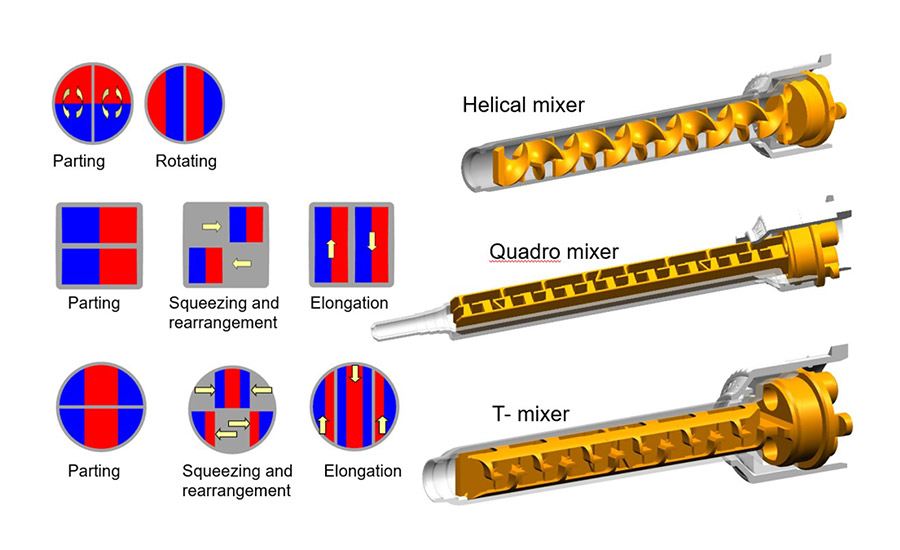
These mixer types and their mixing principles are shown in figure 3. In the case of the three mixer types shown, the number of theoretical material layers doubles respectively; the layer thickness is halved with each mixing element.
Based on the material properties (especially viscosity and viscosity ratio), the mixing ratio, and the operating conditions (flow rate, dispensing device), the customer can choose the optimal mixer for their application.
The next article in this series will explore the influence of rheology on mixing behavior in static mixers.
Additional information is available at www.medmix.swiss.
References:
1. www.cfdsupport.com