Depending on the material to mix and the pre-defined application, different mixer characteristics are of particular importance. This article focuses on characteristics that describe the properties of the mixer itself (mixer-specific characteristics) rather than the application system as a whole (system-specific characteristics).
The mixing efficiency of a mixer can be characterized by the pressure drop over the mixer length, by the shear rate to which the material is exposed to in the mixer, by the mixing quality, by the volume of material remaining in the mixer and by its residence time behavior (see Table 1). In order to obtain a quantitative and comparable description of these properties, dimensionless characteristics were defined. This makes it possible to evaluate the mixing efficiency independently of the material properties of the components to be mixed and the operating conditions.
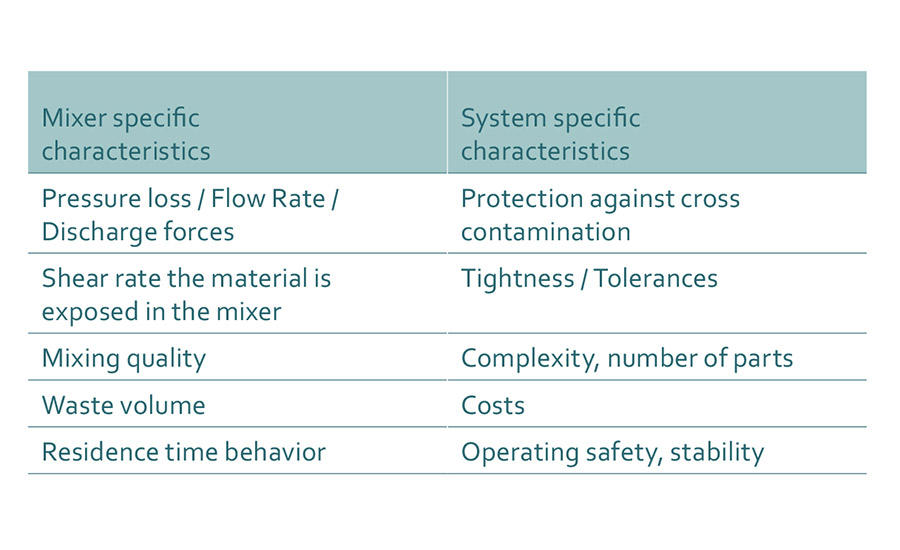
Parameters to Assess the Efficiency of a Mixer
Mixing quality
Due to the high viscosity of the two components, 2C materials for industrial and dental applications almost always have a laminar flow. As a result, mixing does not occur by turbulence, but can only be achieved by repeatedly separating, shearing, and recombining the components to be mixed. The mixing quality is often expressed in terms of the CoV (Coefficient of Variation), which is a purely stochastic variable and is defined as the standard deviation of the concentration distribution divided by its mean value. Therefore, the lower the CoV value, the better the quality of the mixture. In the case of laminar flow, the CoV that can be achieved by a given mixer depends only on the rheology of the material being mixed, the type of mixer, and the number of mixing elements, but is independent of the operating conditions.
Pressure loss
The pressure loss in the mixer — or from the user’s point of view, the force required to discharge the material — is a key characteristic since this force must be applied by a user or a discharge device. If the discharge force is already specified (for example by a pump or an electrical dispenser), the maximum achievable volume flow rate is limited by the pressure loss in the mixer. The pressure loss ∆p per mixing element can be written as:

KL is the dimensionless characteristics to describe the pressure loss per unit of mixer length.
Waste volume
The waste volume is the material remaining in the mixer that must be disposed of after application. Since these materials are often expensive and/or environmentally hazardous, minimizing the waste volume saves money and helps to protect the environment.

Kv is the dimensionless key figure for describing the loss volume of a mixer element.
Shear strain rate
The shear rate is used in rheology as a measure of the mechanical stress acting on a fluid. Knowing the average shear rate S in a mixer is important for several reasons. On the one hand, for shear-thinning materials, high shear rates result in lower pressure losses in the mixer, thus facilitating the mixing process. On the other hand, however, excessive shear can damage sensitive materials and have a negative effect on the curing reactions.

Residence time behavior
Static mixers are generally designed for efficient radial mixing, i.e., to compensate for radial concentration differences. This property can be evaluated using the above-mentioned characteristics for mixing quality. Fluctuations in the mixing ratio can occur in certain applications, in particular when using mobile dispensing systems. The mixer should therefore also have a good axial mixing ability in order to compensate for these problems. This is achieved by mixers that own a broad residence time distribution, meaning that some fluid elements flow rapidly through the mixer while others take longer. One implication of this is that the component that enters the mixer later can still catch up with the other slower moving components, ultimately balancing the mixing ratio at the mixer outlet.
Advantages and Disadvantages of Different Mixer Types
To obtain homogeneous mixing of the two components, high shear forces are generated in a mixer. In general, the better the pressure energy is converted into shear, the more efficiently a mixer mixes. An interesting fact is that all mixers of a given type (regardless of their diameter and the number of mixing elements) can be plotted on one curve. This is true for both Newtonian and non-Newtonian fluids.
In Figure 1, the average shear rate of a particular mixer type is plotted against the pressure drop of that mixer. It is easy to see that Quadro and T mixers are the most efficient at converting the energy from the discharge force into shear. This higher mixing efficiency can also be observed in real applications. For a given pressure drop, Quadro and Helix mixers provide the best mixing quality with the lowest waste volume.
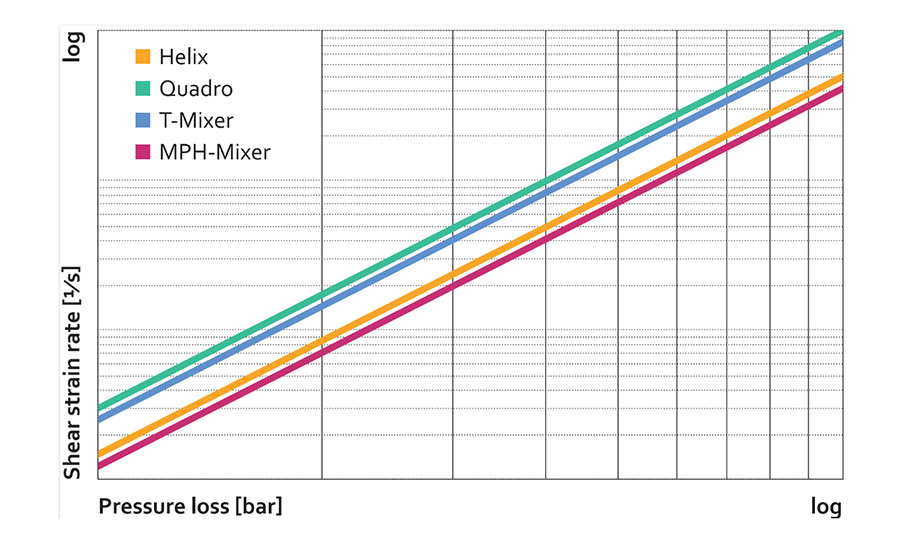
Unfortunately, this relationship only applies to materials that are easy to mix. For 2K-materials with increasingly higher mixing ratio and/or viscosity ratio of the two components, the mixing efficiency of these mixer types decreases and sometimes it is even impossible to obtain a homogeneous mixture with them. Application tests have shown that helix mixers, while not quite as efficient, are suitable for a wider range of applications. X-Grid mixers are particularly recommended for applications with low to medium viscosity, but very high viscosity ratios. For such difficult-to-mix materials, the X-Grid technology offers exceptionally high mixing quality.
A good guidance for what mixer type to choose is provided in the flow chart in Figure 2.
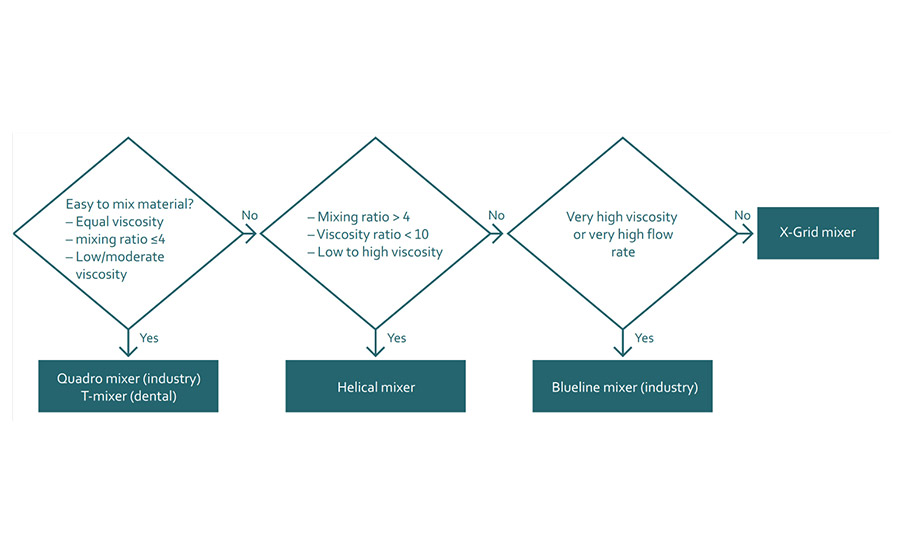
The optimal size (inner diameter) and number of mixing elements mainly depends on the flow rate to be applied and the viscosity of the material. Due o its broad portfolio of different mixer types with a wide variety of mixer sizes and number of mixing elements, medmix can provide an optimal mixer for almost all applications.
Learn more about medmix at https://www.medmix.swiss/.