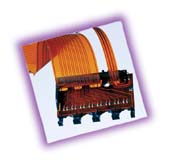
Electrically conductive adhesives play an increasingly prominent role in the design and production of electronic packages and assemblies. Continuing improvements in adhesive technology have enabled adhesives to replace solder in some specialized electronic assembly applications.1-9
Two types of electrically conductive adhesives provide specific benefits where an electrical interconnect is desired. Isotropic conductive materials conduct electricity in all directions equally, and can be used to replace solder on thermally sensitive components. Isotropic materials can be used on devices that require a ground path. Anisotropic conductive materials allow electrical current to flow only along a single axis (typically the Z-axis), and provide electrical connectivity and strain relief for devices such as flip chips. All electrically conductive adhesives have two common qualities: they provide a chemical bond between two surfaces, and they conduct electricity. Figure 1 is a cross-section of a die bonded to a substrate with an isotropic adhesive.
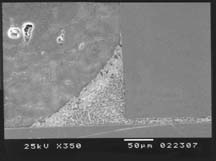
Typical electrically conductive adhesive formulations are made up of an isolating polymer resin that is filled with conductive particles. The resin provides a mechanical bond between two substrates, while the conductive filler particles provide the desired electrical interconnection.
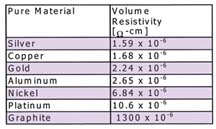
Isotropic Conductive Materials
Electrically conductive isotropic adhesives can be used as an electrical interconnect on non-solderable substrates such as ceramic or plastics, or to replace solder on thermally sensitive components that cannot withstand > 200°C solder processing temperatures. The most popular filler material for highly conductive adhesives is silver due to its moderate cost and superior conductivity (see Table 1).Isotropic silver-filled epoxies can be found as heat- or room-temperature-curing, single- or two-component formulations. Since electrically conductive epoxies require temperatures of only 150°C or less to cure, and room temperature curing is a viable option (typically for two-part formulations), isotropic epoxies are an ideal alternative to solder on thermally sensitive parts.
General-purpose, silver-filled room-temperature or heat-curing epoxies have been formulated specifically for rework and repair applications on large-pitch interconnects. For example, if the trace on a circuit board's surface gets gouged, selected versions of these epoxies may be used to repair the circuit in place of the original solder. These adhesives can also be used as a solder substitute on through-hole components.
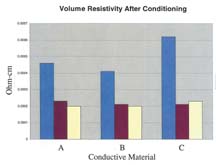
Although silver filled epoxies are the most common isotropic adhesives, newer X-bismaleimide resins (X-BMI) are being employed in more applications. BMI materials have some advantages over epoxies, such as higher temperature stability, lower modulus and rapid cure kinetics.1 As with epoxies, adding various fillers can make BMI materials either electrically or thermally conductive. Certain BMI resin formulations can be cured in seconds at elevated temperatures (e.g., 15 seconds at 200
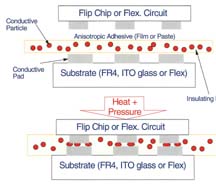
Anisotropic Conductive Materials
Anisotropic adhesives contain a tightly controlled concentration of conductive particles that allow electrical current to travel through the adhesive along only one axis. These materials are frequently used on flip-chip devices to provide electrical connections at planned intervals where particles come into direct contact with conductive substrates.Figure 3 illustrates a cross-section of a fine pitch assembly. If filler loading is increased, the probability of shorts between adjacent pads dramatically increases. If filler level is too low, particles may not be trapped between conductors and open circuits can occur. In most anisotropic materials, the particles are randomly distributed in the matrix material. This can cause problems, particularly for very fine pitch applications, as there will be local variations in particle concentration that can result in an open or short circuit.
Various strategies have tried to address this random particle distribution. A number of conductive fillers have been used to impart conductivity to the polymer system, also called the insulating matrix (e.g., epoxy). The filler is generally spherical in nature and is often mono-disperse. Examples include gold plated polymers, solid gold, silver, nickel, and tin based alloys.
The insulating matrix will either be thermoplastic or thermosetting depending on the final application of the assembly. Although thermoplastic advantages include reworkability and assembly speed, they are not normally chosen as matrices for anisotropic adhesives. Robust thermosetting systems are the more common choice, offering resistance to heat, moisture and mechanical stress. The most common choice for the insulating matrix, epoxy-resin-based adhesives adhere to a variety of substrates, and offer toughness and good corrosion resistance. An epoxy insulating matrix also provides stress relief and adds reliability to the rest of the device.
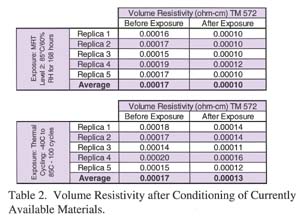
During assembly with anisotropic conductive materials, the chip must be carefully placed in-line with the z-axis. Heat and pressure must be maintained typically for 5-10 seconds until the cure process is completed. This process may prove to be more cost effective and offer higher productivity than the typical C4 process for flip-chip assembly based on total throughput and higher yields. Since flip-chip uses gold plated or stud bump, flux is not used at all during the process, eliminating flux concerns such as cleaning and compatibility. In addition, the process is lead-free and environmentally friendly, as gold replaces tin-lead solder as the bumping material.
For more information on electrically conductive adhesives, contact Henkel Technologies, http://www.henkel.com .