Pulsed UV is a safe and extremely flexible technology that can deliver complete cures of thick formulations quickly. The unique capabilities of pulsed UV technology can solve intractable curing problems. With pulsed UV, we were able to solve a difficult curing problem that allowed an ambitious client to begin manufacturing cutting-edge optical-disc storage products.
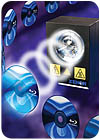
OBSTACLES FOR AN AMBITIOUS CUSTOMER
The optical-disc storage industry is known for its challenging curing requirements. A company that wants to be at the forefront of manufacturers making the third-generation optical-disc-storage format came to us to solve a tough curing problem for the "Blu-ray DiscTM" format.While a DVD can store about 5 GB of information, a Blu-ray Disc will store 50-200 GB, and can be used for computer games and high-definition TV. Manufacturing these discs, however, is markedly more difficult than making DVDs and CDs. The increase in content on each disc results in tightened manufacturing tolerances, while market forces limit increases in cost. The molding process becomes more critical, disc-handling time decreases, and heat-related effects are less acceptable in this new format (see Figure 1).
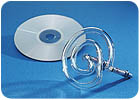
The customer informed us that continuous UV mercury lamps were not doing the job. In addition to the edge cure problem, the mercury lamps required excessive power to penetrate the thick coating, resulting in unacceptable cure times and excessive heat. To solve these problems, they turned to pulsed UV.
Pulsed UV provided a number of advantages for curing the thick coating resin, including the following.
- Deep penetration. The high peak pulse power easily penetrates thick coatings at significantly lower average power than mercury UV systems.
- Low heat. The short-duration pulses are fast enough to avoid heat buildup on the substrate, and the time between pulses acts as a cooling zone.
- Rapid curing. Tests confirmed that crosslinking the formulation used for the thick coating requires a lot of energy, fast. Pulse UV technology instantaneously delivers the required energy, thus achieving the rapid cure that this process requires.
- Edge curing. By using a unique spiral lamp with an outer ring designed to cure the edge of the disc at the same rate as the center, we eliminated the difficulty in achieving complete edge curing (see Figure 2).
- Flexible process capability. Our technology offers many configuration options, allowing customers to tailor a system to their specific needs. The systems are modular, and the timing and spectrum of pulses can be precisely adjusted and controlled to match the substrate's shape and chemistry.
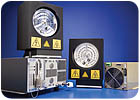
With pulsed UV in the process line, the Blu-ray Disc is going into production using the two-coat process to meet the immediate demands of the industry for more storage capacity. The customer also is developing a single-coat process to eliminate the need for the top hard coat - and high-peak UV pulses provide the right tool for this process.
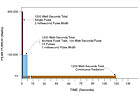
EFFICIENT PULSES
The major attributes of pulsed UV technology (deep penetration, thermal management, energy efficiency and fast curing) are all indicators of pulsed UV's ability to handle difficult curing applications. To recognize how pulsed UV achieves its unique curing results, an understanding of UV is required.UV can be delivered either continuously or in pulses. If we consider how the energy is delivered by these two means, we quickly understand significant differences. For example, consider two ways of expending 100 Joules of energy: one can either power a 10-watt continuous lamp for 10 seconds, or power a 1,000,000-watt pulsed lamp for 100 microseconds. The difference in peak power is readily apparent. This is analogous to penetrating a block of wood with a nail: one could press a nail into the wood with a finger for 10 seconds without effect, or exert the same amount of energy and drive the nail instantaneously into the wood with a single strike of a hammer. Pulsed UV, like the hammer, delivers light at high peak power to achieve deep penetration.
The high-peak-power UV pulses penetrate thick and/or opaque substrates much more effectively than, for example, UV light from continuous mercury UV lamps (see Figure 4). Pulses can deliver the energy necessary to cure an adhesive or coating in short, microsecond pulses. In addition to delivering more energy in a shorter period of time, users can specify both the pulse duration and frequency, allowing for appropriate cooling zones between the pulses to be designed into the process (see Figure 5). This essentially eliminates the possibility of substrate changes from exposure to unwanted thermal energy.
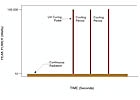
Pulsed UV curing achieves higher overall system energy efficiency. The high-peak pulses and the instant on/off capability greatly reduce the average power requirements. Another client, Time Warner, reduced the average power requirement for their manufacturing line from 6,000 watts using mercury vapor lamps to less than 1,000 watts with pulsed UV systems.
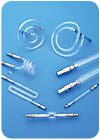
MATCHING OPTICAL FOOTPRINT
Many applications can use the same advantage that was so critical for the optical disc problem: lamp designs for pulsed UV can be matched to the target "footprint." Traditionally, mercury UV lamps have been limited to short-arc or linear-lamp designs. There are no such limits on pulsed UV lamps. The ability to shape the lamp to the application, providing better uniformity and enhanced matching of the UV light with the substrate, is a benefit for our customers in many applications. Pulsed UV lamps are available in a variety of shapes and sizes to match the required optical footprint (see Figure 6).LAMP SPECTRA
In addition to choosing the timing and energy of UV pulses, the lamp spectrum can also be optimized to match an adhesive or coating's chemistry. Pulsed lamps typically emit a broad spectrum, with wavelengths ranging from 200 nanometers (in the UV) through the visible spectrum to 1,000 nm. The spectrum of the pulsed lamp is "tuned" by appropriate design of the pulse configurator, which delivers the electrical energy to the lamp, thus helping achieve optimum energy delivery to the substrate. Pulsed UV is the only technology that allows changes to the spectrum without changing the UV lamp.In addition to general spectral shifts, the spectrum and sequencing of each individual pulse can be tuned to critically match the absorption requirements of chemical formulations. Consider a single pulse: at the beginning of the pulse, the output is delivered at shorter wavelengths. As the pulse continues in time, the output moves toward longer wavelengths. The amount of UV, visible and IR delivered can be adjusted for a specific application.
This unique characteristic of a single pulse was used to solve a major production problem facing the semiconductor industry. As part of the semiconductor manufacturing process, ions are pumped into the wafer. The industry was limited to 700 watts of ion implant dosage, even though existing ion implanters could deliver 1,500 watts. This limit was caused by the destruction of the coating at 700 watts. The industry was looking for a 10% improvement and tried every process possible (i.e., more intense continuous mercury UV, heat, etc.) without success. The problem was resolved by tuning the single pulse of light to deliver the right amount of UV energy and a thermal component with each pulse. Each pulse of a multiple-pulse train moved the chemistry toward a completely crosslinked cure with a greater ability to withstand the ion bombardment. The result was a coating that cured so completely that it could withstand 2,000 watts of ion implant dosage - 500 watts more than the capability of the most powerful implanter, and almost 200% higher than the 700-watt limit.
LOWER FORMULATION COST
Because pulsed UV results in higher performance and lower cost production of adhesives and coatings, more formulators are developing chemistry for pulsed UV. The formulations can use lower photoinitiator concentrations and still result in completely crosslinked chemistry. Some newly developed formulations require both UV and visible light for curing, which takes advantage of pulsed UV's range of wavelengths: the output from these lamps allows users to control the spectra of the overall output (and of specific pulses) to best match the UV to the adhesive's chemistry.MODULARITY
Pulsed UV systems are modular and simple: they do not require lamp warm-up time, mechanical shutter controls, water cooling or substrate rotation. The compact power supply and pulse configurator can be located at a distance from the lamp. Pulsed UV's physical and process flexibility is important because it helps system designers find the optimal balance between energy, heat, short cure times, and footprint. Systems can be customized to solve tough application problems.CONCLUSION
For the Blu-ray Disc application, pulsed UV technology provided the advantages of high peak power pulses that penetrate deeply to cure efficiently and completely, while maintaining low average power and relatively low heating. We were able to tailor key parameters to the application, including changing the peak power, pulse repetition rate, pulse sequencing, curing duration, and output spectrum. The ability to instantly turn the lamp on and off without waiting for the lamp to warm up or cool down was also important to our customer.The adaptability of the technology also means that development for one application lends benefits to others. The combination of Xenon's 40 years of experience with pulsed UV light and the unique capabilities of pulsed UV curing technology can help solve the toughest of curing problems.
For more information, contact Louis Panico, CEO, Xenon Corp., 37 Upton Drive, Wilmington, MA 01887; phone (978) 661-9033 ext. 225; fax (978) 661-9055; or e-mail lrpanicol@xenoncorp.com .