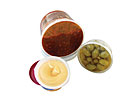
When introducing a new line of products, a regional food manufacturer knew that the selection of the packaging material would have a significant impact on the success of the launch. The manufacturer planned to serve both retail and institutional markets, and needed to develop packaging solutions that would address both markets' needs.
The decision was made to use polypropylene (PP) cups for the retail market. To address consumer desire for product visibility and easy access, a clear peelable lidding material was needed. To reinforce the quality image of the brand, it was important that the peel be smooth and consistent. The seal strength needed to be sufficient to provide consumer confidence that the seal integrity had not been breached yet not so strong as to create frustration. They did not want the consumer to need scissors to open the package. The lidding could not string or web when peeled, or leave an unattractive residue on the flange of the tray.
The institutional market was to be served through the use of large high-density polyethylene (HDPE) trays. To allow visual confirmation by the end user of the product in the tray, a clear lidding material was desired. The lidding was to be peelable to allow quick access to the product, yet needed to be strong enough to withstand the rigors of distribution and handling.
In order to compete with the national brands, the food manufacturer knew that cost was a significant issue. They recognized that manufacturing efficiencies would need to be very high with little spoilage or waste. A packaging solution that was cost-effective both in-the-door and out-the-door was required.
Of course, the materials used in the packaging needed to meet the Food and Drug Administration's indirect food additives regulations.
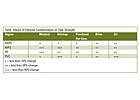
Seals and Peels From a Variety of Rigid Materials
To minimize inventory requirements, the packaging equipment was designed so that the same-width lidding film could be used for both the cups and the trays. However, in order to take advantage of this, a lidding solution that would seal and peel to both PP and HDPE was needed. In addition, the lidding film had to provide the seal and peel requirements necessary to meet the challenges of both the retail and institutional markets.Rollprint Packaging Product's Legato™ lidding film proved to be an excellent solution. Legato consists of an oriented polyester extrusion coated with Allegro® M sealant. It will seal and peel to a variety of cup and tray structures including high-impact polystyrene (HIPS), polyvinyl chloride (PVC), polypropylene (PP) and high-density polyethylene (HDPE).
Because of its wide sealing window and low seal initiation temperature, Legato is a very forgiving material from a manufacturing standpoint. This ensured quick setup times and few machine adjustments, and was one of the primary keys to allowing the manufacturer to meet its waste and efficiency goals. The figure illustrates the seal strength of Legato as a function of sealing temperature.
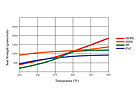
Seals through Contamination
With the speeds at which the manufacturer needed to run (approximately 75 cycles per minute), contamination on the flange was inevitable. While some reduction in seal strength was expected and acceptable, leakers were not. The manufacturer knew that ionomer-based sealants had an excellent reputation for sealing through contamination, and testing proved this out. However, they hoped to find a more cost-competitive solution that would perform well.Legato met this challenge. The sealant system used by Legato was designed to disperse contaminants into fine droplets or particles, providing a smooth peelable seal even under adverse conditions. The table shows the impact on seal strength when sealing through very heavy contamination.
Maintaining the appropriate lidding seal strength until the time of use was a concern for the manufacturer. During distribution and storage, the packaged product would be held refrigerated; in some cases, it was frozen. Experience had taught the manufacturer that many materials that perform well at room temperature do not hold up when subjected to sub-ambient conditions. The seals can weaken or even fail, and the lidding film can become brittle, tearing or breaking when stressed. Careful testing showed that the Legato maintained its excellent performance characteristics across the range of exposure temperatures.
Easily Printable
The manufacturer would be printing a lot code on the lidding destined for the retail market. A sleeve would be used to unitize the cups and provide a surface for the eye-catching graphics needed for the retail market. The lidding used for institutional applications would also be printed in line, via ink-jet process, with the contents as well the lot code. Legato's polyester outer layer provided an easily printable surface. Its naturally high surface tension allowed for crisp, clean high-speed printing without smearing. The manufacturer had the comfort of knowing that a version of Legato was also available with a chemically modified surface to further aid in printability.As the manufacturer looked at ways to improve branding, they wanted the option of purchasing the lidding film preprinted with their logo or other brand identifiers. Legato is available surface- or reverse-printed with up to eight colors.
Technical Support
The manufacturer was surprised at how painless the implementation process was. Prior to the commercialization of the Legato lidding film, Rollprint went through a rigorous validation process. The appropriate controls were put in place to ensure that the manufacturing process was both capable and consistent. This assured the manufacturer that the lidding material would perform as expected day in and day out.When it came time to qualify the material on the manufacturer's equipment, Rollprint was there to help establish operating windows, assist in any troubleshooting that was needed, provide testing support in their packaging laboratories, and, ultimately, assist with validating the manufacturing process.
The result was a packaging system that was robust, efficient and cost-effective. Waste and spoilage goals were exceeded by more that thirty percent, and the product was successfully launched on time and within budget.
For more information on films, contact Rollprint Packaging Products Inc. at (630) 628-1700 or visit http://www.rollprint.com .