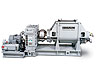
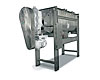
Industries that require process equipment but are clinging to such a cautionary approach to business may still be able to increase production while improving their efficiency and relevance in today’s economy. In particular, two pieces of process equipment are bringing about the best of both worlds for manufacturers of products such as silicones, sealers, inks, adhesives, resins and more: the double-arm mixer extruder and the ribbon blender.
Double-Arm Mixer Extruder
When cost is a driving factor, a double-arm mixer provides businesses with an economical solution to their process equipment needs. By answering the myriad challenges encountered in today’s industrial mixing applications, a double-arm mixer affords users significant value.Constructed of high-quality materials, double-arm mixers are engineered to provide decades of service with minimal maintenance. With less frequent replacement required and fewer dollars spent on upkeep and repairs, business owners enjoy even greater cost savings over the long-term life of the equipment.
The financial benefits of a double-arm mixer continue to add up when the equipment’s compact, space-saving design is taken into consideration. As the Los Angeles Times reported in January, “Propelled by … the age-old imperative to save a buck, companies [are] shift[ing] into smaller offices spaces.” In fact, since the 1970s, American corporations have downsized from about 600 sq ft to just slightly over 200 sq ft per employee. Those figures equate to a 150-250% reduction in corporate space per employed individual. The downscaling tendency hasn’t run its course yet. “The space allocation could hit a mere 50 square feet by 2015,” notes one workplace trend expert.
Businesses that have embraced this downscaling trend will be drawn to the double-arm mixer’s compact, space-saving design. They’ll also appreciate how quietly it operates, even under full load, thereby lowering the likelihood of noise distraction.
Of course, versatility cannot be overlooked when it comes to getting the most mileage out of one’s money. Double-arm mixers flexibly adapt to a variety of mechanical options and construction materials. In doing so, they enable the cost-effective configuration of a heavy-duty mixing machine.
Business owners should not assume that a decrease in functionality and/or quality is the tradeoff for a double-arm mixer’s affordability. The triple output shaft of the MXT transmission eliminates the need for secondary and supplemental gear cases. The double-arm mixer also comes standard with a multitude of options.
Unlike similar industrial mixing equipment, double-arm mixer extruders feature a product deflector in the bowl that helps relieve pressure against the auger packing gland. They are also capable of heating or cooling in a looped arrangement housed directly within the bowl’s chassis and the sidewalls of the mixer. As a result, pinpoint control over the mixing environment’s temperature is possible.
The double-arm mixer’s auger screw affords an array of capabilities as well. Its bidirectional operation enables convenient alteration between mixing and discharging of the bowl contents. This functionality significantly reduces the time needed to sequence the mixer through a product cycle. The equipment also provides adaptability, with fixed speed, hydraulic variable speed and variable frequency drives for a variety of mix applications.
Ribbon Blender
In addition to providing the same economic benefits, versatility, problem solving capabilities, high-quality construction, long-lasting durability and low maintenance as double-arm mixers, ribbon blenders also offer their own set of process equipment benefits.The agitator design provides excellent mixing efficiency to minimize product cycle time and blend product consistently and evenly. Heavy-duty construction enables product density of 75 lbs/cu ft to be processed with a standard drive configuration. As such, expensive enhancements are unnecessary for most process equipment applications.
The mixer body and agitator are both constructed of a high-durability brushed stainless steel alloy that is resistant to chemical corrosion and mechanical fatigue. The cover can also be easily removed and replaced using quick-release clamps. In addition, both the cover and feed hatch feature gaskets that won’t harden over time.
A safeguard proximity switch is added to the unit for customer wiring, and the drive assembly is completely enclosed for safety and durability. In addition, a discharge valve guard is provided on all ribbon mixers (with optional discharge valve mechanisms also available).
Like double-arm mixers, ribbon blenders provide reliable, quiet operation. A high-quality TEFC motor drives a shaft-mounted torque arm reducer using V-belts and sheaves. Noise reduction stems from the heavy-duty, self-aligning support bearings, which provide smoother rotation of the agitator and drive assembly components.
Ribbon blenders also share their construction material with double-arm mixers. The split design packing glands are constructed of stainless steel and can be supplied with a variety of packing materials to minimize leakage and offer ease of maintenance.
Finally, the ribbon blender’s agitator discharges product through a bottom opening for easy use. The product flow is regulated by a manually operated knife-gate valve, so the user maintains complete control over the process.
For more information, contact Aaron Process Equipment, 735 E. Green St., Bensenville, IL 60106; phone (630) 350-2200; fax (630) 350-9047: e-mail sjakubiak@aaronprocess.com, or visit www.aaronprocess.com.