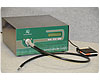
The UV curing process is a photochemical reaction in which free-flowing molecules, excited by UV radiation, link to form solid polymer chains.
Bonding technology has advanced from glass, steel and mechanically fastened products to multi-level polymer materials and superior ultraviolet (UV) curing methods. With the continued movement toward more compact devices, the need to reliably bond smaller and smaller compounds has never been greater.
Process History
UV-curable inks and coatings were first introduced in the 1960s as an alternative to solvent-based products. Conventional heat and air drying were originally achieved through solvent evaporation, which shrinks the initial application of coatings by 50% and creates environmental pollutants. Since UV curing avoids the use of solvents, however, it results in zero environmental pollutants, no loss of coating thickness, higher productivity in a shorter amount of time, and a reduction in waste.UV curing involves 100% solids in a fluid state. The UV curing process is a photochemical reaction in which free-flowing molecules, excited by UV radiation, link to form solid polymer chains. Small amounts of chemicals known as photoinitiators act as catalysts, allowing the UV-curable adhesives and coatings to solidify or cure the instant that the UV light hits them.
No hazardous substances are released during the UV curing process. The volatile organic compounds (VOCs) found in the noxious, flammable solvents used by conventional coatings, adhesives and inks are completely eliminated. The environment benefits from the fact that the amount of liquid applied before the curing process is the same amount remaining after the curing is complete: no leftovers, no VOC emissions and no compliance problems.
UV curing is now a multi-billion-dollar industry and constitutes about 4% of the industrial coating market. It is currently used in many industries, including automotive, electronics and graphic arts.
Benefits
When UV light penetrates through a substrate and causes the liquid-to-solid chemical reaction, UV adhesives can cure materials to glass, stainless steel, or other difficult-to-bond substrates. Although UV-cured adhesives mimic the chemistries found in any other polymer, they offer several major advantages. For example, the chemical bonding reaction happens very quickly, and high-quality UV ink goes farther than solvent-based ink. As a result, UV curing can increase throughout four times over solvent-based processes. Cleanup time practically disappears, so the time available for production is increased significantly.UV adhesive bonds display a range of physical properties that are similar to those of thermal or air-dried adhesives. As soon as they are cured, UV adhesives display a number of crucial physical properties (e.g., high tensile strength and desirable elasticity) between the substrate and the adhesive. For example, UV adhesives can feature a high compression modulus, which determines the amount of stress the material will exhibit under strain, and a low elastic modulus, which ensures the adhesive’s stretchability.
UV light replaces the use of thermal sources that can color adhesives in undesirable ways. They are beneficial for medical device applications because the excitation of their photoinitiators occurs in the UV region, which prevents some adhesives from yellowing. Curing mechanisms that operate in the visible light region, in contrast, include yellow photoinitiators-an undesirable characteristic that can affect the adhesive’s color.
UV dryers also take up less space than traditional dryers, so manufacturers can use the extra space for more revenue-producing equipment. UV technology uses less energy, which translates to a significant cut in operational costs. In addition, the technology does not pollute the inside or outside of the facility. A cleaner workspace means healthier employees and a “greener” environment.
Technology Advances
UV light-emitting diode (LED) curing has been developed to offer an advanced, high-performing curing technology. UV LED technology offers multiple advantages compared to traditional lamps: it is mercury-free; does not generate ozone; and allows for accelerated production speeds, lower production costs and reduced energy use. While traditional mercury-based UV curing lamps dominated the market in the past, more efficient and environmentally friendly UV LED technology is now becoming a superior alternative for spot, flood and conveyor curing formats.For additional information, email beustace@auvco.com or visit www.americanultraviolet.com/curing_solutions.