BASF has made a game-changing breakthrough toward sustainable snack packaging that can help companies and communities everywhere get closer to their goal of zero waste. This past fall, the company partnered with The Seattle Mariners and used the iconic snack of the American pastime—peanuts—to debut prototype packaging developed with its advanced biopolymer technology. The first 10,000 fans to arrive at Safeco Field that day received a free bag of peanuts in a 100% compostable snack bag.
Previously, most empty snack packages, such as for cookies or breakfast bars, could only be sent to the landfill because most conventional food packaging is neither recyclable nor compostable. It consists of a multi-layer film structure comprised of traditional plastics and adhesives. The multiple layers are needed to provide the barriers, colorful print and necessary adhesives that bond all the layers together. These varied materials are not easily separated for disposal, making recycling problematic. Composting the package wasn’t an option, either; the chemicals those layers are made from cannot be composted.
BASF’s new compostable food packaging film structure is composed of a six-layer film (see Figure 1). The innovative design allows for the entire structure to be composted.
“Flexible packaging with this BASF technology is a big step forward for the snack food industry,” said Kimberley Schiltz, manager of Market Development, Consumer Packaging. “It means that popular snack foods can be brought to market in compostable packaging that delivers needed shelf life at a competitive price point, with a more sustainable ‘end-of-life’ solution than with conventional packaging materials.”
Like all advances in sustainability, major breakthroughs must balance economic and environmental interests. “Whenever there are contaminants in our compost stream, like regular snack bags and candy wrappers, we have to pay a premium to have them removed by hand,” said Scott Jenkins, vice president of Operations for the Mariners. “If all of the snacks sold at Safeco came in compostable packaging, it would represent a significant savings of time and money for the team and get us a whole lot closer to achieving zero waste.”
Earlier attempts have been made to introduce fully compostable snack packaging; however, those fell short of consumer expectations. BASF’s research finds that its biopolymers technology can meet those expectations and provide a viable solution to the snack food packaging industry.
“Compostable snack food packaging made with BASF’s advanced technology can put us much further down the path to a zero-waste world, much faster,” said Stephan Banchero, general manager, Cedar Grove Composting.
As municipalities grapple with how best to implement greening initiatives and engage citizens, this kind of technology could represent a more convenient alternative to the punitive approach already in place in some cities.
“We welcome technological advances like this that inspire our entire society to move toward sustainability and help municipalities like the city of Seattle divert more waste than ever away from landfills,” said Brett Stav, senior planning and development specialist, Seattle Public Utilities.
Advancing Adhesives: Game Changer
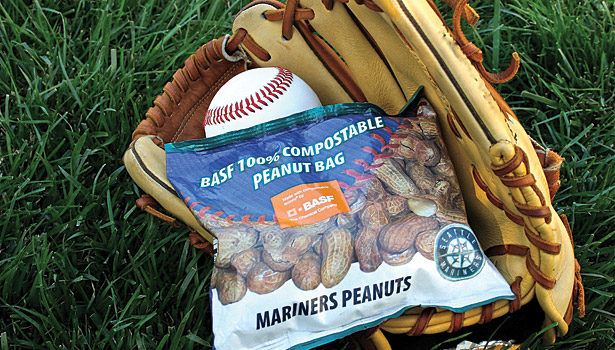
BASF partnered with The Seattle Mariners to debut prototype packaging that contained a free bag of peanuts in a 100% compostable snack bag.

Figure 1. Compostable Food Packaging Layers