Operating in the food and beverage industry requires careful considerations for packaging—from food safety to aesthetics. Therefore, when it is time to make an update to packaging, it is important to revisit key factors related to adhesion, including:
- Field performance
- Resistance to hot and cold
- Shelf appeal
- Line performance and material processing
- Changes in cost due to label updates
Familiar with these considerations, a national baby-food manufacturer was considering a packaging change—from paper labels to clear poly labels on its recyclable glass jars. In updating the look of the packaging, the question surfaced: Will the current adhesives used with the paper label be visible through the proposed poly label?

Lap bond strength was evaluated using a modified loop tack test, where two loops of label material are adhered to each other (instead of one loop contacting a metal plate).
Having relied on APPLIED Adhesives to provide adhesive products and expertise for years, the baby-food manufacturer engaged the company to explore the potential for the proposed packaging update. The APPLIED Technical Services team focuses on helping customers navigate adhesive-related challenges.
Evaluating New Products without Sacrificing Production Time
Time is quite literally money on a production line. One research study estimates that the industry can rack up losses in the range of $260,000 per hour of unplanned downtime.1 As such, the baby-food manufacturer was looking for help with pre-qualifying the updates prior to making significant investments of time or materials in switching to the new, clear poly labels.
The adhesives that were being used on the glass jars with the paper labels included a hot-melt pressure-sensitive adhesive (PSA) and a semi-PSA. The APPLIED Technical Service team utilized its in-house adhesive lab to analyze the project from a holistic perspective, considering:
- What equipment is used and at what speeds?
- What are the substrate materials? What challenges do they present? Is the label sized appropriately to allow for enough room for the adhesives?
- How is the bond assembled? How much glue is being used?
- What is the condition of the product prior to labeling (e.g., temperature, moisture, etc.)?
- What conditions will the bond be subject to from production to end use?
- What are the cost objectives?
- What are the manufacturing plant’s conditions, processes, and areas of expertise?
At the start, APPLIED had confidence that hot-melt PSAs were the right choice for this type of application (label on a glass food jar) because the residual tack is present at room temperature, offering significant flexibility to overcome potential disruptions in handling. Even though there was a strong initial hypothesis, APPLIED worked to identify the key performance attributes of the ideal adhesive to enable a comprehensive evaluation.
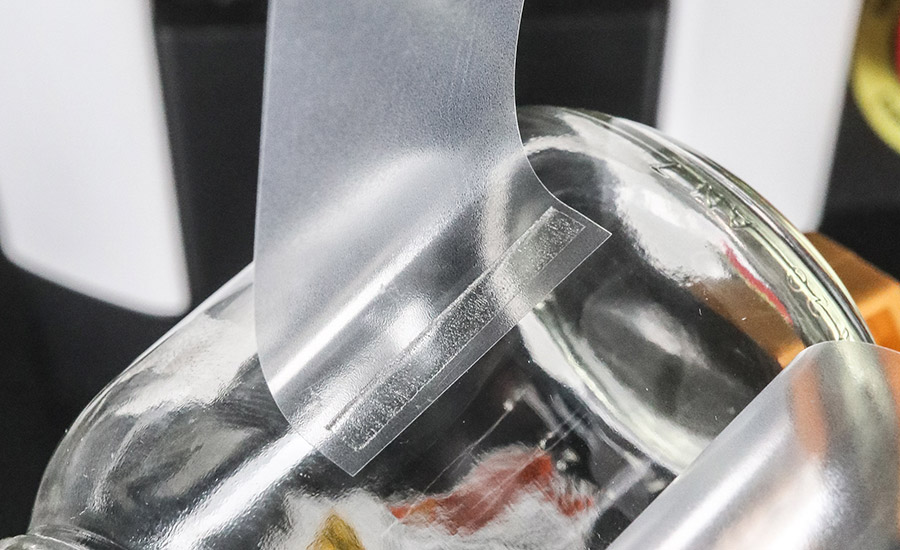
In pickup bond strength testing, a force tester grips the glass jar and pulls the label at an angle to the bond.
In this case, taking a comprehensive look enabled the team to design the just-right analyses for the baby-food manufacturer’s needs—including some that were not initially requested but proved to be beneficial. For example, although the initial question posed in this case was around adhesive visibility, the APPLIED team wanted to ensure that the necessary adhesion properties would carry forward with the poly labels, which have a lower dyne level (surface energy) than paper labels.
Through continued discussion, the baby-food company became optimistic that APPLIED’s analysis could result in the ability to consolidate to a single adhesive for the proposed poly labels and the current paper labels. This solution would also offer the baby-food manufacturer the flexibility to run multiple product lines or substrates in the future.
Testing with Real-World Conditions
Quantitative performance can demonstrate not only how a product works, but why. This is best done using the same materials and methods that would be used during production.
The APPLIED team requested the baby-food manufacturer send samples of the materials used during production, including the glass jars, current paper labels, and proposed clear poly labels. Using the supplied examples of current products to baseline performance and set targets, APPLIED would be able to examine adhesive application to identify potential performance challenges, such as poor machining or pattern location.
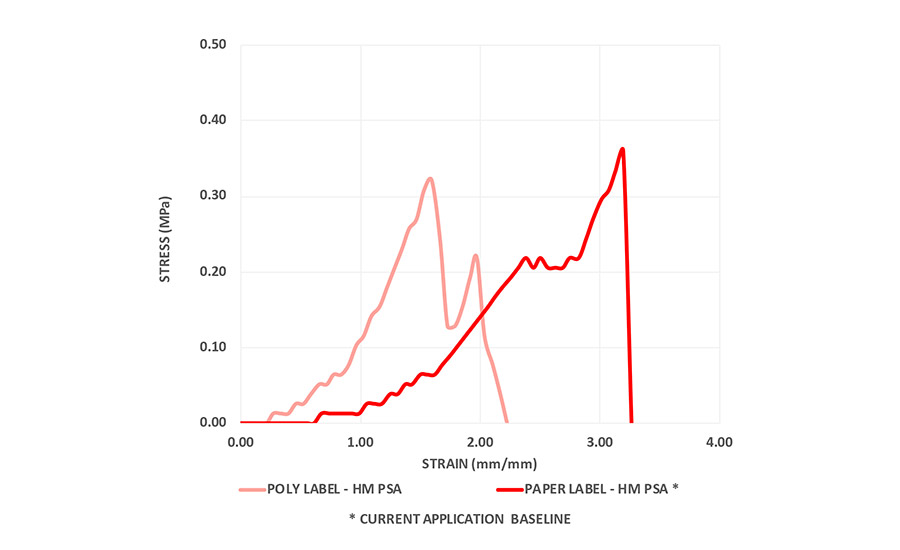
Figure 1. The overlap test results showed peak stresses of 0.36 MPa for the paper labels and 0.32 MPa for the poly labels.
Precisely mimicking actual production conditions, the materials were set up in an application-appropriate manner for customized testing unique to the project (e.g., applying adhesive in a method similar to an actual production line capable of speeds up to 1,000 units per minute). The testing procedures included:
- Making samples on release paper of each current adhesive
- Trimming film samples
- Simulating pickup application (applying adhesive to the glass jar, removing release paper, applying label stock over the adhesive film, and heating the jar for adhesive wet-out)
- Simulating lap application (applying adhesive to label stock, removing release paper, applying a second label over the first, and heating the assembly for adhesive wet-out)
- Conditioning samples for 24 hrs before placing in force-testing equipment to simulate tensile forces
Thorough testing examined:
- Lap bond strength using a modified loop tack test, where two loops of label material are adhered to each other (instead of one loop contacting a metal plate)
- Pickup bond strength using a force tester to grip the glass jar and pull the label at an angle to the bond
- Visibility by applying the adhesive to the poly labels and applying the labels to the glass jar
Providing a Data-Driven Recommendation
Prior to beginning this evaluation, a thorough review of available technical data sheets indicated that multiple products may have been suitable for the new product label. However, the APPLIED evaluation concluded that one specific PSA was clearly the best option for the application.
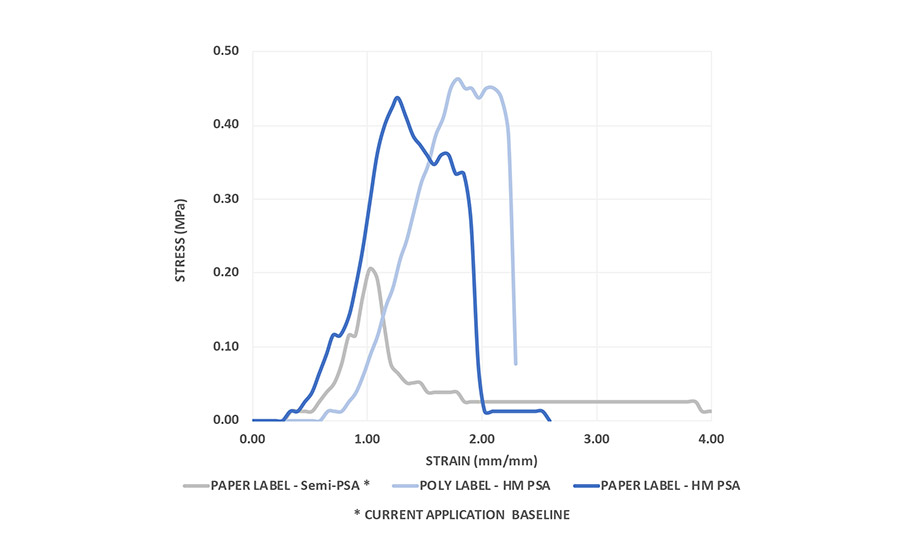
Figure 2. After switching to the PSA, pick-up testing showed that bond strength was effectively doubled on the paper labels, with a peak stress of 0.43 MPa. The PSA showed further improved bond strength on the poly labels, with a peak stress of 0.46 MPa.
The overlap application results confirmed compatibility of the PSA with both paper and poly labels, showing peak stresses of 0.36 MPa and 0.32 MPa, respectively. The pick-up application using the semi-PSA on paper labels showed a bond strength with a peak stress of 0.21 MPa. By switching to the PSA, the baby-food company was able to effectively double the bond strength on the paper labels, with a peak stress of 0.43 MPa. The PSA shows further improved bond strength on poly labels, with a peak stress of 0.46 MPa.
Furthermore, the APPLIED team also uncovered a process improvement to consolidate and use one PSA for all applications, which created additional benefits for the baby-food manufacturer. Although the two adhesives used with the paper labels each have roughly the same cost, switching to one adhesive product decreases inventory requirements. In addition, a single product is one less worry for line operators. It eliminates the need to fill different tanks with separate adhesives, improving line productivity.
For more information, visit www.appliedadhesives.com.
Reference
- “Minimising Production Downtime in Food and Drink Manufacture,” HPS Hygienic Pigging Systems, www.hps-pigging.com/minimising-production-downtime-in-food-and-drink-manufacture.
Note: Opening image courtesy of Fabio Camandona Via iStock/Getty Images Plus. All other images courtesy of APPLIED Adhesives.