When identifying solutions that can offer assurance and longevity, the maintenance and reliability of assets repairs can be challenging, this white paper will look into the use of structural adhesives as the first-choice solution.
Structural adhesives can be used for affixing metal substrates or components, as they provide high modulus and high strength. However, they are not currently internationally recognized like the traditional methods even though adhesives are already used in a wide range of industries, such as aerospace, rail, and construction.
Traditional practice such as welding, riveting, nuts and bolts, and mechanical fixing are perceived as the go-to method. However, they all have their inherent inadequacies. Welding can be hazardous to health; riveting and nuts and bolts concentrate the stress locally; and mechanical fasteners can concentrate stress.
This paper introduces a novel, two-component, solvent-free toughened epoxy adhesive material that provides high adhesion to metallic substrates while also being able to withstand high movement or cyclic fatigue in comparison to general epoxy materials.
As well as potential application areas, the article also discusses a number of benefits, including ease of use, load bearing, and impact-resistance properties.
Introduction
Most industrial maintenance or repair procedures can either involve welding or use of mechanical fasteners as these can be perceived as easy and quicker; however, these procedures might initially seem to correct the issue but may cause more harm than good. Depending on the repair situation, for instance, welding or drilling to connect mechanical fasteners on a storage tank containing flammable liquid is not recommended for obvious reasons. This is where a structural adhesive can really offer a solution for that maintenance repair.
There are many structural fixings used across a whole range of industries that may be part of any maintenance or repair; these include support brackets such as cable trays, antennas, heating coils filter pans, or any other internal fixtures in vessels that suffer from corrosion, impact, or vibration damage. Within construction, there are fire-water deluge systems, nozzles connections, facades panels, and signs that can require maintenance over time or adverse weather conditions. Process equipment or piping can suffer from thinning of the steel or even through-wall defects that will need either monitoring or repairing depending on whether the integrity of the equipment has been lost. Structural fittings are generally used to fix static members but may be subjected to forces that are unknown at time of installation. This could include thermal cycling of the joints, cyclic loading, or vibration due to fatigue of a component. If there are repairs due to the above, the contractor maybe in a situation where a choice of solutions can be made; then, the strengths and weaknesses need identifying.
Welding is regularly used for repairs as it is widely available while being well regulated with high customer confidence and high repair strength. It does come with its inherent risks: both to the material (by heat stressing) and the user, as welding can cause both acute and chronic health risks.1 Application of welding repairs onto live piping sections, storage tanks, or process systems and equipment should not be undertaken due to the high temperatures involved, not to mention the combustible nature of the process fluid or gas running through or being stored in these components.
Bolted joints are seen as simple and low cost due to the ease of disassembly and reassembly. These can be dissimilar metals; but the use of dissimilar metals will contribute to galvanic corrosion and add weight to the joint, thus requiring routine inspection and tensioning. With the drilled holes in the support material, stress distribution is not uniform and concentrated at the holes.
Structural adhesives have high bond strength while being lightweight. Adhesive is applied to cover the entire joint, resulting in uniform stress distribution, reducing metal distortion under strain.
A Strong Bond
Adhesive bonding is the joining of similar or dissimilar members together while creating permanent high strength bonds that can transfer structural stress without loss of structural integrity.
Regardless of the joint type used, it is important to understand the different stresses that are imparted onto a bonded assembly. Adhesives perform the best when the stress is two-dimensional to the adhesive, allowing the force to be applied over the entire bond area.
Joints that are well designed for adhesives place most of the stress into compression or shear modes; adhesives perform the worst when stress is one-dimensional to the adhesive, concentrating the load onto the leading edge of the bond line. Joints placing stress into cleavage or peel concentrate the stress onto the leading edge, which may lead to premature bond failures, especially if subjected to vibration, impact, or fatigue.
Bonds of high strength are achieved after cleaning of the substrate by removal of any contaminants, followed by the roughening of the substrate, generally in the form of grit blasting to internationally recognized standards2. This is why surface preparation is critical to success regardless of the type of adhesive used.
There are three types of bonding that are important to achieve to ensure good adhesion. These are: adhesive, chemical, and mechanical. Adhesive bonding relies on surface energy to generate adhesion to the substrate. While chemical bonding relies on chemical bond formation and electronic bonding to produce adhesion. Mechanical adhesion is achieved through the creation of an irregular profile that allows a deeper profile to be produced.
The types of structural adhesives available have been summarized in Table 1.
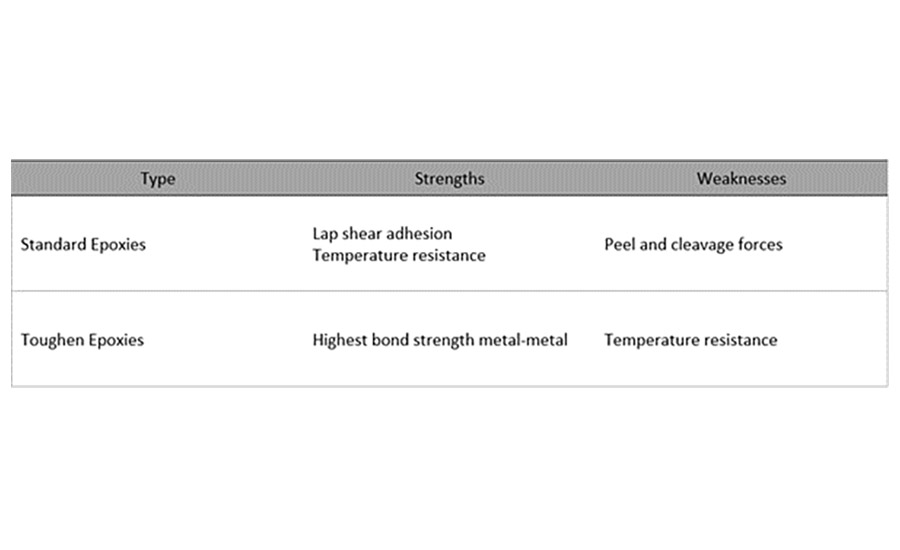
There are two types of failure mechanisms associated with structural adhesives: cohesive failure and adhesive failure. These failure mechanisms are described below.
- Cohesive failure occurs in the bulk layer of the adhesive material. This failure mode is limited by the strength of the adhesive material and can be caused by insufficient curing of the adhesive and applications at a greater thickness than that recommended, among others.
- Adhesive failure occurs when the mechanical adhesion between the adhesive and the parts being joined is overcome by the loading. This failure mode is associated with inadequate surface preparation, presence of contaminants, or insufficient curing of the adhesive, among others.
Background
Design considerations for Belzona 7311, the adhesive being studied, were based on both technical target requirements and a practicality approach, as summarized in Table 2.
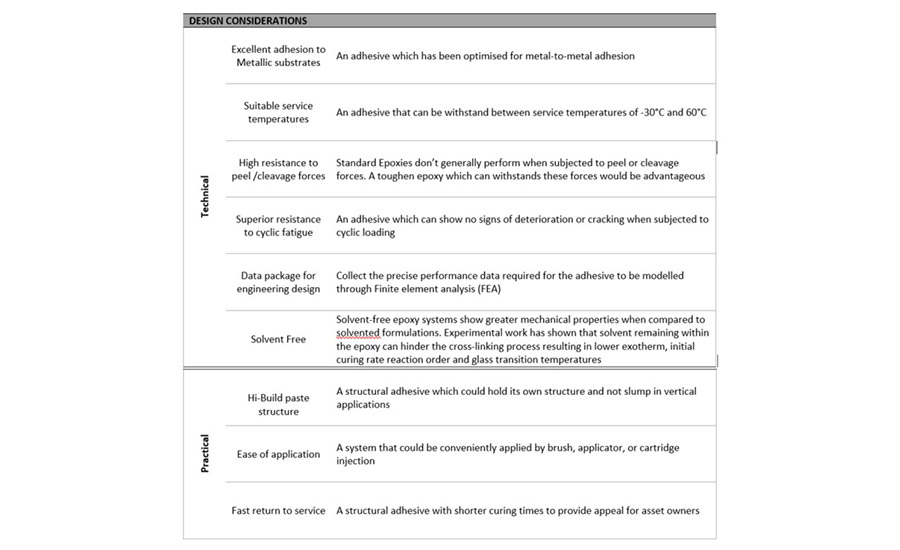
The adhesive was subjected to the following tests and evaluation protocols to ensure that it met the design criteria previously discussed. Where possible, internationally recognized standards were used.
- Cleavage Adhesion – ASTM D10623
- Tensile Shear Adhesion – ASTM D100244
- Tensile Fatigue Resistance – ISO 96645
- Impact Resistance – ASTM D2566
Experimental Procedure
1. Cleavage Adhesion – ASTM D1062
Cleavage adhesion is used to assess the strength of an adhesive bond between two substrates when exposed to cleavage stress.
The adhesive was applied between two identical grit-blasted metallic cleavage test pieces to create a fixed bond area of 125mm² of minimal bond-line thickness. The specimen was allowed to cure then attached to a 25kN tensometer using suitable grips. The tensometer then applies a load at a fixed rate of 1.3mm/min, exerting a cleavage force on the specimen until bond failure. This test is repeated five times so an average force can be calculated.
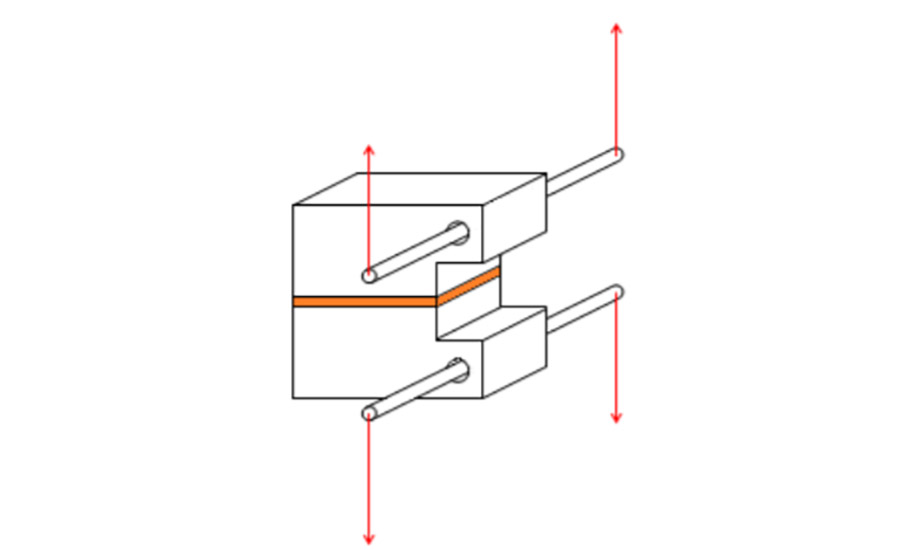
2. Tensile Shear Adhesion – ASTM D1002
Tensile Shear Adhesion or lap shear adhesion is used to determine the adhesive strength of a material when bonded between two ridged metallic substrates.
Samples are 100 x 25.4 x 2mm and are overlapped lengthwise by approximately 12.7mm and bonded to a minimal bond-line thickness with the adhesive.
The specimen was allowed to cure then attached to a 25kN tensometer using suitable grips. The tensometer then applies a load at a fixed rate of 1.3mm/min, exerting a cleavage force on the specimen until bond failure.
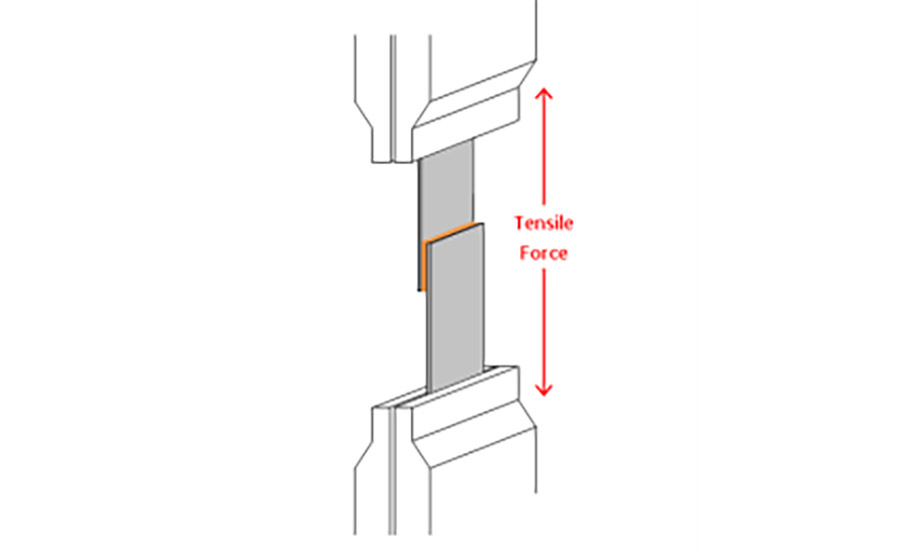
3. Fatigue Resistance – ISO 9664
Fatigue resistance is the highest stress that a material can withstand for a given number of cycles without breaking. A standard static Tensile shear adhesion test was conducted to determine the mean breaking stress — 24.17 MPa following this 35% of the mean breaking stress value is used as the mean stress in fatigue testing — 35% mean shear stress = 8.461 MPa (24.17 MPa x 35%).
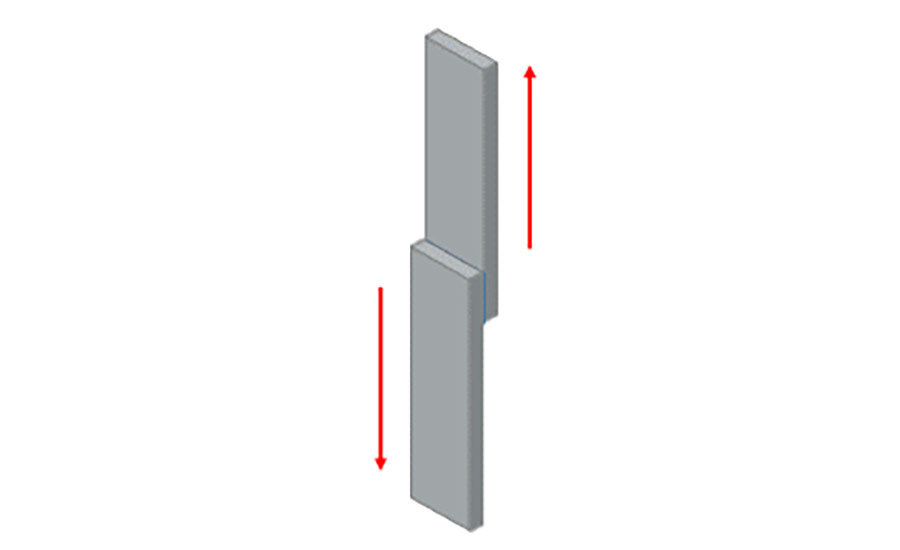
At four different alternating stresses, fatigue testing was conducted at 30Hz until failure:
- 80% = 6.8 MPa (8. 461 MPa x 80%) Stress amplitude cycles between
- 60% = 5.1 MPa (8. 461 MPa x 60%) Stress amplitude cycles between
- 57.5% = 4.9 MPa (8. 461 MPa x 57.5%) Stress amplitude cycles between
- 55% = 4.7 MPa (8.461 MPa x 55%) Stress amplitude cycles between
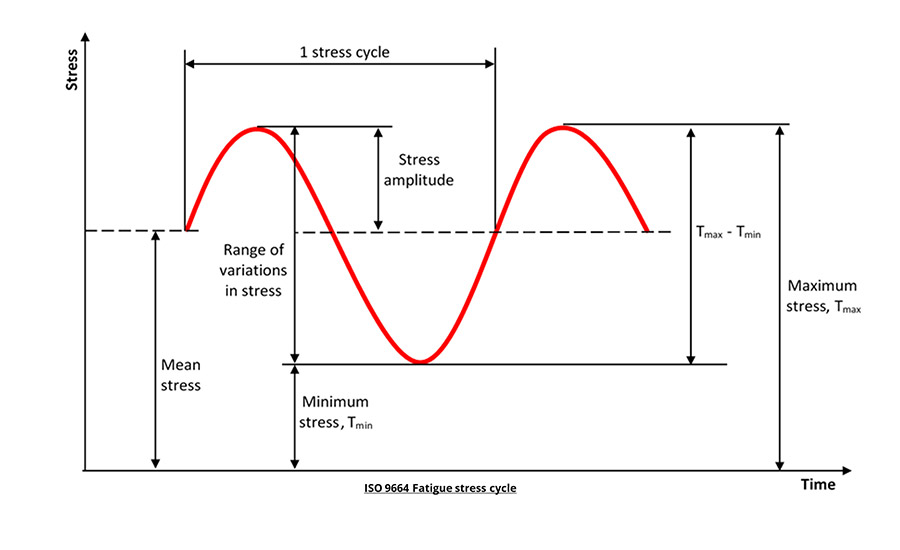
4. Impact Resistance – ASTM D256
Impact tests can be used to assess the toughness of a material. A material’s toughness is a factor of its ability to absorb energy during plastic deformation. Brittle adhesives have low toughness as a result of the small amount of plastic deformation that they can endure. Tougher materials on the other hand can absorb greater energy during fracture and thus have improved impact resistance.
The Izod impact test allows for samples to be tested in two forms: either “notched” or “un-notched.” In our case, the testing will be notched, which has a V-shaped notch of approx. 2.5mm in depth with a total defect angle of 45° in the center of a specimen sample with dimensions of 12.7 x12.7 x 65mm. The notch concentrates stress and allows measurement of crack propagation.
Non-standard testing:
5. 3-Point Load Test
This comparative technique is used to assess the relative flexibility of adhesives when applied to a metallic substrate. In this test, a mild steel panel of dissimilar dimensions – Plate 1 550 x 50 x 10 mm thick and Plate 2 225 x 50 x 10 mm thick – are stressed to the point the adhesive fails. The panel is held in position at two points, one at either end of the sample, and is gradually stressed at a single point in the center of the specimen via a hydraulic press as seen in figure 5. The greater the displacement i.e., the further the press travels until failure, the more flexible the adhesive. The thickness of the adhesive will influence the degree of flexibility, so analysis should be duplicated for repeatability purposes. In the case of this testing at the manufacturing stage, the specimens were compressed by hand pressure only to try and replicate “in field” applications of achieving below the maximum bondline thickness of 2mm.
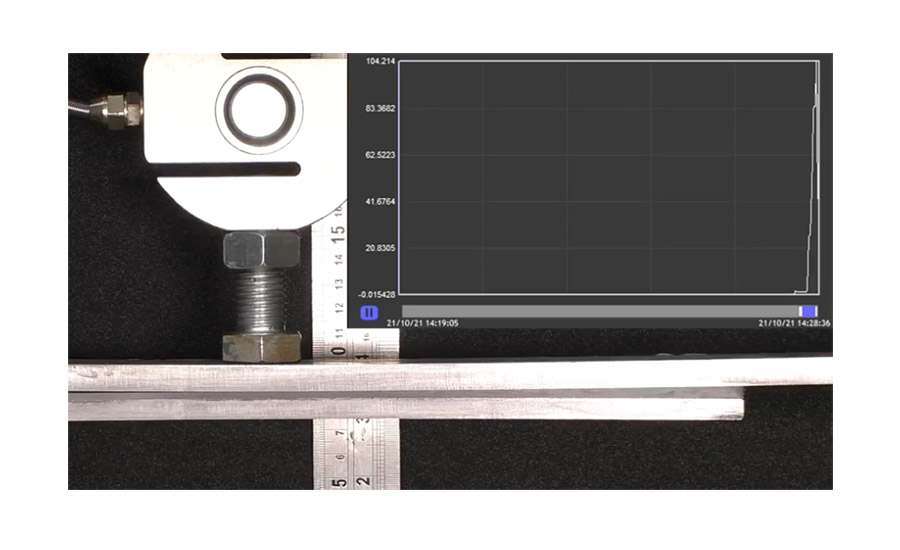
Testing Results and Discussion
1. Cleavage Adhesion – ASTM D1062
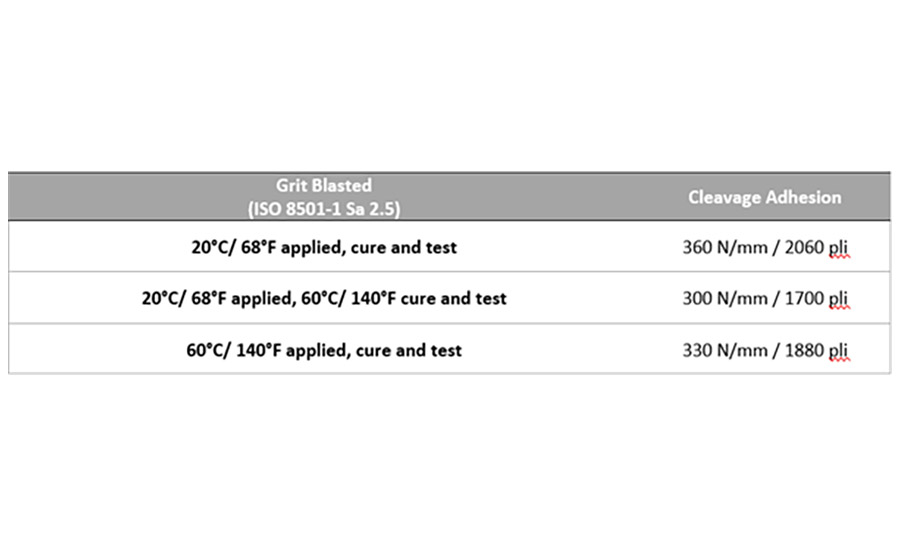
2. Tensile Shear Adhesion – ASTM D1002
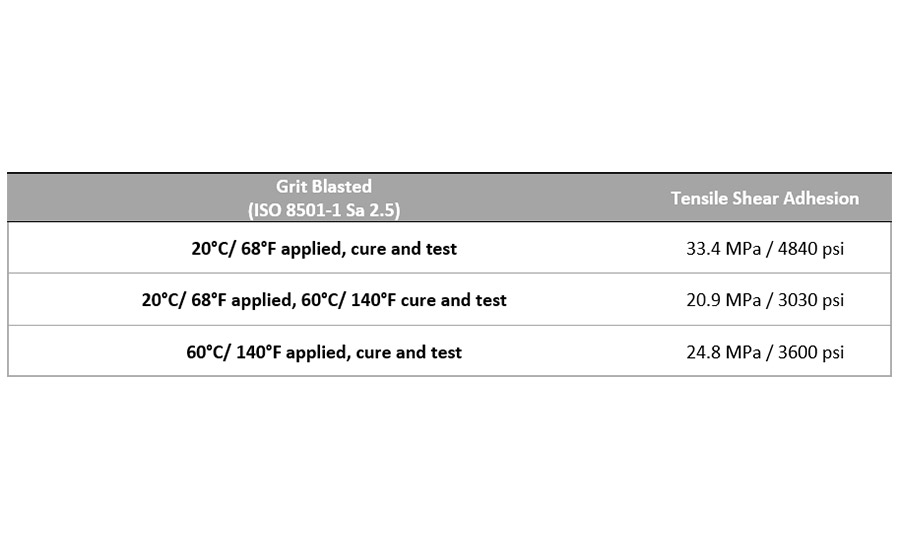
3. Tensile Fatigue Resistance – ISO 9664
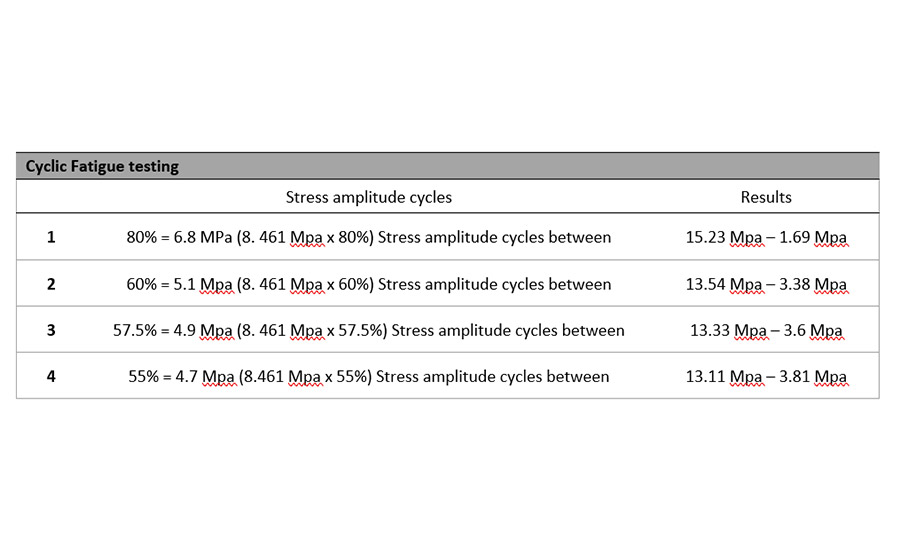

From a mean breaking stress of 35% (8.461 Mpa), the adhesive will survive 106 cycles at 56.6%, with an alternating stress amplitude of ± 4.791 Mpa = 13mpa to 3.67 Mpa.
4. Impact Resistance – ASTM D256
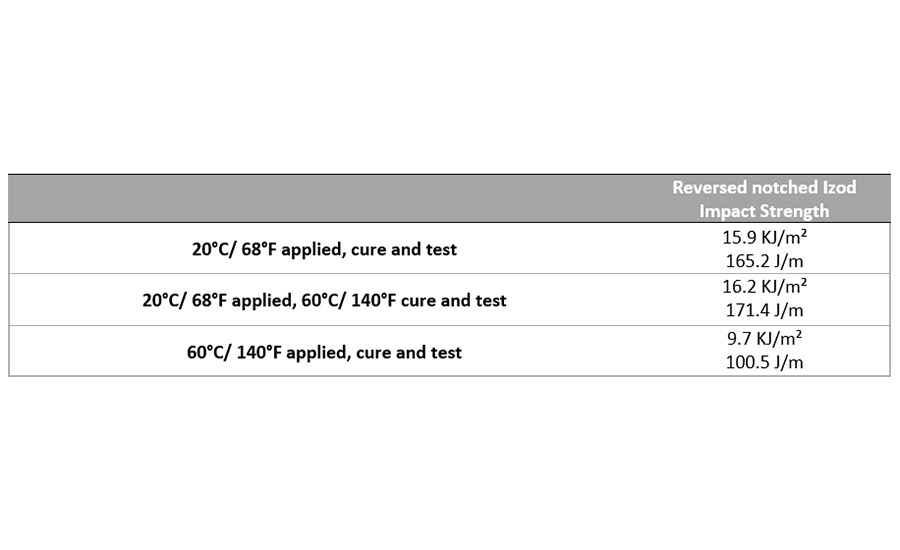
5. 3-Point Load Test
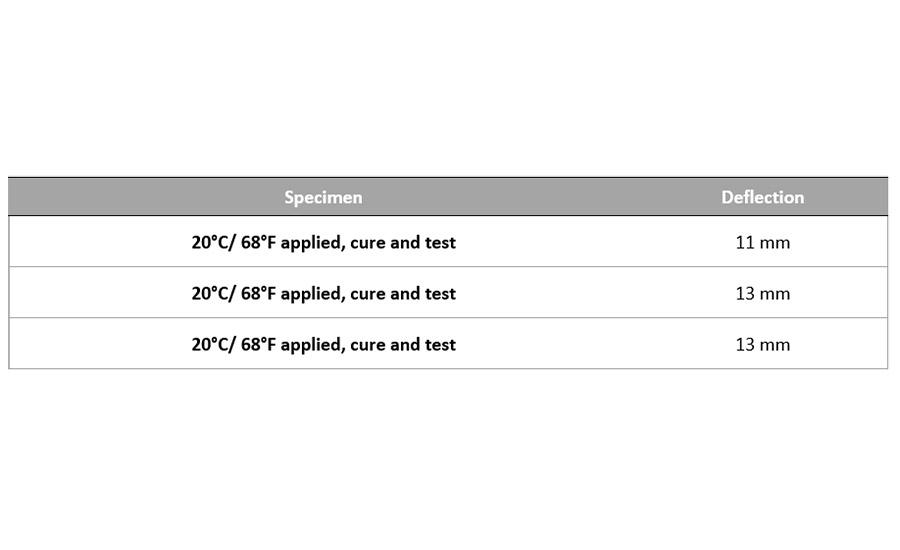
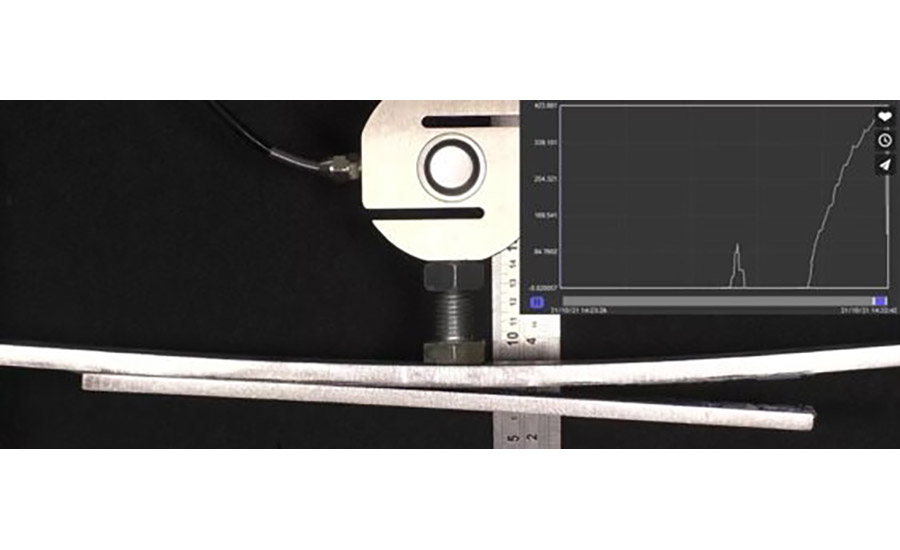
Conclusions
Several conclusions can be drawn from the use of the adhesive as a solution for the repair or maintenance of assets.
- The adhesive offers high resistance to structures that are subjected to forces such as peel, cleavage, vibration, or cyclic loading. These include, but are not limited to, support brackets for fire deluge systems, internal and external fixtures on process equipment, wear pads and wind girders on storage tanks.
- As the adhesive offers an array of additional practical features including ease of application, ability to hold its own structure when placed in vertical applications, and superior adhesion to metallic substrates, the toughened epoxy can be used on structural support reinforcements, load transfer supports, and metallic staircases and ladders.
- Plate bonding to repair thinning or through-wall defects on areas such as pipe/piping, process equipment, storage tank floating roofs and platform decks can utilize the adhesive, as it offers high impact resistance and flexural properties.
- The adhesive has been optimized for metal-to-metal adhesion and exhibits an extensive data list with over 20 tests solely based on adhesion. The performance data can be used for Finite Element Analysis (FEA) or simulations to aid in bond designing or qualification of the adhesive in areas that would normally be seen as high risk for standard epoxies, such as handrails and walkways.
For additional information, visit https://www.belzona.com/en/products/other/7311.aspx.
Images courtesy of Belzona Polymerics Ltd.
References:
- https://www.hse.gov.uk/welding/health-risks-welding.htm
2. ISO 17212:2012 Structural adhesives — Guidelines for the surface preparation of metals and plastics prior to adhesive bonding
3. ASTM D1062-08(2015) Standard Test Method for Cleavage Strength of Metal-to-Metal Adhesive Bonds
4. ASTM D1002-10(2019) Standard Test Method for Apparent Shear Strength of Single-Lap-Joint Adhesively Bonded Metal Specimens by Tension Loading (Metal-to-Metal)
5. ISO 9664:1993 Adhesives — Test methods for fatigue properties of structural adhesives in tensile shear
6. ASTM D256-10(2018) Standard Test Methods for Determining the Izod Pendulum Impact Resistance of Plastics