Adhesives play an important role in creating sustainable and resilient infrastructure. While the hybridization of adhesives is not a novel concept, recent innovations in raw materials have unlocked new possibilities for toughened epoxy systems. The reaction of a polyurethane segment into an epoxy polymer has proven to be successful in building and construction applications that require flexibility as well as resistance to temperature and solvents. This study shows that hybrid epoxy-urethane adhesives can achieve higher adhesive strength and faster cure than non-hybridized epoxy adhesives alone.
The North American markets for epoxy and polyurethane adhesives are $2.4 billion and $2.3 billion, respectively, across all industries, as estimated by The Adhesive and Sealant Council.1 Transportation applications make up approximately half of all epoxy adhesive volume, but epoxy adhesives are also often used in the assembly, building and construction, and do-it-yourself (DIY) spaces as well. Polyurethane adhesives are more diversified in their uses, as they can be found in packaging, woodworking, footwear, and leather applications, in addition to those mentioned for traditional epoxy materials. Recognizing the large market size and wide range of applications, it’s no surprise why someone would want to take advantage of both technologies’ strengths.
Both epoxy and polyurethane structural adhesives impart their unique properties to meet the requirements of the adhesive system in which they function. Epoxy adhesives are used in applications requiring rigidity, solvent resistance, and high-temperature resistance. They are, however, brittle because of their high crosslink density. Polyurethane adhesives are widely used in applications requiring toughness, processing flexibility, tunable cure rates, low-temperature cure, and adhesion to many different substrates. By combining the two chemistries, adhesive formulators can take advantage of their complementary properties to achieve a strong yet impact-resistant product.
Minimizing brittleness in epoxy formulations can be achieved through several strategies. One strategy involves creating a second phase in the epoxy matrix that interrupts crack propagation through the brittle epoxy matrix. A second involves the addition of reactive diluents or plasticizers to the epoxy resin.
In phase-separated, toughened epoxies, the second phase should be incompatible with the epoxy matrix and phase-separate uniformly during cure. It is also preferred that the second phase is reactive with epoxy resins so that the hard epoxy phase and the second phase are covalently bonded. In addition, the components should be compatible until polymerization, so that the resins can be stored without separating into layers. If the resins separate during storage, additional mixing will be required before application. The second phase may be formed from thermoplastic resins, high-molecular-weight flexible polyether amine resins, rubber particles, core-shell rubber particles, dispersed acrylic rubbers, epoxy functional fatty acids, nanoparticles, or amine-terminated butadiene acrylonitrile resins.
The strategy of reacting a polyurethane segment into an epoxy polymer has existed for many years and is widely used commercially in the coatings industry.2 This method of toughening is also used in commercial adhesive applications. The addition of a polyurethane segment into an epoxy adhesive by means of a blocked polyurethane prepolymer was tested and reported in the past.3 It was found that the addition of a polyurethane segment improves both adhesion and temperature resistance.
A newly developed low-viscosity blocked polyurethane prepolymer makes the adhesive easier to apply than epoxy adhesives toughened using earlier generation products. Unlike its predecessors, this product gives a low formulation viscosity while still providing commercial epoxy adhesives with improved lap shear strengths.
The novel blocked polyurethane prepolymer uses a bio-based blocking agent. The low viscosity allows for faster and easier handling of the product. The unconventional composition of this polymer, along with the special properties it imparts to the final adhesive, makes it attractive to those who want to reduce the brittleness of their epoxy.
Epoxy Chemistry
Epoxy reactions are characterized as the reaction of an epoxy resin and a curing agent (sometimes called a hardener). The epoxy functional resin is typically multifunctional and can vary in molecular weight. The reactive moiety is a three-member carbon-carbon-oxygen ring.
Curing agents are reacted with the epoxy resin. Curing agents are typically amines, alcohols, or carboxylic acids possessing an active hydrogen. In many two-component adhesives, the epoxy reaction is between an epoxy ring and an amine. The driving force for this reaction is the release of strain of the three-member ring.
Each primary amine can react with two epoxy moieties, so a diamine with two primary amines actually has a functionality of four. This high functionality leads to highly crosslinked polymers that are brittle. Vitrification can occur before the polymerization is complete, trapping unreacted end groups in the polymer matrix and lowering the molecular weight of the polymer. If this happens, the full development of physical properties is limited.
Blocked Polyurethane Prepolymers
Polyurethane prepolymers blocked with phenolic compounds react at room temperature with a strong primary amine to form a urea group (see Figure 1). As opposed to stoving compounds, for instance, heat is not required for a reaction to occur. The prepolymer reacts at room temperature, with the primary amine being substituted for the phenolic compound.
One blocked polyurethane group reacts with one primary amine to form a urea group. This leads to linear or low crosslink density polymers, providing a more flexible structure.
High- and Low-Viscosity Blocked Prepolymers
The properties of a high-viscosity blocked prepolymer (HVBPP) as an epoxy toughener were examined in a previous study.3 The Brookfield viscosity of the blocked prepolymer was measured to be approximately 148,000 cps (see Formulation G in Table 1). The viscosity of a novel low-viscosity blocked polyurethane prepolymer (LVBPP) was measured to be approximately 30,000 cps (Formulation N).
Blocked Polyurethane Prepolymers in Model Epoxy Compound
Increasing levels of a blocked polyurethane prepolymer were added to a simple epoxy resin to demonstrate the blocked prepolymers’ effect on properties. An epoxy resin was blended with increasing levels of either the HVBPP or the LVBPP. The viscosity of the mixture was measured for each formulation using a Brookfield viscometer (see Table 1). Since the viscosity was measured before the addition of amine, no reaction should have occurred.
The LVBPP formulations (Formulations I through N) did not show the large increase in viscosity of the epoxy resin mixture as seen in the analogous HVBPP formulations (Formulations B through G). This difference can be seen graphically (see Figure 2).
The LVBPP’s diminished effect on the viscosity increase of a formulation is advantageous for coating and adhesive formulators. Coating formulations will flow and level better, apply easier, and possess longer work times. The adhesive formulations will see better penetration of the resin into porous substrates than with formulations containing the HVBPP.
After mixing the blocked prepolymer into the epoxy, the amine was added to each formulation in Table 1. The gel times of each formulation were measured with a gel timer, and a sample of each resin was poured into a mold. The gel times and the physical properties of the cured blends were measured (see Table 1).
For both the LVBPP and HVBPP formulations, the gel time decreases with increasing levels of blocked prepolymer when epoxy resin was present, except Formulation M. As the level of blocked prepolymer increases, the level of released phenolic compound also increases. Phenolic compounds are known to act as catalysts for the epoxy reaction, and it is postulated that the phenolic compound acts as an internally released catalyst and catalyzes the epoxy reaction. Thus the gel time decreases as the blocked prepolymer content goes up, even though the functionality of the system is going down.
Interestingly, when either prepolymer was combined with the amine without an epoxy compound (Formulations G and N), the mixture reacted but with a longer gel time. The longer gel time was expected because the epoxy was not present to be catalyzed and the functionality of the system was low.
Physical property testing confirms that the blocked prepolymers increase the strength of the epoxy adhesive. The all-epoxy formulations, Formulations A and H, were too brittle to test for tensile properties and softening point. For the formulations containing blocked prepolymers, the tensile strength initially increased with increasing levels of blocked prepolymer content (see Formulations B and I). This was most likely the result of Formulations A and H vitrifying before the polymerization was complete.
The incorporation of 20% blocked polyurethane prepolymer in Formulations C and J allowed the polymerization to complete before vitrification occurred. These samples had the highest tensile strengths. After 20% blocked prepolymer, strength fell as the epoxy content decreased and the polyurethane content increased. Maximum elongation increased as the percentage of blocked prepolymer increased for both series of experiments.
The tear resistances of the formulations were tested, and the results confirm that the blocked prepolymers provide increased toughness. A tear resistance value was measured for the non-toughened epoxy Formulation H, but it was very low. For both series of experiments, the tear resistance increased as the level of toughener increased. Tear resistance reached a maximum with Formulations E and L. Tear resistance decreased in Formulations F and M as epoxy content decreased and the percentage of blocked prepolymer increased.
Adhesive Strength of Model Formulations
The lap shear adhesive strengths of the model formulations were determined on several substrates up to a prepolymer level of 35% (see Table 1). Increasing the level of HVBPP increased the lap shear strength on steel and on oak wood for all levels tested. In the LVBPP tests, lap shear strength increased on oak with increasing level of prepolymer. On steel, a 20% addition of LVBPP resulted in a significantly higher lap shear strength than a 20% addition of HVBPP.
Softening Point Determination of Model Adhesives
Heat resistances of the adhesive formulations were determined by a standard softening point experiment. The all-epoxy formulations broke when the weight was hung from the sample. Surprisingly, the addition of a small amount of block prepolymer increased the toughness of the adhesive so a softening point for the adhesive could be measured. Additional amounts of blocked prepolymer lowered the softening point of the adhesive (see Table 1).
Testing of Modified Commercial Epoxy Adhesives
In a previous article, it was reported that the addition of the HVBPP to commercial adhesives increased the strength and the softening point of the adhesive.3 These commercial epoxy adhesives were purchased at a home improvement warehouse. An appropriate amount of HVBPP and a stoichiometrically adjusted amount of diamine were added to each adhesive.
The lap shear strength of each adhesive was measured on steel, and the softening point temperature was measured on canvas. A 20% addition of the HVBPP increased the lap shear strength of the adhesive to over 1,500 psi (see Figure 3). Unexpectedly, the softening point of the epoxy adhesive increased with the addition of HVBPP.
These findings were confirmed with testing on a second commercial epoxy adhesive. Increasing the blocked prepolymer content to 20% improved the lap shear strength. Softening points were increased with the addition of the HVBPP at all concentrations (see Figure 3).
The LVBPP was also tested to confirm that it would provide benefit to a commercial epoxy adhesive. Several epoxy adhesives were purchased at a local hardware store.
As before, the LVBPP and a stoichiometric amount of diamine were added to each epoxy adhesive. With the first adhesive, the lap shear strength on steel increased when the level of LVBPP was increased to 10%, from approximately 2,180 psi to approximately 2,500 psi. The lap shear strength on oak wood also increased when the level of LVBPP was 10%. The lap shear strength went from approximately 990 psi to approximately 1,270 psi (see Figure 4)
A second commercial epoxy adhesive was tested. Lap shear strength on oak wood increased when 10% of the LVBPP was added to the epoxy adhesive (see Figure 5).
A third commercial epoxy adhesive was tested with the addition of the LVBPP. The addition of 10% of the LVBPP to the epoxy adhesive increased steel lap shear strength from approximately 2,750 psi to 2,800 psi. The lap shear strength on oak wood increased from 1,180 psi to 1,310 psi when 10% of the LVBPP was added to the epoxy adhesive.
A fourth commercial epoxy adhesive confirmed the results on wood. The oak lap shear adhesive strength increased from 1,410 psi to 1,580 psi on the addition of 10% LVBPP to the epoxy adhesive. The testing performed on wood clearly indicates that the lap shear strength can be increased by adding the LVBPP to a commercial epoxy adhesive.
Summary
A low-viscosity blocked prepolymer was developed to toughen epoxy resins. The use of an alternative bio-based blocking agent makes it a unique raw material for adhesive formulations. The low viscosity allows the product to be handled easier, making drum emptying more efficient. Unlike previous generations of tougheners, this prepolymer has a minimal effect on the viscosity of the epoxy/blocked prepolymer mixture.
Previous work showed that the physical properties of model compounds and commercial epoxy adhesives can be improved through the addition of a high-viscosity blocked polyurethane prepolymer. This study confirms that improved physical properties can also be achieved with a low-viscosity blocked polyurethane prepolymer. The adhesive strength of simple model epoxy formulations was improved with the low-viscosity blocked polyurethane prepolymer as well. It was demonstrated that the cure time of the model epoxy formulations decreased with the addition of the low-viscosity product.
Testing revealed that, in some cases, the low-viscosity toughener improved the metal lap shear strength of commercial epoxy adhesives. In all cases tested, the adhesion to wood was improved with the addition of the low-viscosity blocked prepolymer to a commercial epoxy adhesive. Overall, the new material shows comparable performance to previously available products and provides a unique advantage in lower viscosity of both the product and formulations made with it.
For additional information, call (412) 413-3983 or visit https://solutions.covestro.com.
Authors’ acknowledgement: Laboratory testing was performed by Adam Miller.
References
- The Adhesive and Sealant Council 2017-2020 North American Market Report, www.ascouncil.org/store/viewproduct.aspx?id=10934163.
- U.S. patent 4,753,826.
- Johnston, Jay A., “Toughening Epoxy Adhesives,” Adhesives & Sealants Industry, July 2013, pp. 14-17.
Watch our interview with Jay Johnston in this ASI Insider!
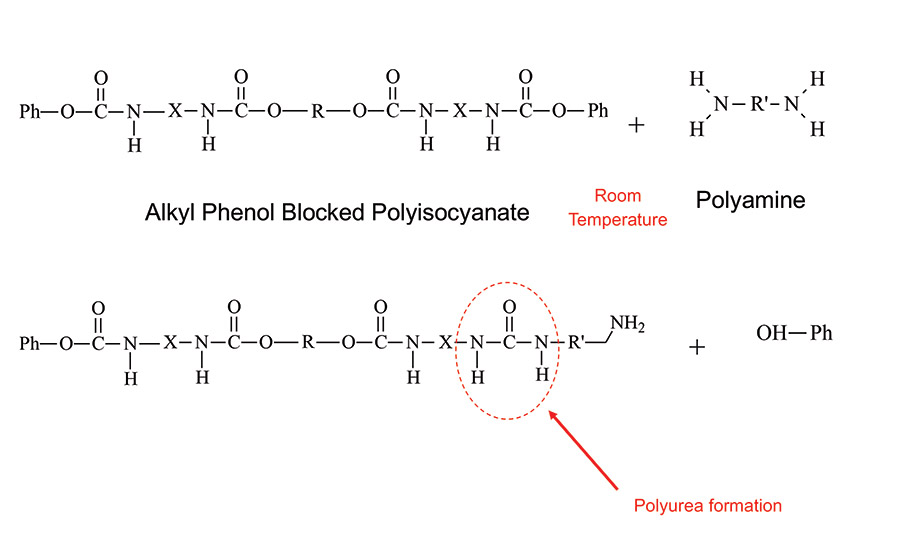