Starch- and dextrin-based adhesives play a large part in industrial production, especially the packaging industry. Starch and dextrin are principally used for bonding paper products. Most corrugated boxboard for making cartons is bonded with starch-based adhesives, and other porous substrates can be easily joined with these versatile adhesives.
Starch and dextrin adhesives are readily available, low in cost, and easy to apply from water dispersion. They are considered to be the least expensive class of paper-packaging adhesive. Formulated starch and dextrin adhesives can be applied hot or cold. These adhesives are generally supplied as powder and mixed with water prior to use to form a relatively thick paste. Starch and dextrin cure by the loss of moisture. Since these adhesives cure to a thermosetting structure, they have excellent heat resistance. Another significant advantage is their very slow curing rate, allowing ample assembly time. Disadvantages include poor moisture resistance and mold growth.
Although starch and dextrin have been used as adhesives for many decades, there are several important reasons why these natural adhesives will not be entirely replaced by synthetic products. The following advantages ensure that they will continue to fill particular niches in the marketplace.1
- Good availability
- Relatively low cost
- Stable quality
- Good adhesion to cellulose and many porous substrates
- Insoluble in oils and fats
- Non-toxic and biodegradable
- Heat resistant
This article will review the raw materials that go into starch and dextrin adhesives, the methods of adhesive manufacture, and the additives that are commonly used in formulations for improvement of specific properties. Finally, the common applications and formulations of starch- and dextrin-based adhesives will be reviewed.
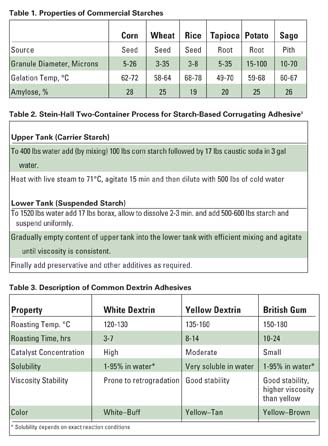
Raw Materials
Both starch and dextrin (dextrin is starch that is processed further) are considered carbohydrate polymers, and they come from basically the same sources. Starch is a natural polymer (a polysaccharide) derived from the seeds, roots and leaves of plants. Only a few plants yield starch in sufficient quantity to be economical: corn, wheat, potato, rice, tapioca and sago. The quality of the starch must be high to produce high-quality adhesives.
Starch is made up of two molecules: amylose and amylopectin. Amylose consists of long helical chains, and amylopectin has a branched structure. Starch does not have a uniform composition. Its molecular structure and amylase/amylopectin ratio vary according to plant source. Thus, processing characteristics and end properties will vary as well. The most important differences between starches are the molecular weight of the amylose fraction and the ratio of amylose to amylopectin.
While amylopectin can be supplied in cold-water-soluble form, amylose is insoluble. Amylose can be dissolved with strong alkali, by cooking with formaldehyde or by cooking in water at 150-160°C under pressure. Upon cooling or neutralization, such amylose dispersions will form firm gels at concentrations higher than 2% and will precipitate at concentrations lower than 2%. Amylose fractions are never truly soluble in water and in time will form crystalline aggregates by hydrogen bonding - a process known as retrogradation, or setback. Retrogradation is the cause of viscosity instability in certain starch-based adhesives. The amylopectin is more soluble and less prone to retrogradation. The percent of amylose in various starches and their resulting properties are summarized in Table 1.
Most starches contain 20-30% by weight of amylase, although certain specialty types can have as little as 0% or as high as 80%. Because of the amylose fraction, starch suspended in cold water is essentially unable to act as an adhesive because the starch is so tightly bound in crystalline regions. These granules must be opened through processing to obtain adhesive bonding.
Manufacture of Starch Adhesive
Heating in water is the simplest method of breaking up starch granules. On heating in water, starch granules first swell and then burst open with a resulting thickening of the suspension. The temperature at which this thickening of the suspension occurs is called the gelation temperature. For most starches in pure water, gelation occurs between 57 and 72°C (see Table 1). In this form, the starch is not a true solution but a colloidal suspension.
The heating process can take one of two forms. In the first, salts (usually the chlorides of metals such as calcium, magnesium and zinc) are added to a suspension of the starch in water, and the adhesive is produced by controlling temperature and the time of stirring. In the second and primary method, caustic soda is added to the starch suspension; the product is neutralized with acids later in the process.
The starch paste now has a high viscosity and acts as an adhesive. If the concentration of the starch is above 7%, then the cooked paste is very viscous and difficult to pump. Above 15% starch solids content, the cooked paste forms an immobile rubbery mass on cooling. Suspensions with a higher amylose/amylopectin ratio will have a higher viscosity.
Pregelation starch is produced by physical modification of the starch to impart the ability to form a paste easily in cold water. The process consists of heating the starch slurry to a temperature above the gelation temperature and then quickly drying the starch before retardation can occur. The main process equipment used is a heated-drum drier or hot roll.
Unmodified starches, such as those produced by the steps outlined previously, come in powder form (pregelation) or as high-viscosity, low-solids content pastes that do not show a stable viscosity with time. Therefore, several treatments have been developed to provide liquid adhesives that are not subject to retrogradation and have a viscosity and rheology more suitable for many applications. These treatment methods include alkali treatment, acid treatment and oxidation.
The gelation temperature can be lowered by the addition of an alkali, such as sodium hydroxide, to the starch suspension. If sufficient alkali is added, the starch can be induced to gel at room temperature.
Acid modification of starch is achieved by heating the starch at 49-54°C with small amounts of aqueous mineral acid, followed by neutralization with a base. This tends to make for a much thinner solution at the same solids content when compared to unmodified starch. Starches prepared in this manner are often known as thin-boiling or high-fluidity starches. Acid modification is often used when applications require higher solids content but a controlled, lower viscosity.
Oxidization of starch is usually obtained by treatment with aqueous alkaline hypochlorite. A starch suspension at pH 8-10 is treated with hypochlorite (5-10% Cl based on starch) for a long enough time to produce the desired viscosity. Acid is liberated during the reaction, so base must be added to maintain the pH for optimum reactivity. Dried oxidized starch is generally whiter than unmodified starch. Because of the low color, these starches are often used for the sizing and coating of printing papers. These oxidized or chlorinated starches behave similarly to acid-modified starches. However, the oxidized starch has greater tack and adhesive character and, thus, is often used in adhesive applications.
The Stein-Hall Process
The first major commercial process for producing starch adhesives was the Stein-Hall Process. This was introduced in the 1930s for the purpose of producing an adhesive for corrugated boxes.2 The Stein-Hall system combines the properties of an 8-9% cooked starch paste and a 25% starch slurry in a two-component, two-container process, as indicated in Table 2. Sodium hydroxide is used to lower the gelation temperature and borax is used to increase the tack. Crosslinkers and special starches may be used to impart water resistance.
The high-viscosity cooked starch paste serves as a carrier to prevent the starch granules in the slurry portion from settling out. When the adhesive is applied and heated to above its gelatinization temperature, the granules gelatinize, and a very viscous and tacky paste is produced. In corrugated box manufacturing, the suspended starch should gelatinize immediately on contact with the heated fluting rolls and develop instant tack at 60-70°C. Starch solids may range from 20-30%.
Single Container, or "No-Carrier," Process
This entire operation can also be carried out in a one-container system where there is no carrier portion of the adhesive. In this process, a solution of caustic soda is added to a slurry of starch to swell the starch granules uniformly until they reach the required adhesive viscosity. An acid is then added to stop this swelling process short of complete gelatinization, and borax is finally added.
When preparing such single-container adhesives, it is essential to carefully control the concentrations and temperature of the starch slurry and the caustic solution, and to stop the swelling at the correct stage to ensure that the required viscosity is achieved. Benefits of the single-container starch system include:
- Less heat required for bond formation (as the starch granules are already partially swollen)
- Less free water
- Viscosity allows increase in machine speeds and reduction in warped board production
- Superior storage and shear stability is allowed
Manufacture of Dextrin Adhesives
Dextrin adhesives are manufactured by dry-roasting starch in the presence of an acid catalyst. Through treatments with heat and acid, the starch molecules are hydrolyzed into small fragments, and then repolymerized into highly branched, readily soluble polymer molecules of moderate size. Cornstarch is commonly used because of its low cost and ready availability, although other starches are also used.
Unlike starch, dextrins are soluble in water. The severity of the heat and acid treatment determines the degree of solubility, which is the basis for classifying dextrins. Finished dextrins take a very fine powder form, varying in color from pure white to brown.
There are three main types of dextrin adhesives: white dextrins, canary (or yellow) dextrins and British gums. The differences are determined by the roasting time and the temperature and amount of catalyst used. Table 3 describes the properties of these dextrin adhesives.
British gums are dextrins with the highest molecular weight, and though they are the strongest adhesives among the dextrins, their maximum usable-solids content is only approximately 25%. Yellow dextrins are the lowest in molecular weight. Materials of this type are available with a viscosity of only 1700 cps at 60% concentration. White dextrins have the lowest color of the three, and their molecular weight is intermediate between those of the other two.
The range of solubilities of dextrin adhesives are advantageous in that they may be used to formulate a variety of solutions of very different viscosities, creating a variety of gel strengths. These formulations can then be further modified as described in the next section. The same additives and processes used for starch adhesives are generally used to formulate dextrin adhesives.
Dextrins are often preferable to starch, as they need less or no cooking and much less water to form the paste. This means that drying time is reduced and there is little likelihood of mold infection in warmer climates. As adhesives, dextrins are used in many of the same applications as starch adhesives. Dextrins are also used as a core binding material in the manufacture of foundry cores. Here, the main function is to provide good green strength and to prevent deformation of the core before being fired in the oven.
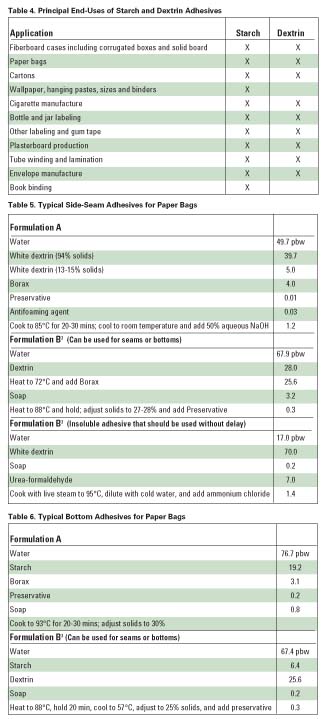
Additives and Modifiers
Properties of starch and dextrin adhesives that can be modified through formulation variables include: viscosity; solids content; stability; tack; slip; substrate penetration; drying rate; flexibility; water and fungus resistance; and cost. These formulations generally depend on the type of starch and modification as indicated above, as well as the additives used.
Frequently, dextrin adhesives—and sometimes starch-based adhesives—are formulated with borax (sodium tetraborate) to obtain high tack at moderate concentrations and viscosities with good aging characteristics. They also have good adhesion and machining properties. The borax is generally added in amounts of up to 10% based on dry starch. Sodium hydroxide is also added to convert the borax to the more active sodium metaborate. Applications include case sealing, carton sealing, bag seams, tube winding and laminating.
Plasticizers are widely used to control brittleness of the glue line and to regulate the speed of drying. Common plasticizers include glycerin, glycols, sorbitol, glucose and sugar. These types of plasticizers act as a hygroscopic agent to decrease the drying rate of the film. Plasticizers based on saps, polyglycols and sulfonated oil derivates lubricate the layers within the dried adhesive and, thus, impart flexibility. Urea, sodium nitrate, salicylic acid and formaldehyde plasticize by forming a solid solution with the dried adhesive.
Chemicals such as calcium chloride, urea, sodium nitrate, thiourea and guanidine salts are used as liquefiers to reduce viscosity. They are also used as humectants to control open time and speed of drying. They are usually added at about 5-20% based on dry starch. Colloid stabilizers, such as soaps and sodium chloride, are sometimes used to retard the tendency to retrogradation.
Native starches are capable of yielding high degrees of water resistance, which may be necessary for labeling, bill posting and other applications. Improved cold-water resistance can be obtained with polyvinyl alcohol or polyvinyl acetate blends. These adhesives will also dissolve in hot water, which is often a benefit. Optimal moisture resistance is obtained through the addition of thermosetting resins, such as urea formaldehyde or resorcinol formaldehyde.
Mineral fillers, such as kaolin clay, calcium carbonate and titanium dioxide, are often used in starch and dextrin adhesives to reduce cost and control penetration into porous substrates. They are usually used at concentrations of 5-50%. Thixotropic agents like bentonite are also often used in certain applications to control viscosity.
Other additives that are found in starch- and dextrin-based adhesives include preservatives, bleaches, and defoamers. Preservatives that are commonly used to prevent microbial activity include formaldehyde (35% solids) at 0.2-1.0%, copper sulfate at about 0.2%, zinc sulfate, benzoates, fluorides and phenols. Possible toxic effects must be carefully considered before choosing a preservative. Common bleaching agents include sodium bisulfite, hydrogen and sodium peroxide, and sodium perborate. Organic solvents are sometimes added to improve adhesion to waxed surfaces.
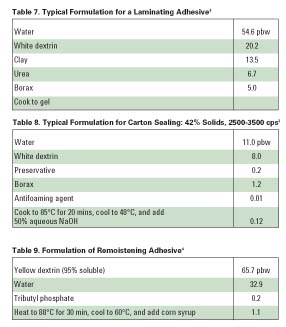
Common Applications and Formulations
The majority of starch and dextrin adhesives are used in the paper and textile industries. The principal end uses of starch and dextrin adhesive are shown in Table 4. Some of the most common applications for these adhesives are described below.
Most corrugated boxboard for making cartons is bonded with starch-based adhesives. A fraction of the starch needed to formulate the adhesive is gelatinized with aqueous caustic. This is blended with a concentrated suspension of unmodified starch granules (see Table 1). A typical starch-adhesive formulation also includes bentonite (used as a thixotroping agent), borax (to speed gelatinization), and a small quantity of preservatives (for use as a mold inhibitor). The paste is applied cold to the corrugated flutes and the liners. Upon subsequent exposure to heat, the starch granules swell and burst, forming a strong bond.
Starch-based adhesives are also commonly used in bag manufacturing. Normally, three adhesives are used in this application: seam, cross-pasting, and bottoming. In bag production, the paper is initially formed into a long tube with a side-seam adhesive. The viscosity and solids content of these adhesives are relatively low. They are generally made from highly soluble white dextrin or acid modified starch. The bottom adhesive is made from a more viscous paste, and it usually has greater tack. Bottom pastes are normally composed of white dextrins or starch. Typical formulations for seam and bottoming adhesives are shown in Tables 5-6. Cross-paste adhesives are used for the manufacture of multi-wall bags. In general, mineral fillers are added to this adhesive so it does not bleed through the paper.
Laminating adhesives must exhibit high tack, low permeation of the substrate and non-curling behavior. The adhesive must also meet the requirements of the laminating equipment. White dextrin is often used in this application. A typical formulation is shown in Table 7. Sugar, sodium nitrate or urea is often added at 30-50% of the dextrin to increase solids and to control open time. Foil laminations require resin-based adhesive for adhesion and water resistance. And while alkaline-starch types provide excellent adhesion to aluminum foil and good heat resistance, they also demonstrate poor water resistance.
Today, most paperboard cartons are sealed with liquid glues or hot-melt adhesives. These are generally preferred because of their high speed of operation and ability to bond securely to many different substrates. However, dextrin adhesives are used in certain applications where low cost must be achieved. Carton-sealing adhesives require a low and stable viscosity, and they must set quickly. A formulation for a white dextrin adhesive for carton sealing is provided in Table 8.
Adhesives for tapes, envelopes, labels and similar applications require noncurling ability, and they should be nonblocking under humid conditions. Certain tape and label adhesives also must be capable of rewetting or remoistening. This generally requires that the formulation contain acid-modified starch or high-soluble white and yellow dextrins to allow high-solids contents. A formulation for a remoistening adhesive that is often used for envelopes is given in Table 9.
To prevent curling, several processes have been used. In one process, the tape or label substrate with dried adhesive is run over a bar to produce microcracks in the adhesive layer. Another process uses a solvent deposition of the adhesive where a cold-water-soluble dextrin is suspended in an organic solvent. When this suspension is applied to paper and dries, it leaves behind discrete particles of adhesive, which will swell and produce the required tack on contact with water.
Dextrins and converted starches are often used for bonding labels. In bottle labeling, high-solids starch-based jelly gums represent tacky, slow-drying, humidity-resistant adhesives. They exhibit good adhesion to polyethylene and treated polypropylene. Dextrin formulations are used where high concentration and speed are required.
For more information, visit http://www.specialchem4adhesives.com.
References
- Lazarus, D.M. "Adhesives Based on Starch," Ch. 10, Adhesives and Adhesion, Vol. 7, K.W. Allen, ed., Applied Science, London: 1983.
- Bauer, I.V. U.S. Patents 2,051,025 (1936), 2,102,937 (1937), 2,212,557 (1940).
- Jarowenko, W. "Starch Based Adhesives," Ch. 12, Handbook of Adhesives, van Nostrand Reinhold, New York: 1977.
- Baumann, M.G.D.; Conner, A.H. Ch. 22, "Carbohydrate Polymers as Adhesives," Handbook of Adhesive Technology, 2nd ed., A. Pizzi and K.L. Mittal, Marcel Dekker, New York: 2003.